Bearings: Basic Concepts and Design Applications
Bearings are essential mechanical components widely used in various industries to reduce friction and facilitate smooth motion between moving parts. By supporting rotating or moving shafts, bearings enable machines to operate efficiently and with minimal wear. Bearings come in numerous types, each designed for specific applications based on load, speed, and environmental conditions. Understanding their basic concepts and design applications is key to ensuring optimal machine performance and longevity.
Basic Concepts of Bearings
1. What is a Bearing?
A bearing is a machine element that allows constrained relative motion, typically rotational or linear. Bearings are designed to minimize friction and wear between moving parts by providing a smooth, controlled surface for contact. They support the load, absorb forces, and enable rotational or linear motion to occur with minimal energy loss.
2. Types of Bearings
Bearings can be classified based on their design and the type of motion they support. The most common types include:
- Ball Bearings: These are the most common type of rolling bearings, consisting of steel balls or other spherical elements that reduce friction between the inner and outer races. Ball bearings are used in various applications where moderate loads and high-speed operations are required.
- Roller Bearings: Similar to ball bearings, roller bearings use cylindrical rollers instead of balls. They are better suited for supporting heavier radial loads and are commonly used in industrial machinery, such as conveyors and motors.
- Thrust Bearings: Designed to support axial loads (parallel to the shaft), thrust bearings can be either ball or roller types. These are typically used in automotive applications, such as transmissions or heavy machinery.
- Plain Bearings (Sleeve Bearings): These bearings have a simple design without rolling elements, often used in low-speed applications where space is limited, or cost is a primary concern. Plain bearings can handle high loads but generate more friction compared to rolling element bearings.
- Magnetic Bearings: These bearings use magnetic fields to support a rotating object without physical contact. They are used in applications requiring ultra-precise motion and are often found in high-speed, high-precision machinery, such as turbines or MRI machines.
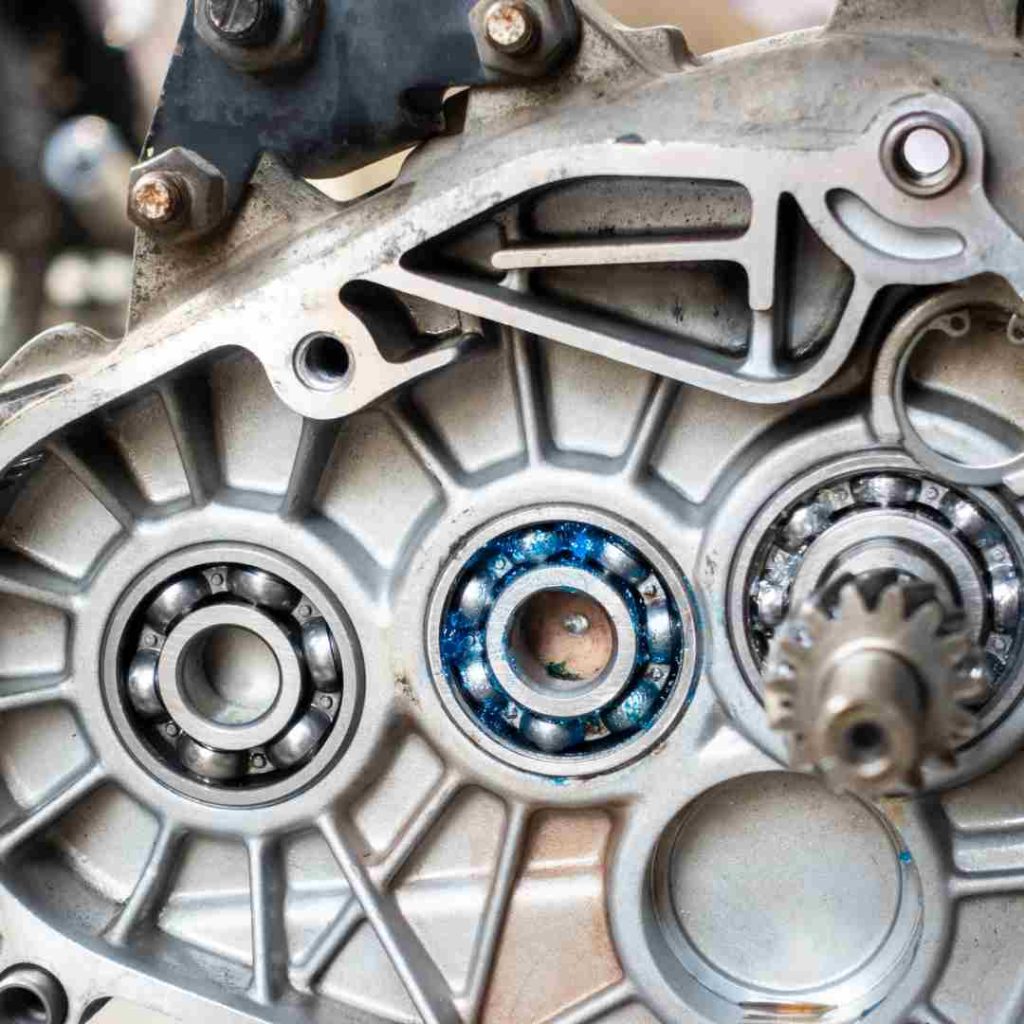
Design Considerations for Bearings
The design of a bearing depends on several factors, including the type of load, speed, accuracy requirements, and environmental conditions. Some of the critical design elements include:
1. Load Capacity
Bearings must be designed to handle the expected loads without failure. The two main types of loads bearings handle are:
- Radial Loads: Perpendicular to the shaft.
