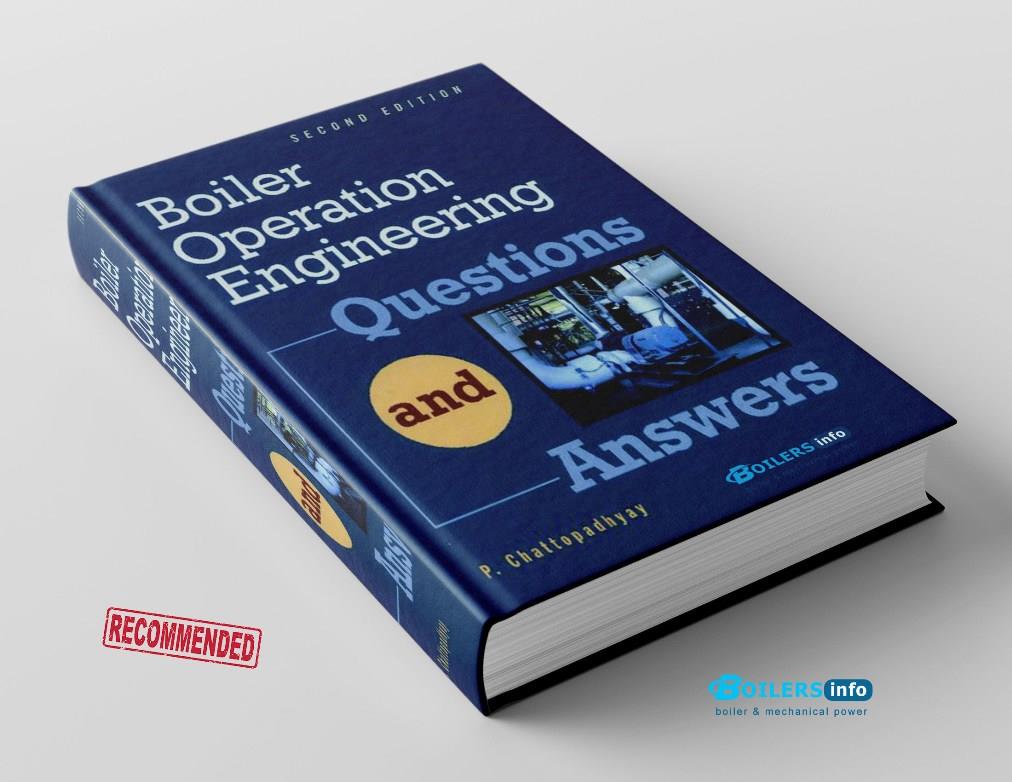
Boiler operation engineering questions and answers pdf by chattopadhyay best book I ever read. Recommended from boilers info for all boiler engineers and power plant professionals. you must read this book. almost every topic of boiler engineering is included.
Boilers are integral components in many industries, particularly in power generation, where they are used to convert chemical energy into thermal energy for steam production. Optimizing boiler operation is essential for improving efficiency, reducing emissions, and ensuring long-term reliability. This article explores key topics in boiler operation engineering, including upgrading PC-fired boilers, low NOx burners, emissions control, cooling water treatment, reverse osmosis, and condition monitoring techniques.
Comprehensive Guide to Boiler Operation and Engineering
Boilers are critical components in power plants, industrial processes, and heating systems. They convert energy from fuel into steam or hot water, which is used for power generation, heating, or various industrial processes. To ensure their efficiency and longevity, understanding their design, operation, maintenance, and the technologies used to optimize performance is essential. This guide delves into various aspects of boiler operation and engineering, from fundamental concepts to advanced technologies.
1. Introduction to Boilers
A boiler is a closed vessel in which water or another fluid is heated to produce steam or hot water. Boilers are classified based on their design, fuel type, and operating conditions. They are widely used in power generation, heating applications, and industrial processes.
2. High-Pressure Boilers
High-pressure boilers are used in power plants and other industrial applications where steam at high pressure is needed for efficient heat transfer and energy generation. These boilers operate at pressures above 80 bars and can reach temperatures in the range of 540-600°C.
3. Boiler Auxiliaries
Boiler auxiliaries are the components that support the operation of the boiler. These include feed pumps, air preheaters, soot blowers, and fans, which ensure optimal operation and efficiency by providing fuel, air, and other necessary conditions.
