Engineering Metrology and Measurements
Engineering metrology and measurements play a crucial role in ensuring the accuracy, reliability, and functionality of manufactured components. By employing precise measurement tools and techniques, engineers can verify that parts meet specified dimensions and tolerances, ensuring smooth assembly and optimal performance. Below is a detailed exploration of key areas in engineering metrology, with examples and use cases.
Table of Contents
ToggleLimits, Fits, and Tolerances
Limits, fits, and tolerances are foundational concepts in metrology, crucial for ensuring that mating parts function together as intended.
- Limits define the acceptable range for a dimension (e.g., a shaft’s diameter might have limits of 49.95 mm to 50.05 mm).
- Fits describe the relationship between assembled parts, such as clearance fits (for loose movement), interference fits (for press-fit assemblies), and transition fits (for balanced assemblies).
- Tolerances set the permissible deviation from the nominal dimension to balance precision and manufacturing cost.
Use Case: In the manufacturing of automobile engines, crankshafts and bearings must have precise interference fits to avoid excessive vibration or operational failure. Tolerance stacks are carefully analyzed to ensure parts align correctly without compromising functionality.
Linear Measurement
Linear measurement focuses on evaluating straight-line dimensions like length, width, and height using precise tools. Common instruments include vernier calipers, micrometers, and coordinate measuring machines (CMMs) for intricate geometries.
Use Case: In aerospace manufacturing, components like turbine blades must meet stringent dimensional tolerances. CMMs are widely used to measure the intricate profiles and ensure uniformity across production batches. This guarantees that all blades perform efficiently under high-speed and high-temperature conditions.
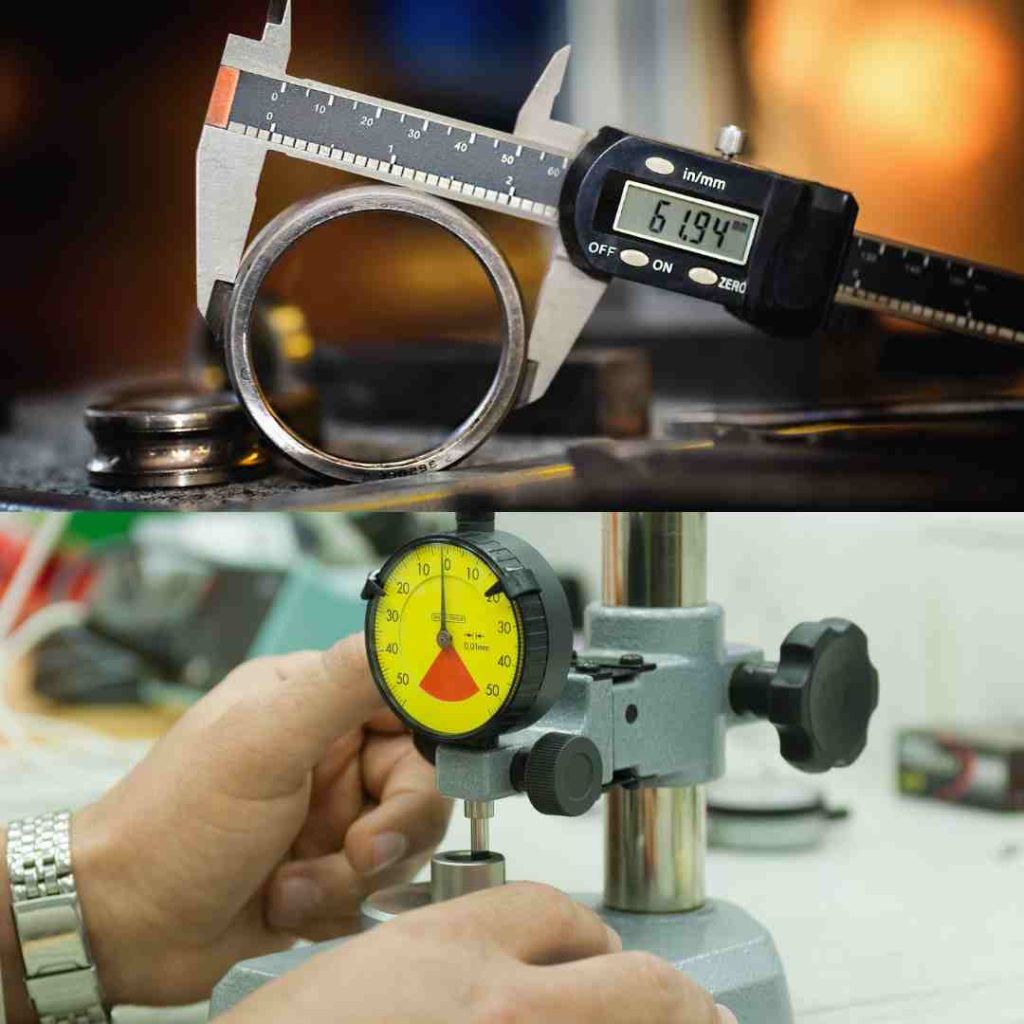
Angular Measurement
Angular measurement ensures precise control over angles, which is critical in parts like bevel gears or turbines. Instruments such as sine bars, bevel protractors, and autocollimators are commonly used.
Use Case: During the production of bevel gears for power transmission, even slight angular deviations can result in improper meshing and noise during operation. Autocollimators are often used to measure angular deviations with sub-arcsecond precision, ensuring optimal gear performance.
Optical Measurement and Interferometry
Optical methods provide non-contact measurement techniques that are especially valuable for delicate or highly polished components. Interferometry uses the interference of light waves to measure dimensions and surface profiles with nanometer precision, while optical comparators magnify parts for visual inspection.
Use Case: In semiconductor manufacturing, interferometry is used to inspect the flatness of silicon wafers. A flat surface is essential for uniform deposition of layers, ensuring the performance and reliability of microchips.
Comparators
Comparators are precision instruments that compare a dimension to a standard. Dial comparators and electronic comparators allow quick checks against tolerance limits without needing complex calculations.
Use Case: In the production of piston rings, electronic comparators are used to verify diameters and ensure they fit snugly into engine cylinders. Any deviation could lead to engine inefficiency or excessive wear.
Metrology of Gears and Screw Threads
Accurate measurement of gears and screw threads ensures they meet functional requirements like smooth operation and load transmission. Gear metrology involves checking parameters such as pitch, profile, and lead. Similarly, screw thread metrology assesses pitch diameter and thread angles.
Use Case: In wind turbine gearboxes, gear profile errors can cause energy loss and noise. Gear testers ensure these components meet design specifications, enhancing efficiency and reliability in power generation. For screw threads, precision is critical in medical devices like bone screws, where even minor inaccuracies can affect surgical outcomes.
Metrology of Surface Finish
Surface finish affects friction, wear, and aesthetics, making its measurement crucial in industries like automotive and aerospace. Instruments like stylus profilometers and optical scanners measure surface roughness and waviness.
Use Case: In automotive engine manufacturing, the surface finish of cylinder bores affects lubrication and sealing performance. Stylus instruments are used to ensure the roughness values fall within optimal ranges, improving engine efficiency and lifespan.
Conclusion
Engineering metrology and measurements are vital for maintaining quality and precision in manufacturing processes. Whether ensuring the tight tolerances of mating parts, verifying angular alignment in critical assemblies, or assessing surface finish for optimal functionality, metrology underpins modern engineering excellence. By applying these techniques with advanced tools and technologies, industries can achieve superior product performance and reliability across applications.