- Axial Loads: Parallel to the shaft.
Designing for load capacity involves choosing the correct bearing type and material, as well as ensuring that the bearing’s geometry is appropriate for the application.
2. Speed and Efficiency
The bearing’s speed capability depends on factors such as lubrication, materials, and design. High-speed bearings are designed to minimize friction and heat generation. Ball bearings are commonly used in high-speed applications because of their low friction and efficient design.
3. Lubrication
Proper lubrication is critical to bearing performance. Bearings can be lubricated using grease or oil, which reduces friction, prevents wear, and ensures smooth operation. For high-speed applications, special lubricants are used to maintain performance while reducing energy loss.
4. Materials
Bearings are made from various materials depending on their application and load requirements:
- Steel: The most common material used for bearings due to its high strength and wear resistance.
- Ceramics: Used in high-speed or high-temperature applications, ceramics reduce friction and wear even further than steel.
- Plastic Bearings: In low-load or corrosive environments, plastic bearings may be used to reduce cost and weight.
5. Sealing and Protection
Bearings often require seals to protect them from dirt, moisture, and other contaminants that could lead to premature wear. Seals can be integrated into the bearing design or installed separately.
Applications of Bearings
Bearings are found in almost every industrial application, from small household appliances to large-scale machinery. Some of the most common applications include:
1. Automotive Industry
In vehicles, bearings are used in the engine, transmission, wheels, and steering systems. Wheel bearings, for example, allow the wheels to rotate smoothly with minimal friction, which is essential for efficient fuel consumption and handling. Thrust bearings are used in the transmission system to manage axial loads during gear changes.
2. Aerospace
Bearings are essential in aircraft for reducing friction in engine components, landing gear, and control surfaces. These bearings must meet strict performance standards, as failure in any bearing could lead to catastrophic consequences.
3. Industrial Machinery
Bearings are used extensively in industrial applications, including motors, conveyors, and heavy machinery. Roller bearings are particularly useful in large-scale machinery where heavy radial loads need to be supported, while high-precision bearings are used in equipment that requires low friction and smooth motion.
4. Electric Motors
Bearings are essential components in electric motors. In this application, bearings help to support the rotating shaft, ensuring that it moves smoothly and efficiently. For small motors, ball bearings are typically used, while larger motors might require roller or thrust bearings depending on the load.
5. Consumer Electronics
In products like computer hard drives, printers, and fans, bearings ensure that components like hard drive platters and cooling fans spin smoothly, contributing to the overall performance and longevity of the device.
6. Wind Turbines
Bearings are used in wind turbine generators to support the rotor and reduce friction in the system. These bearings must withstand high loads and harsh environmental conditions, so they are often made from high-performance materials and require regular maintenance.
Conclusion
Bearings are indispensable components in modern engineering, enabling machines and equipment to function efficiently and reliably. By understanding the basic principles of bearing types, design considerations, and applications, engineers can select the most appropriate bearings for specific tasks, ensuring long-lasting performance and minimizing maintenance needs. As technology advances, new bearing materials, designs, and technologies will continue to shape industries and improve the performance of machinery worldwide.