A case study in mechanical engineering is a detailed analysis of a real-world engineering problem, project, or system. It involves investigating how mechanical engineering principles are applied to design, analyze, and improve mechanical systems. Case studies are often used in education, research, and industry to understand engineering challenges and solutions.
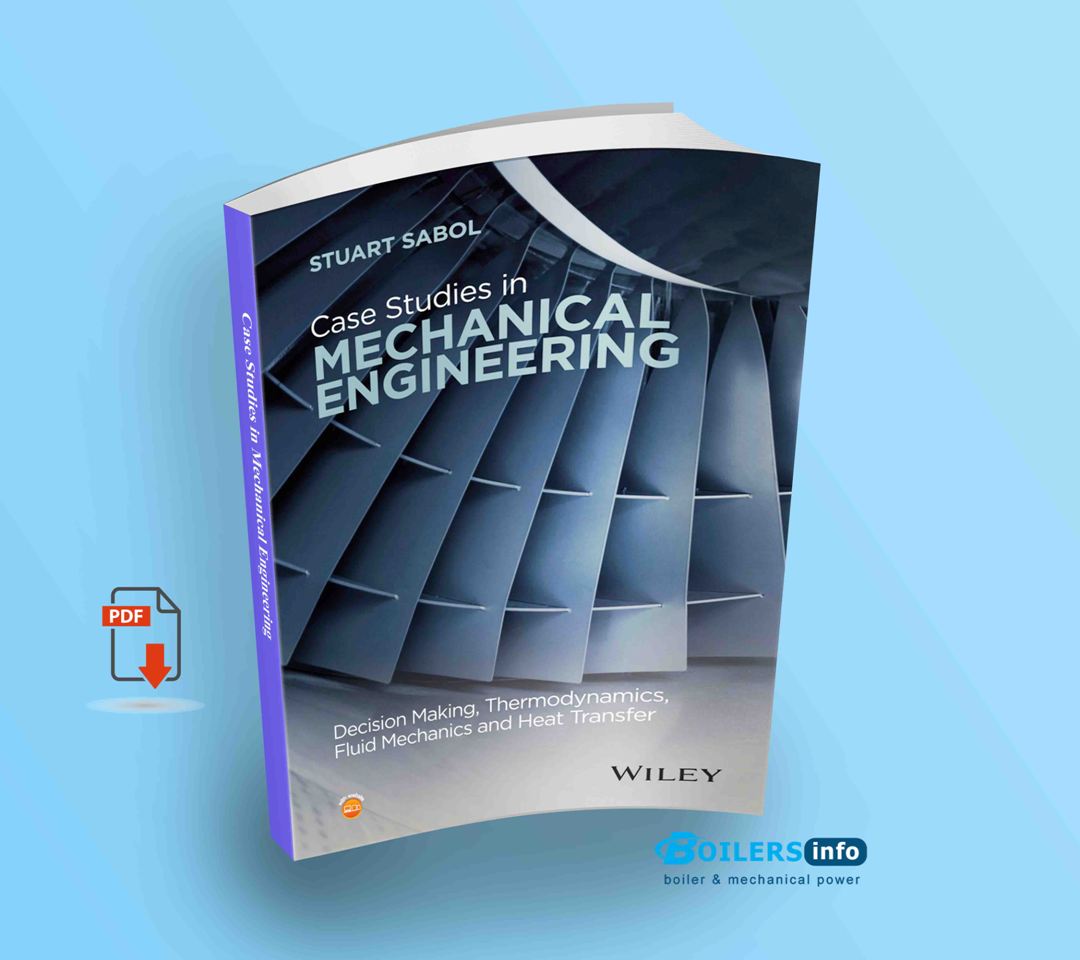
Key Elements of a Mechanical Engineering Case Study
- Problem Definition – Clearly state the engineering challenge or issue.
- Background Information – Provide details about the system, industry, or scenario.
- Analysis & Methodology – Describe the engineering principles, calculations, simulations, or experiments used.
- Solution & Implementation – Explain how the problem was solved, including design improvements, material selection, or process modifications.
- Results & Discussion – Present performance improvements, cost-benefit analysis, or efficiency gains.
- Conclusion & Lessons Learned – Summarize findings and recommendations for future work.
Examples of Mechanical Engineering Case Studies
- Failure Analysis of a Turbine Blade – Investigating cracks in turbine blades to improve material selection.
- Optimization of Heat Exchangers – Enhancing efficiency in a power plant using computational fluid dynamics (CFD).
- Design of an Automated Assembly Line – Implementing robotics to improve manufacturing efficiency.
- Aerodynamic Analysis of a Formula 1 Car – Using wind tunnel testing and CFD to improve vehicle performance.
- Welding Process Improvement in Heavy Industries – Optimizing welding parameters to reduce defects and increase strength.
Case Study: Failure of a Turbine Blade
Introduction
Mechanical engineers often study real-world problems to find better solutions. One common issue in power plants and jet engines is the failure of turbine blades. This case study explores why a turbine blade failed and how engineers solved the problem.
Problem Statement
A power plant reported damage to a turbine blade. The blade had cracks and signs of wear, leading to reduced efficiency and a risk of breakdown.
Investigation
Engineers examined the damaged blade using:
- Visual Inspection – Noting cracks and material wear.
- Material Testing – Checking for weaknesses in the metal.
- Stress Analysis – Using computer simulations to see how forces affected the blade.
Findings
The investigation showed that:
- High temperatures caused thermal stress, leading to cracks.
- The blade material had small defects, making it weaker.
- Vibrations during operation worsened the damage over time.
Solution
To prevent future failures, engineers took these steps:
- Used a better heat-resistant material for the blades.
- Improved cooling techniques to reduce temperature stress.
- Adjusted blade design to handle vibrations more effectively.
Conclusion and Book
This case study highlights how mechanical engineers analyze failures and improve designs. By solving this issue, the power plant improved efficiency, reduced downtime, and increased the lifespan of turbine blades. read more