Practical Industrial Safety Risk Assessment
Risk assessment is a critical component of industrial safety management. It involves identifying potential hazards in the workplace, assessing the likelihood and severity of accidents or incidents, and implementing measures to control or mitigate those risks. A practical industrial safety risk assessment is essential to ensure that the working environment remains safe for employees, minimizes potential losses, and complies with regulatory standards.
What is a Safety Risk Assessment?
A safety risk assessment is a systematic process that identifies hazards, evaluates the risks associated with them, and determines control measures to minimize or eliminate these risks. It is a proactive approach that helps organizations understand safety risks before they lead to incidents, injuries, or fatalities.
The primary objectives of a safety risk assessment are:
- Hazard Identification: Identifying physical, chemical, ergonomic, and psychosocial hazards that could harm employees.
- Risk Evaluation: Analyzing the potential consequences of each hazard and the likelihood of their occurrence.
- Risk Control: Implementing controls or measures to mitigate or eliminate the identified risks.
Key Steps in Conducting a Safety Risk Assessment
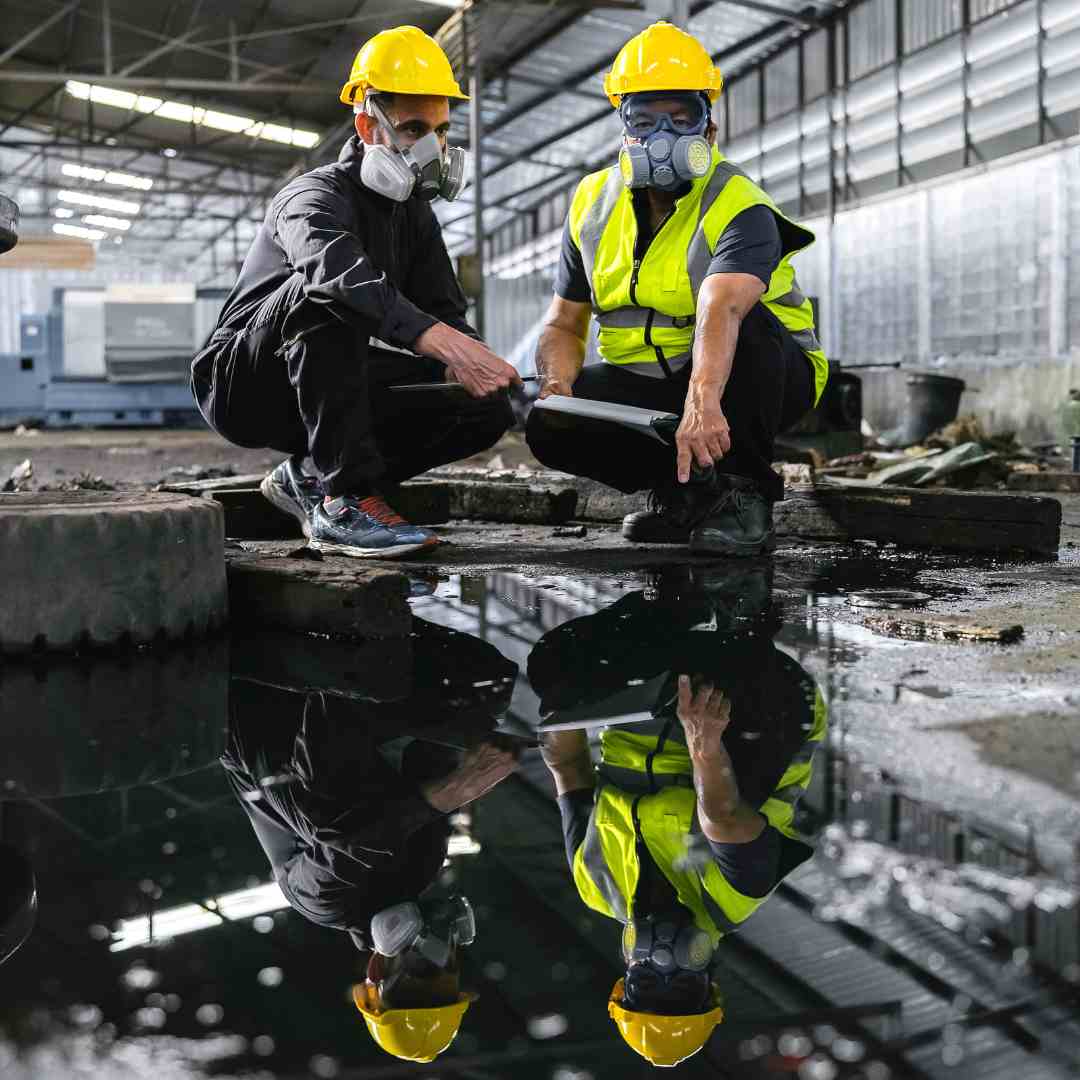
1. Hazard Identification
The first step is identifying potential hazards in the workplace. This can involve reviewing historical incident data, observing work processes, and consulting with employees who have direct experience with specific tasks. Common hazards include:
- Physical Hazards: Machines, tools, noise, and vibrations.
