🔥 Heat Exchanger Design Handbook: Essential Guide for Engineers
Introduction to Heat Exchangers
Heat exchangers (HX) are crucial components in many industrial processes, including power generation, chemical processing, HVAC systems, refrigeration, oil and gas, and food industries. They facilitate the transfer of heat between two or more fluids without direct contact. The efficiency, reliability, and safety of a system often depend on the proper design and selection of the heat exchanger.
This article provides a comprehensive overview of heat exchanger design principles, types, key design considerations, and common challenges.
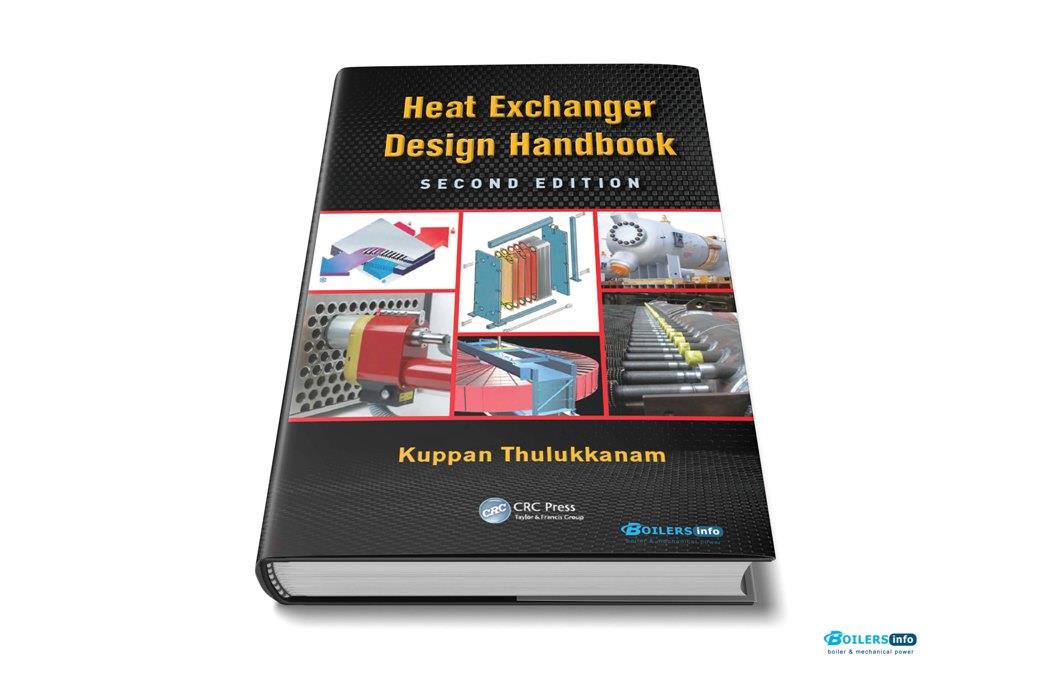
Types of Heat Exchangers
The first step in heat exchanger design is selecting the appropriate type based on the application, fluid properties, and heat duty. Common types include:
🔹 Shell and Tube Heat Exchanger (STHE)
- Consists of a series of tubes housed within a shell.
- Ideal for high-pressure and high-temperature applications.
- Common in power plants and oil refineries.
🔹 Plate Heat Exchanger (PHE)
- Made up of multiple thin plates stacked together.
- Compact, high heat transfer efficiency, but lower pressure resistance.
- Common in HVAC, food processing, and pharmaceutical industries.
🔹 Air Cooled Heat Exchanger (ACHE)
- Uses air as the cooling medium.
- Suitable for remote or offshore applications where water is scarce.
🔹 Double Pipe Heat Exchanger
- Simple design with one pipe inside another.
- Suitable for small-scale or low heat duty processes.
Basic Design Principles
1️⃣ Heat Transfer Calculation
The fundamental design of a heat exchanger revolves around the amount of heat to be transferred. This is calculated using:
Q=U×A×ΔTmQ = U \times A \times \Delta T_m
Where:
- Q = Heat duty (W)
- U = Overall heat transfer coefficient (W/m²·K)
- A = Heat transfer area (m²)
- ΔTₘ = Log Mean Temperature Difference (LMTD)
2️⃣ Flow Arrangement
- Counter-flow: Fluids move in opposite directions. Highest efficiency.
- Parallel-flow: Fluids move in the same direction.
- Cross-flow: Fluids cross each other at right angles.
3️⃣ Material Selection
Material must resist corrosion, erosion, and thermal stress. Common materials:
- Stainless steel
- Copper alloys
- Titanium
- Carbon steel
Key Design Considerations
✅ Thermal Design:
Calculate required surface area, select heat exchanger type, and determine flow configuration.
✅ Mechanical Design:
Design for pressure ratings, mechanical stresses, and compliance with standards (ASME, TEMA).
✅ Hydraulic Design:
Ensure correct flow velocities to avoid erosion, vibration, or fouling.
✅ Cost and Maintenance:
Balance initial cost with operating efficiency and ease of maintenance.
Challenges in Heat Exchanger Design
⚠ Fouling:
Deposition of unwanted materials reduces efficiency. Proper material choice and cleaning systems are vital.
⚠ Corrosion:
Fluid properties may cause material degradation. Use corrosion-resistant alloys.
⚠ Thermal Stress:
Temperature fluctuations can cause fatigue. Allowances must be made in design.
Heat Exchanger Design Software Tools
- HTRI (Heat Transfer Research Inc.)
- Aspen HYSYS
- CHEMCAD
- ANSYS Fluent (for CFD analysis)
These tools help automate complex calculations, simulations, and optimization of heat exchanger designs.
Conclusion
Heat exchanger design is a multidisciplinary task that involves thermodynamics, fluid dynamics, materials science, and mechanical design. By carefully considering process requirements, thermal duties, material selection, and mechanical constraints, engineers can develop efficient, reliable, and cost-effective heat exchangers.
Whether you’re dealing with a simple plate heat exchanger or a complex multi-pass shell-and-tube system, following best practices in design ensures safe and efficient operation.
👉 Downloadable Heat Exchanger Design Handbook (PDF)
📘 Includes formulas, selection charts, case studies, and real-world examples.
Available upon request.