Reciprocating Compressors: Operation and Maintenance
Reciprocating compressors are vital equipment in numerous industrial applications, used for compressing gases to achieve desired pressures. Their robust design and adaptability make them ideal for diverse sectors, including oil and gas, manufacturing, refrigeration, and chemical processing. This guide explores the operation, maintenance, and advancements in reciprocating compressors, offering insights into their principles, performance, and future trends.
Introduction to Reciprocating Compressors
A reciprocating compressor is a positive displacement machine that compresses gas by reducing its volume using a reciprocating piston within a cylinder. Its versatility and efficiency make it a preferred choice for applications requiring high pressures or small flow rates. Understanding the fundamentals of reciprocating compressors is essential for optimizing their performance and longevity.
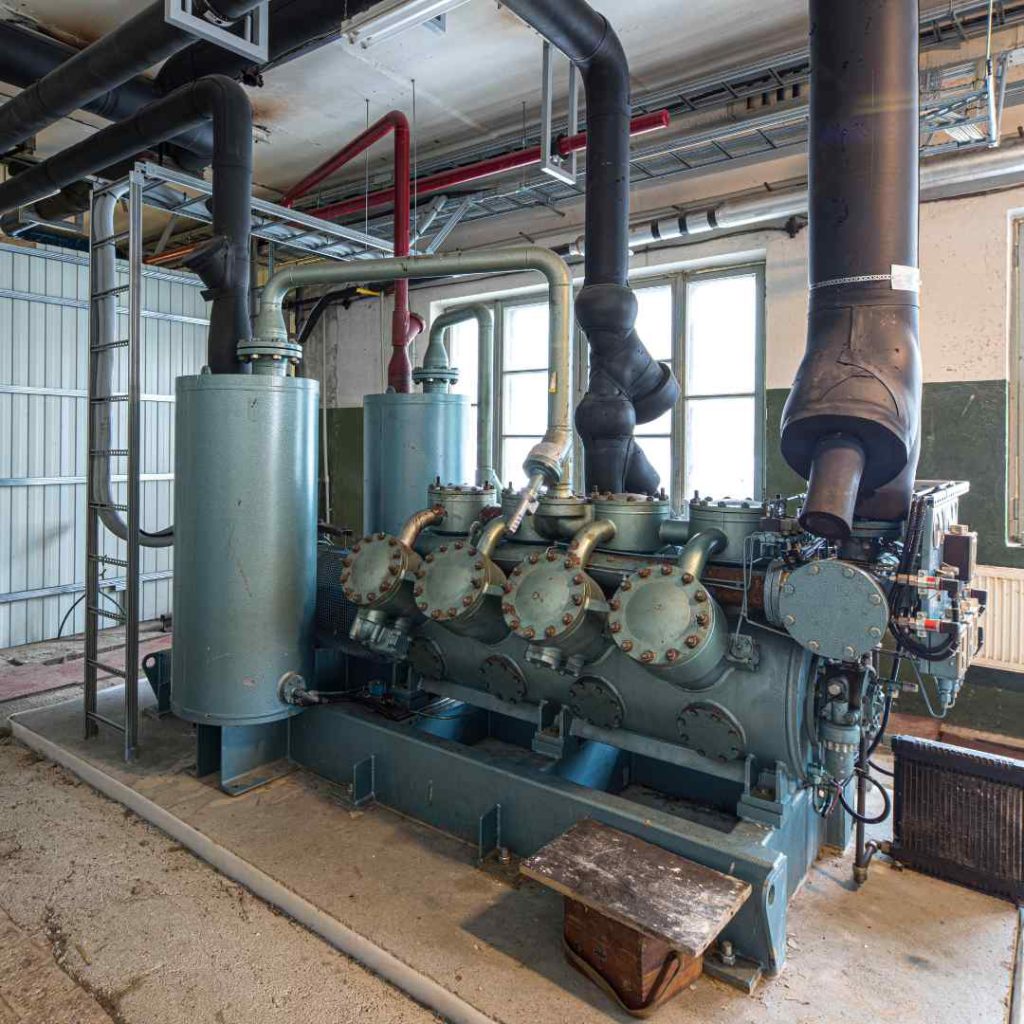
Basic Principles of Reciprocating Compressors
The basic working principle involves the piston moving back and forth within a cylinder to compress gas. During the suction stroke, the piston creates a vacuum, drawing gas into the cylinder. In the compression stroke, the piston reduces the gas volume, increasing its pressure before discharge. Key thermodynamic principles, such as Boyle’s Law and heat transfer, govern the compression process.
Reciprocating Compressor Types
Reciprocating compressors are categorized based on their design and application:
- Single-acting compressors: Compress gas on one side of the piston.
- Double-acting compressors: Compress gas on both sides of the piston, offering higher efficiency.
- Diaphragm compressors: Use a flexible diaphragm instead of a piston, ideal for handling corrosive or hazardous gases.