- Chemical Hazards: Exposure to toxic substances, gases, or fumes.
- Ergonomic Hazards: Poor workstation design, repetitive tasks, and manual handling.
- Psychosocial Hazards: Stress, harassment, and workplace violence.
Example: In a manufacturing plant, a potential hazard could be the moving parts of a machine that could cause entanglement or crushing injuries.
2. Risk Evaluation
After identifying the hazards, the next step is to evaluate the associated risks. This involves considering the likelihood of the hazard occurring and the potential consequences. Risk evaluation often uses a risk matrix that classifies risks as low, moderate, or high based on:
- Likelihood: The chance that the hazard will lead to an accident.
- Severity: The potential impact or consequences if the hazard were to cause an incident.
Example: A risk assessment of a machine with exposed rotating parts may show a high likelihood of injury if safety guards are not in place, and the severity of an accident could be severe (e.g., amputations or fractures).
3. Risk Control Measures
Once risks are evaluated, risk control measures must be implemented to prevent or mitigate the identified hazards. These control measures are typically based on the hierarchy of controls:
- Elimination: Remove the hazard from the workplace.
- Substitution: Replace the hazard with something less dangerous (e.g., using less harmful chemicals).
- Engineering Controls: Use physical means, such as machine guards or ventilation systems, to isolate workers from hazards.
- Administrative Controls: Implement work practices or procedures, such as job rotation or training, to reduce exposure to hazards.
- Personal Protective Equipment (PPE): Use equipment such as helmets, gloves, or eye protection to reduce the risk to workers.
Example: For the rotating parts hazard, an engineering control would be installing machine guards, and administrative controls would involve worker training on the importance of never bypassing safety devices.
4. Implementation and Monitoring
Once controls are in place, it’s essential to ensure that they are functioning correctly. This involves continuous monitoring of safety protocols, performing regular inspections, and encouraging employee participation in safety initiatives. Additionally, organizations should conduct periodic reviews of the risk assessments to ensure they remain up-to-date with any changes in work processes, equipment, or regulatory standards.
Example: Regular checks to ensure machine guards are in place and that no workers are bypassing safety systems would help maintain a safe environment.
5. Documentation and Reporting
All aspects of the risk assessment process must be thoroughly documented. This includes hazard identification, risk evaluations, control measures, and monitoring efforts. Documentation not only provides a record of safety practices but also serves as evidence in case of audits, inspections, or investigations.
Example: In the event of an accident, documented risk assessments and control measures can demonstrate that reasonable precautions were taken to prevent the incident.
Benefits of a Safety Risk Assessment
Improved Safety: By identifying and controlling hazards, risk assessments prevent accidents and injuries, leading to a safer work environment.
Legal Compliance: Regulatory bodies require organizations to perform risk assessments to comply with workplace safety laws. Adhering to these guidelines ensures that businesses avoid penalties and legal issues.
Increased Productivity: Safe workplaces reduce the number of disruptions caused by accidents, injuries, or illnesses, leading to higher employee morale and productivity.
Cost Savings: Preventing accidents and mitigating risks reduces medical costs, insurance premiums, and legal fees, ultimately saving the company money.
Employee Engagement: Involving workers in the risk assessment process helps them become more aware of safety issues, leading to a more safety-conscious culture.
Real-World Example of a Safety Risk Assessment
In a chemical manufacturing plant, a comprehensive safety risk assessment might be conducted to address the potential hazards associated with the handling of flammable chemicals. The assessment would identify hazards such as chemical spills, leaks, or exposure to harmful fumes. The risk evaluation could indicate that a spill could have a high likelihood and a severe consequence, resulting in fire or toxic exposure.
To mitigate this risk, control measures would be implemented, such as:
- Installing spill containment systems and alarms.
- Training workers in proper handling and storage techniques.
- Providing PPE such as gloves, goggles, and flame-retardant clothing.
- Creating emergency response plans in case of spills or leaks.
Regular monitoring would ensure the controls are working, and documentation would provide a record of all the actions taken to address the identified risks.
Conclusion
Practical industrial safety risk assessments are a critical part of ensuring a safe and productive workplace. By identifying hazards, evaluating risks, and implementing control measures, businesses can reduce the likelihood of accidents, improve legal compliance, and enhance overall employee safety. This proactive approach not only protects employees but also fosters a culture of safety, efficiency, and continuous improvement.