4. Boiler Mountings and Accessories
Boiler mountings are safety devices installed on the boiler to ensure its safe operation. These include pressure gauges, safety valves, and water level indicators. Accessories, like economizers and air heaters, enhance the efficiency of the boiler.
5. Boiler Operation Inspection and Maintenance
Routine inspection and maintenance are vital to prevent boiler breakdowns, ensure efficiency, and extend the service life of the equipment. This includes checking the pressure relief valves, water treatment systems, and combustion controls.
6. Boiler Calculations
Boiler calculations involve determining key operational parameters such as steam generation rate, efficiency, fuel consumption, and heat transfer. These calculations help in optimizing performance and ensuring compliance with safety and regulatory standards.
7. Draught
Draught is the pressure difference between the boiler and the atmosphere, created by the exhaust fans or natural buoyancy, which is necessary for the combustion process. Proper draught ensures optimal air supply to the burner and effective flue gas removal.
8. Primary Fuels
Primary fuels for boilers include coal, natural gas, oil, and biomass. The choice of fuel depends on factors such as availability, cost, and the type of boiler system.
9. Principles of Combustion
Combustion is the process of burning fuel in the presence of air (oxygen) to produce heat. The efficiency of combustion directly impacts boiler performance and emissions. Proper fuel-air mixing, temperature control, and sufficient oxygen supply are key to achieving efficient combustion.
10. The Chemistry of Combustion
Combustion involves the chemical reaction between a fuel and oxygen to produce heat, carbon dioxide (CO2), water vapor, and other byproducts. The efficiency and emissions of combustion depend on factors like the fuel’s chemical composition and the combustion temperature.
11. Coal Pulverization
Coal pulverization is the process of grinding coal into fine particles to improve combustion efficiency. Pulverized coal-fired boilers require finely ground coal to ensure complete combustion and maximize heat transfer.
12. Pulverized Coal Fired Furnaces
Pulverized coal-fired furnaces are the most common type of boiler for coal-based power generation. These furnaces burn finely ground coal in a high-temperature environment to generate steam, which drives turbines to produce electricity.
13. Upgrading PC-Fired Boilers
Upgrading Pulverized Coal (PC)-fired boilers focuses on improving combustion efficiency, reducing emissions, and increasing the reliability and lifespan of the equipment. This can include retrofitting low-NOx burners, improving combustion controls, and enhancing air and fuel mixing.
14. Fuel Oil and Gas Fired Furnaces
Boilers fired with fuel oil or natural gas are more flexible in terms of operation and have lower emissions compared to coal-fired units. They are commonly used in industrial settings and for backup power generation.
15. Low NOx Burners
Low NOx burners are designed to minimize the formation of nitrogen oxides (NOx), a harmful pollutant produced during combustion. These burners achieve this by controlling the combustion temperature and air-to-fuel ratio.
16. Emissions Control
Emissions control systems are employed to reduce the release of harmful gases, such as NOx, SOx, and particulate matter, from boilers. Technologies such as selective catalytic reduction (SCR), flue gas desulfurization (FGD), and electrostatic precipitators (ESPs) help meet environmental standards.
17. Dust Collection
Dust collection systems, such as bag filters or electrostatic precipitators, capture particulate matter from flue gases before they are released into the atmosphere. This helps to minimize air pollution and improve plant efficiency.
18. Ash Handling System
Ash handling systems are essential for collecting and transporting ash produced during combustion in coal and biomass boilers. These systems ensure that ash is properly disposed of or utilized in other processes, reducing environmental impact.
19. Carryover, Scale, and Sludge
Carryover refers to the unintentional transfer of water droplets or solids from the boiler into the steam system. Scale and sludge buildup can clog the system, reducing heat transfer efficiency and causing corrosion. Regular water treatment and maintenance are necessary to prevent these issues.
20. Steam Contamination and Its Control
Steam contamination, including the presence of dissolved solids and chemicals, can harm turbines and other components. Proper water treatment and monitoring of steam quality are essential to prevent damage and maintain efficient operation.
21. Prevention of Deposit Formation in Boiler Units
Deposits such as scale and soot can form on boiler surfaces, reducing heat transfer and increasing fuel consumption. Regular cleaning, water treatment, and the use of anti-fouling agents help prevent these deposits.
