Introduction
HVAC chillers are a critical component in commercial and industrial cooling systems, playing a pivotal role in maintaining indoor comfort and equipment functionality. Due to their high energy consumption and central role in facility operations, optimizing their performance is essential. This manual outlines best practices in the selection, operation, and maintenance of chillers to ensure efficiency, longevity, and cost-effectiveness.
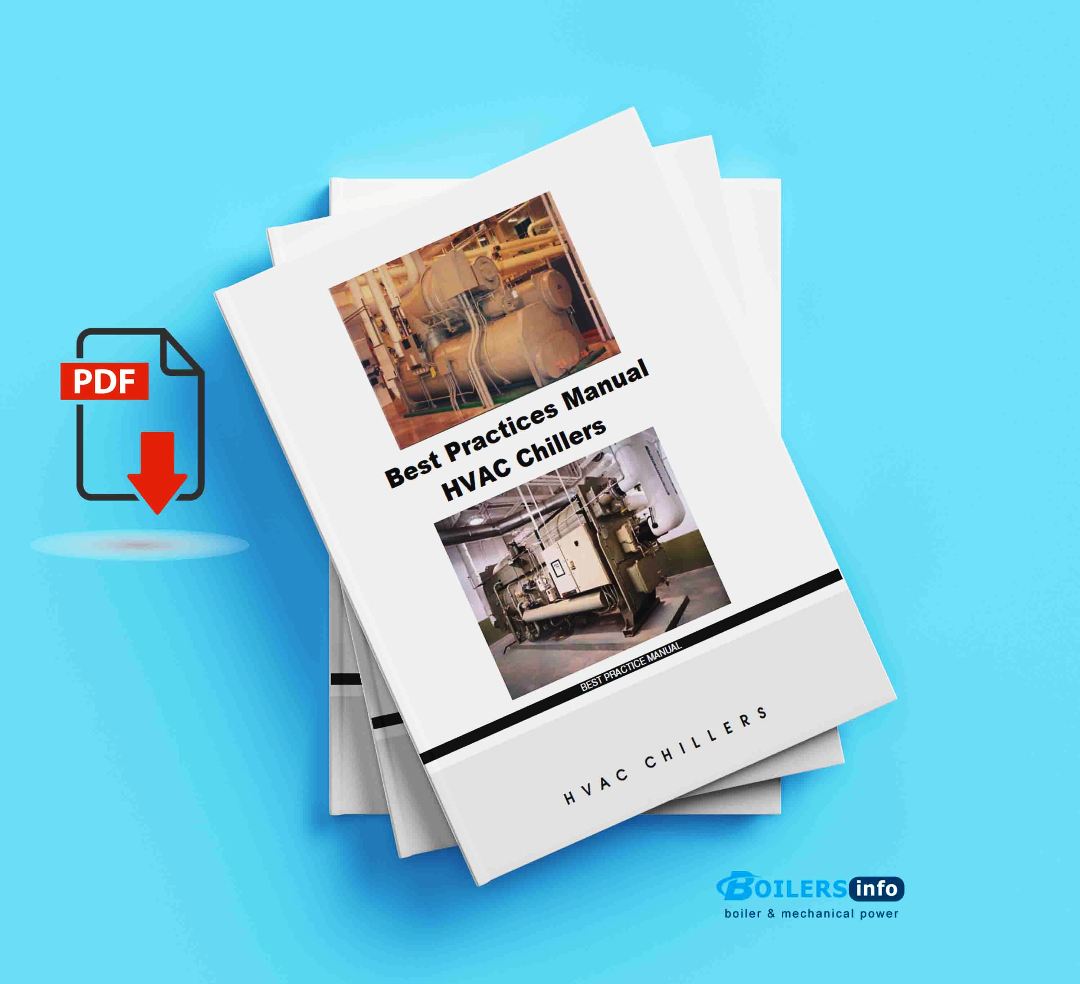
1. Chiller Selection and Design Considerations
a. Load Analysis
-
Conduct a thorough cooling load analysis to avoid oversizing.
-
Use historical data or simulation tools to predict peak and partial loads.
b. Chiller Type Selection
-
Air-Cooled Chillers are ideal for smaller systems or areas with water scarcity.
-
Water-Cooled Chillers offer higher efficiency and are suitable for larger, continuous load applications.
c. Efficiency Ratings
-
Choose chillers with high full-load and part-load efficiency ratings (e.g., IPLV, COP).
-
Look for ENERGY STAR or equivalent certifications.
2. System Design Optimization
a. Variable Speed Drives (VSDs)
-
Use VSDs on compressors, pumps, and fans to match system demand dynamically.
b. Proper Piping Layout
-
Design piping to avoid air traps and ensure laminar flow.
-
Use variable primary flow design to reduce pumping energy.
c. Thermal Storage Integration
-
Incorporate thermal storage where peak demand charges are high or where load profiles vary significantly.
3. Installation Best Practices
-
Ensure proper vibration isolation and acoustic treatment.
-
Use high-quality insulation on all cold surfaces to prevent energy losses.
-
Validate flow rates and pressures during commissioning to match design specs.
4. Efficient Operation
a. Optimize Chilled Water Setpoint
-
Adjust setpoints based on actual space loads and external conditions.
-
Use reset strategies to improve energy savings during part-load operation.
b. Monitor and Manage Load
-
Avoid short-cycling by maintaining a consistent load.
-
Use Building Management Systems (BMS) or Energy Management Systems (EMS) for real-time monitoring.
c. Sequencing Multiple Chillers
-
Operate chillers in optimal sequence (base-loading the most efficient unit).
-
Implement automatic staging based on load requirements.
5. Maintenance and Reliability
a. Regular Preventive Maintenance
-
Clean condenser and evaporator tubes periodically.
-
Inspect refrigerant levels and test for leaks.
-
Replace filters and monitor water treatment to prevent scaling.
b. Condition-Based Monitoring
-
Use sensors to track temperature, flow, pressure, and vibration.
-
Analyze trends to predict failures before they occur.
c. Water Treatment Program
-
Maintain water chemistry to avoid corrosion, scale, and biological growth.
-
Consider side-stream filtration and UV treatment for additional protection.
6. Performance Monitoring and Benchmarking
-
Establish baseline performance metrics (e.g., kW/ton).
-
Use energy dashboards or automated reporting tools to track efficiency.
-
Conduct periodic energy audits and tune-ups.
7. Environmental and Regulatory Compliance
-
Ensure compliance with refrigerant handling regulations (e.g., EPA 608 in the U.S.).
-
Choose low-GWP refrigerants where possible.
-
Implement leak detection and recovery systems.
Conclusion and Book Download
Implementing best practices for HVAC chillers enhances energy efficiency, reduces operational costs, and extends equipment lifespan. With a focus on smart design, precise control, and proactive maintenance, facilities can significantly improve performance and sustainability.