Benchmarking Best Practices in Maintenance Management
Effective maintenance management is a cornerstone of operational excellence in any industry. By benchmarking best practices, organizations can identify areas for improvement, enhance efficiency, and achieve world-class performance. This guide explores the essential chapters in achieving excellence through benchmarking in maintenance management.
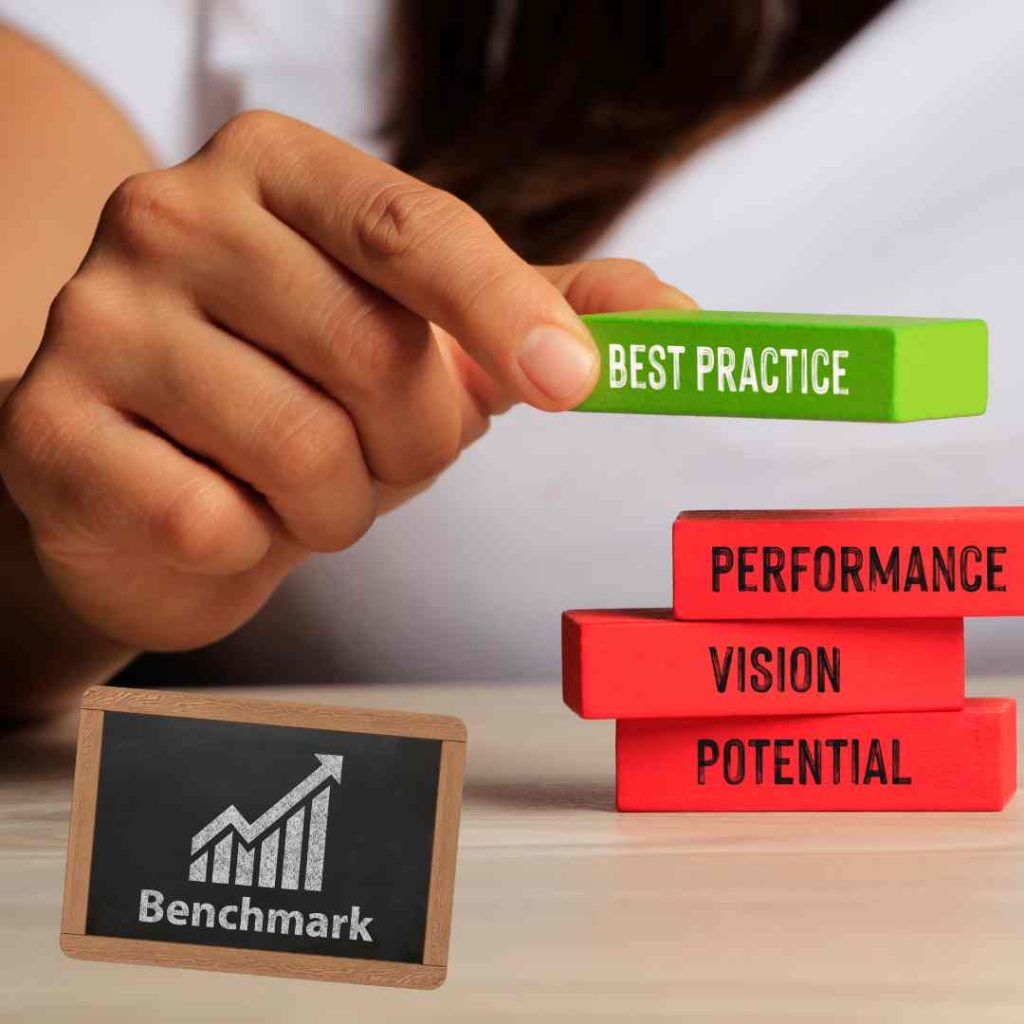
Table of Contents
ToggleAnalyzing Maintenance Management
Analyzing maintenance management serves as the foundation for building a robust and efficient system. It begins with evaluating current practices, processes, and outcomes to understand the organization’s strengths and weaknesses. Key performance indicators (KPIs), such as mean time between failures (MTBF) and mean time to repair (MTTR), are essential metrics for establishing a baseline. Conducting a gap analysis helps identify discrepancies between current performance and industry standards, paving the way for targeted improvements. This thorough assessment enables organizations to prioritize resources, focus on critical areas, and lay the groundwork for implementing best practices.
Benchmarking Fundamentals
Benchmarking is a systematic approach to comparing an organization’s maintenance performance and processes with those of industry leaders or peers. It serves as a catalyst for improvement by identifying areas where changes can yield significant benefits. Benchmarking can be internal, external, or functional, depending on the focus of the comparison. The process involves defining the scope, collecting data, and analyzing the findings to develop actionable strategies. The key is to understand what makes industry leaders successful and adapt those strategies to fit the organization’s context. Effective benchmarking not only drives innovation but also fosters a culture of continuous improvement, aligning maintenance objectives with overarching business goals.