22. Characteristics of Steam-Water Flow
The flow of steam and water through the boiler system is governed by thermodynamic principles. Understanding the behavior of steam-water mixtures is essential for controlling pressure, temperature, and flow rates to ensure safe and efficient operation.
23. Temperature Conditions and Heat Transfer
Temperature control is critical for the efficient operation of boilers. Heat transfer mechanisms, including conduction, convection, and radiation, play a vital role in transferring heat from the combustion gases to the water or steam in the boiler.
24. Hydrodynamics of Closed Hydraulic Systems
Closed hydraulic systems in boilers, such as those in feedwater systems, require careful management of fluid dynamics to maintain pressure and flow rates, ensuring the stability and performance of the system.
25. Deaeration and Deoxygenation
Deaeration removes dissolved gases like oxygen from feedwater, preventing corrosion in the boiler. Deoxygenation is typically achieved through chemical treatment or physical methods like vacuum deaeration.
26. Cooling Water Treatment and Cooling Towers
Cooling water treatment ensures that the water used in cooling systems does not cause scaling, corrosion, or biological growth. Cooling towers are used to cool water before it is recirculated, playing a crucial role in maintaining the efficiency of the plant.
27. Water Treatment and Demineralization
Water treatment processes, including demineralization, remove impurities from the feedwater to prevent corrosion, scaling, and fouling in the boiler. Demineralized water is used to ensure the production of high-quality steam.
28. Reverse Osmosis
Reverse osmosis is a filtration process used in water treatment to remove dissolved salts, minerals, and impurities, producing high-purity water for use in boilers and other systems.
29. Scaling of Fireside of Heating Surfaces
Scaling on heating surfaces reduces heat transfer efficiency and increases fuel consumption. Regular cleaning, water treatment, and proper combustion control help to minimize scaling.
30. Corrosion of Waterside Heating Surfaces
Corrosion on the waterside of heating surfaces can lead to pitting, material degradation, and failure. Effective water treatment and the use of corrosion inhibitors are essential to prevent these issues.
31. Corrosion of Fireside Heating Surfaces
Fireside corrosion, often caused by high temperatures and the presence of acidic gases in flue gases, can damage the boiler’s heating surfaces. Regular inspection and maintenance are required to detect and mitigate fireside corrosion.
32. Evaporators
Evaporators are used in boilers to convert water into steam by adding heat. Their efficiency is crucial for achieving high steam quality and ensuring safe operation.
33. Superheaters
Superheaters increase the temperature of steam beyond its boiling point to maximize energy extraction in turbines. Proper design and material selection are necessary to avoid overheating and damage.
34. Economizers and Air Heaters
Economizers and air heaters capture waste heat from flue gases to preheat the feedwater and combustion air, respectively. These systems enhance overall boiler efficiency by recovering energy that would otherwise be wasted.
35. Steam Condensers
Steam condensers convert exhaust steam from turbines back into water. They play a crucial role in maintaining the efficiency of the steam cycle and reducing energy loss.
36. Steam Turbines
Steam turbines convert thermal energy into mechanical energy, driving generators to produce electricity. The efficiency of steam turbines is directly impacted by the quality of steam and the condition of the boiler.
37. Cycles for Steam Power Plants
Steam power plants typically operate on Rankine or regenerative Rankine cycles. These cycles are designed to maximize thermal efficiency by optimizing steam generation, expansion, and condensation processes.
38. Boiler Design
Boiler design involves selecting appropriate materials, sizing components, and ensuring proper heat transfer. Advanced designs optimize efficiency, emissions, and reliability.
39. Nuclear Steam Generators
In nuclear power plants, steam generators convert heat produced by nuclear reactions into steam. They require special materials and safety features to handle high radiation levels and extreme conditions.
40. Energy from Waste
Energy-from-waste plants convert municipal and industrial waste into energy through combustion or gasification. These plants are crucial for reducing landfill waste while generating power.
41. NDE and Condition Monitoring
Non-destructive examination (NDE) and condition monitoring techniques, such as ultrasonic testing and vibration analysis, are used to assess the health of boiler components and predict maintenance needs, reducing unplanned downtime and improving safety.