Compressor Components and Their Functions
Key components of reciprocating compressors include:
- Cylinder and piston: Perform the compression.
- Valves: Control the flow of gas into and out of the cylinder.
- Crankshaft and connecting rod: Convert rotational motion into reciprocating motion.
- Lubrication system: Reduces friction and wear between moving parts.
- Cooling system: Removes excess heat generated during compression.
Compressor Performance and Efficiency
The performance of reciprocating compressors is assessed based on parameters like volumetric efficiency, compression ratio, and power consumption. Volumetric efficiency is the ratio of the actual gas intake volume to the theoretical volume displaced by the piston. Factors such as valve design, leakage, and re-expansion of trapped gas affect this efficiency. The compression ratio, or the ratio of discharge pressure to suction pressure, directly influences the energy required for compression.
Improving efficiency involves minimizing pressure losses in valves and pipelines, using advanced materials to reduce wear and friction, and optimizing the design of pistons and cylinders. Modern advancements include variable-speed drives (VSDs) that adjust motor speed based on demand, reducing energy consumption during low-load operations. Additionally, multi-stage compression, where gas is compressed in stages with cooling between stages, enhances overall efficiency and reduces the work required for compression.
Lubrication and Cooling Systems
Lubrication and cooling systems are essential for maintaining the reliability and longevity of reciprocating compressors. Lubrication reduces friction between moving parts, such as pistons, connecting rods, and crankshafts, thereby minimizing wear. Compressors may use oil-lubricated or oil-free systems depending on the application. Oil-free systems are preferred in industries like food processing and pharmaceuticals where contamination must be avoided. The lubricant’s viscosity, thermal stability, and compatibility with the compressed gas are crucial for efficient operation.
Cooling systems manage the significant heat generated during compression. The two main types are water-cooled and air-cooled systems. In water-cooled systems, water absorbs the heat from compressor components, providing efficient cooling in high-capacity setups. Air-cooled systems use fins and fans to dissipate heat and are commonly used in smaller or portable compressors. Maintaining optimal operating temperatures prevents thermal expansion, overheating, and potential damage to components.
Compressor Operation and Control
Efficient operation of reciprocating compressors relies on robust control systems to manage pressure, flow rates, and operational stability. Control mechanisms include:
- Unloader valves: Reduce the load on the compressor during startup or when demand is low.
- Bypass valves: Redirect compressed gas to balance system pressure.
- Variable speed drives (VSDs): Adjust the motor speed to match demand, improving energy efficiency.
Automation technologies play a significant role in modern compressor control. Digital systems equipped with sensors monitor parameters like temperature, pressure, and vibration in real time. Automated shutdowns and alarms prevent potential failures and optimize performance. Effective control ensures stable operation, reduces energy consumption, and extends equipment lifespan.
Maintenance and Inspection Procedures
Regular maintenance and inspections are critical for ensuring the reliability and efficiency of reciprocating compressors. Maintenance tasks include:
- Leak detection: Identifying and fixing leaks in valves, gaskets, or seals.
- Valve inspection: Checking for wear, carbon deposits, and proper seating to maintain performance.
- Filter cleaning or replacement: Ensuring unimpeded gas flow and protecting internal components from debris.
Periodic inspections involve analyzing vibration, temperature, and pressure trends to detect early signs of issues. Scheduled downtime for preventive maintenance, such as lubrication system checks and cylinder bore inspections, helps avoid unexpected failures. Maintenance logs and records are vital for tracking performance and planning future interventions.
Troubleshooting and Repair
Troubleshooting focuses on diagnosing and addressing common problems in reciprocating compressors. Examples include:
- Valve failures: Resulting from wear, improper seating, or carbon deposits. Solutions include valve cleaning or replacement.
- Excessive vibration: Caused by misalignment, loose components, or unbalanced forces. Fixes involve realignment and dynamic balancing.
- Overheating: Often due to cooling system inefficiencies, excessive compression ratios, or lubrication failure. Ensuring proper cooling and lubrication addresses this issue.
Repair tasks range from replacing worn seals, pistons, and rods to complete overhauls involving reconditioning cylinders and crankshafts. Overhauls restore performance and extend compressor lifespan. Having spare parts readily available and adhering to repair guidelines are essential for minimizing downtime during repairs.
Future Trends and Developments
Advances in reciprocating compressors include improved materials, enhanced automation, and energy-efficient designs. Trends such as digital monitoring, predictive maintenance, and eco-friendly refrigerants are shaping the future of compressor technology. Innovations in compression techniques and system integration continue to expand their applications.
Case Studies and Practical Insights
Case studies highlight the successful application of reciprocating compressors in industries such as petrochemicals, power generation, and refrigeration. For example, the adoption of advanced control systems in natural gas compressors has reduced operational costs and enhanced reliability.