Maintenance Organizations
The structure of a maintenance organization is critical to its success. A well-organized team ensures efficient workflows, clear accountability, and optimal resource allocation. Maintenance structures can be centralized, decentralized, or a hybrid of both. Centralized systems promote uniformity in decision-making, while decentralized setups provide flexibility at local levels. Hybrid models strike a balance by combining strategic oversight with operational independence. Clearly defined roles and responsibilities—such as planners, technicians, and managers—prevent overlap and ensure that tasks are executed efficiently. Regular performance evaluations and the use of KPIs allow organizations to track team effectiveness and identify areas for skill development or structural adjustments.
Maintenance Training
Training is the backbone of any successful maintenance organization. Skilled personnel are more effective in diagnosing issues, executing repairs, and adhering to safety standards. Comprehensive training programs should cover technical skills, such as equipment-specific knowledge, alongside soft skills like teamwork and communication. Safety training is equally vital, ensuring compliance with regulations and reducing workplace accidents. Organizations should encourage continuous learning and certifications, such as the Certified Maintenance and Reliability Professional (CMRP), to keep employees updated on best practices and emerging technologies. By investing in training, companies not only improve operational efficiency but also foster employee satisfaction and retention.
Work Order Systems
A well-designed work order system is indispensable for organizing and tracking maintenance activities. It provides a structured approach for submitting, approving, and executing maintenance tasks. Modern Computerized Maintenance Management Systems (CMMS) have revolutionized work order management by automating processes, reducing paperwork, and improving traceability. These systems allow teams to prioritize tasks, allocate resources, and monitor progress in real-time. Clear documentation of completed work orders helps in analyzing trends, identifying recurring issues, and planning future maintenance activities. An effective work order system enhances communication between departments, minimizes downtime, and ensures that maintenance tasks are completed efficiently and accurately.
Maintenance Planning and Scheduling
Maintenance planning and scheduling are essential for optimizing resources and minimizing disruptions. Planning involves defining the scope of work, estimating costs, and allocating the necessary tools and personnel. Scheduling prioritizes these tasks, ensuring they are executed in a timely and orderly manner without conflicting with other operations. Advanced CMMS tools facilitate automated scheduling and reminders, helping teams stay on track. Proper planning and scheduling reduce the occurrence of emergency repairs, extend equipment life, and improve overall productivity. By addressing both short-term needs and long-term goals, organizations can ensure a balanced approach to maintenance management that aligns with their operational objectives.
Preventive Maintenance
Preventive maintenance (PM) involves routine inspections and servicing to prevent equipment failure.
- PM Programs:
- Schedule regular checks based on equipment specifications.
- Use predictive analytics to anticipate potential issues.
- Tools and Techniques:
- Condition Monitoring: Use sensors and IoT devices for real-time data.
- Checklists: Standardized procedures for inspections and servicing.
- Benefits of PM: Increases asset lifespan, reduces downtime, and lowers repair costs.
Maintenance Inventory and Purchasing
Efficient inventory and purchasing systems are critical for ensuring the availability of spare parts and tools.
- Inventory Management:
- Maintain optimal stock levels to prevent shortages or overstocking.
- Use inventory management software to track usage and reorder levels.
- Purchasing Practices:
- Develop relationships with reliable suppliers.
- Negotiate contracts for cost-effective procurement.
Management Reporting and Analysis
Accurate reporting and analysis provide insights for informed decision-making.
- Key Reports:
- Asset performance reports (e.g., uptime/downtime analysis).
- Cost analysis reports (e.g., labor, materials, and overhead).
- Safety compliance reports.
- Dashboards and Analytics: Use CMMS dashboards for real-time performance monitoring and predictive analytics for future planning.
- Decision-Making: Leverage insights from reports to optimize processes, allocate resources, and improve overall performance.
World-Class Maintenance Management
Achieving world-class maintenance management involves implementing strategies and practices that drive operational excellence and maximize the value derived from assets. This level of management is characterized by a proactive approach that prioritizes predictive and preventive maintenance over reactive methods. Organizations striving for world-class standards adopt advanced technologies, such as artificial intelligence (AI), the Internet of Things (IoT), and big data analytics, to monitor equipment health in real-time and predict potential failures. Sustainability is also a hallmark of world-class maintenance, with a focus on energy-efficient practices and minimizing environmental impact. Additionally, these organizations foster a culture of excellence by aligning maintenance goals with broader organizational objectives, promoting accountability, and encouraging continuous improvement. By integrating innovation, strategic alignment, and best practices, world-class maintenance management not only enhances equipment reliability but also contributes to overall business success and competitiveness in the industry.
Conclusion
Benchmarking best practices in maintenance management is a dynamic process that drives continuous improvement and operational excellence. By analyzing current practices, integrating cutting-edge technologies, and learning from industry leaders, organizations can achieve world-class performance. Maintenance management is not just about maintaining equipment—it’s about creating a strategic advantage that enhances productivity, safety, and profitability.