This procedure defines the requirement and procedure of hydrostatic testing of the boiler pressure parts after completing the assembly of all the boiler high pressure and temperature components.
Hydrostatic testing Objective
Hydrostatic testing in the boiler is carried out to check the following:
- Leakages in the boiler pressure parts (Tubes, headers and Pipes).
- To test the soundness of welded joints and associated pressure parts of the boiler in order to comply the code requirements.
- To prove the strength of the boiler pressure parts at a pressure greater than the working pressure of the boiler at ambient temperature.
The hydraulic test of the boiler is carried out at the following conditions / situations.
- On completion of the boiler erection activities
- On completion of repair work on boiler pressure parts
- On completion of annual overhaul
- At the request of statutory authority to fulfill the statutory requirements.
New Boiler ready for hydro-static test
Preparation for Boiler Hydrostatic test:
The following activities have to be completed before carrying out the boiler hydraulic test.
• Ensure that the complete boiler Pressure part erection is completed.
• Ensure that all welding/NDT and heat treatment activities are completed.
• Ensure that necessary pressure parts welding are completed as per the drawing.
• Ensure that pressure parts welding joints are free from paint & rust
• Ensure that, all the buck stays, its guides and anchors are installed as per the drawings. (Check and confirm the clearance provided in the guides and anchors are strictly as per the drawing).
• Ensure that all the boiler permanent supports, structural bracings are provided as per the drawings.
• Ensure that all temporary supports provided for erection supports are removed.
• Ensure that, all tools; equipment and loose items have been removed from the drums and manifolds.
• Ensure that, steam drum, man holes and manifolds inspection caps are properly joined and tightly sealed.
• Ensure that, the constant load hangers are locked in position with locking pin and the spring loaded hangers are locked.
• Ensure that the Boiler filling arrangements are ready.
• Ensure that Hydrostatic testing pump is available.
• Ensure that Power supply to the pressure raising pump should be available.
• Ensure the DM water quality & availability as per requirement. (Minimum three (3) times of the boiler water holding capacity shall be readily available).
• Ensure that, minimum two set of spare gaskets for the drum and boiler important gaskets must be available ready.
• Ensure that proper lighting, approach platforms and communication systems, are ready.
• Ensure that, the following temporary arrangements are completed for conducting a hydraulic test.
• Temporary piping connection from pressure pump discharge to hydro test connection point in the Boiler.
• Boiler filling line to be made ready from existing DM fill pump station for Boiler filling.
• Ensure that, all the temporary piping’s are adequately supported.
• Ensure that minimum three (3) numbers of calibrated pressure gauges are fitted at the identified locations (One in the steam drum, one in the steam outlet header and the other at the outlet of the hydraulic pump).
• Ensure that, the dial pressure gauge used in the testing shall have dials graduated over the entire range of the hydro test pressure.
• It is preferable to have calibrated pressure gauge size greater than 200mm.
• Ensure proper and adequate man power is available during the test.
• Ensure that, the drum internals are not fitted inside the steam drum.
Boiler Filling Operation for Hydrostatic testing
- Ensure that the following valves are closed.
• Root valves of all instruments.
• Chemical dosing line valves
• CBD and IBD Valves
• All header and pipe drain valves
• Soot blowing system and sample cooler system isolation valves.
- Ensure that, the following valves are opened.
• Hydro test connection valve
• Filling line valve
• Drum vent valve
• Hydro test pressure indicator isolating valves
• Super heater vent valve
- Ensure that, the following DM water quality is maintained.
• PH between 8.5- 10.5.
• The water quality shall be as per contract with supplier.
• DM water temperature should be maintained between minimum 21 °C to maximum 50°C.
• The DM water and the metal temperature of the pressure parts should be above the ambient air dew point to prevent condensate formation on the pressure parts being tested, which interfaces with the detection of small leaks.
• Open the filling line valve and start filling the boiler through low point drains.
• Continue the filling until the water starts corning out through all the air vents of boiler drum and super heater headers. Ensure air is released completely.
• Do not weld any pressure parts or attachments to the pressure parts, with water inside tubes.
• Once the boiler is completely filled, close all the air vents, when water starts coming out freely without air bubbles, and stop the filling pump and isolate the filling pump from the boiler.
Carry out inspection in the designated areas. If leaks are observed at this stage, the water level must be lowered on Boiler and emptied as necessary to attend the leakages. After attending the leakage’s the procedure for filling the boiler shall be repeated. Open the hydro test connection isolating valve and put pressure pump on line.
Pressurization and Inspection
If all the condition is satisfactory start the pressurizing pump by keeping the discharge pressure relief valve open and ensure no person inside the furnace. While raising the pressure, the identified test team should go around the boiler for inspection. Once the Boiler pressure is raised to 10 kg/ cm2 (g) stop the pump and observe the pressure drop.
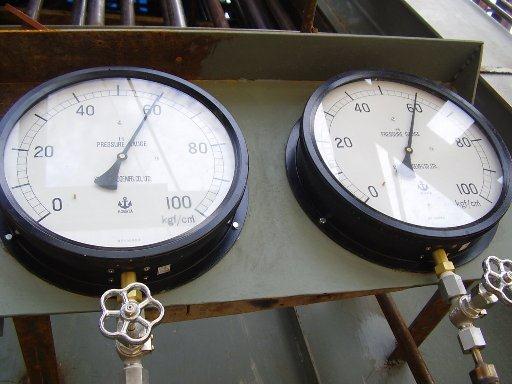
If no leakage is observed to the satisfaction of the inspecting personnel, start the pressurizing pump. Raise the pressure gradually to 25% of the hydro test pressure and repeat the above steps. Similarly do it for 50% and 75% of the hydro test pressure. When the pressure reaches the hydro-test pressure, stop the pressurizing pump and observe the pressure drop for 30 minutes and identified test team should inspect the boiler thoroughly to check for any leakage or sweating. Ensure that the test pressure never exceeds more than 6% of required pressure. If any leakage is identified it is to be attended after draining the water and repeat the hydro test as mentioned above. If no leak is observed release the -boiler; for further work. Reduce the boiler pressure gradually by crack opening drain valves till the boiler is 2 kg/ cm2 (g) and then open all the vent valves.
Hydrostatic testing safety precautions
For pendent type (Non drainable) superheaters, necessary precautions are taken to avoid corrosion. DM water with oxygen scavenger added to 300ppm and PH not more than 9.5 to be used. This may then be left filled after the test. In case of welded safety valves, remove the hydro test plug and re-install the normal safety valve seat, after de-pressurizing and draining the boiler. In case of flanged safety valves, remove the blind flange and refit the valves. Re-install the instruments that have been sealed off for the test. The drained water shall never be used. Boiler shall always be filled with treated water as specified in the contract. Filling the boiler with un-treated water will cause internal damage and corrosion of pressure parts.
[bws_pdfprint]