Root Cause Failure Analysis: Uncovering Systemic Issues in Industrial Operations
Root Cause Failure Analysis (RCFA) is a systematic approach to identifying and addressing the underlying causes of equipment, process, or system failures. Rather than focusing on surface-level symptoms, RCFA digs deeper to uncover the fundamental issues that lead to failures, ensuring they are resolved effectively and do not recur. This methodology is critical in industrial settings, where unplanned downtime and safety risks can have severe operational and financial consequences.
This article delves into the key aspects of RCFA, incorporating specific equipment analysis techniques, safety considerations, regulatory compliance, and methodologies for various industrial processes.
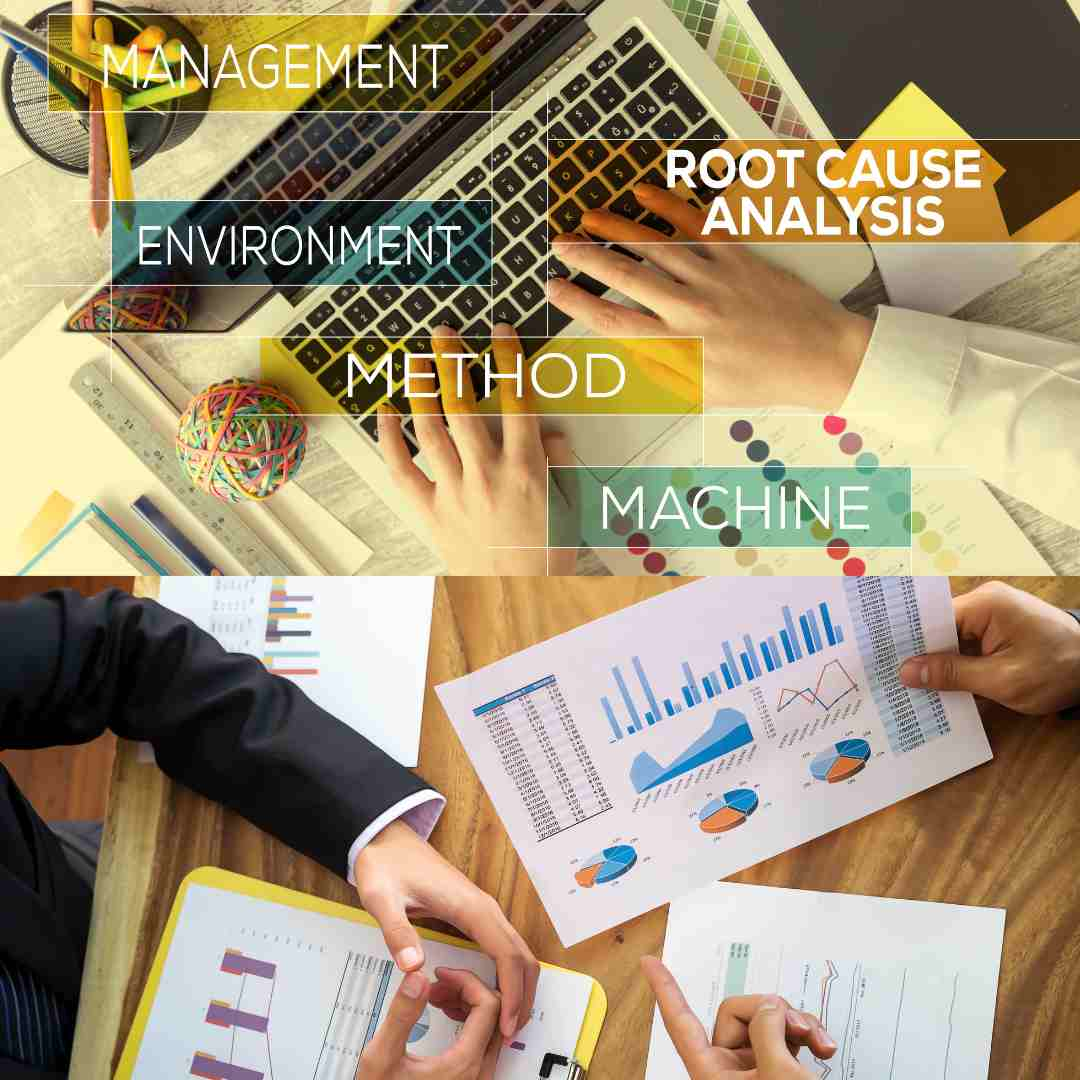
Table of Contents
ToggleGeneral Analysis Techniques
RCFA begins with defining the problem clearly, gathering data, and systematically analyzing it. The process involves several key steps:
- Failure Identification: Establish when, where, and how the failure occurred.
- Data Collection: Gather data from operational logs, maintenance records, and physical inspections of the failed equipment or system.
- Failure Mode Analysis: Use techniques like fault tree analysis (FTA), fishbone diagrams, or Pareto charts to identify potential failure modes.
- Cause-and-Effect Mapping: Link symptoms to their root causes by analyzing contributing factors, environmental conditions, and human interactions.
Use Case: In a manufacturing plant, conveyor belt failure may initially appear to result from wear and tear. However, detailed analysis might reveal misalignment issues caused by improper maintenance procedures.
Safety-Related Issues
Chapter 4 emphasizes the importance of addressing safety hazards during RCFA. Failures that lead to accidents, fires, or hazardous material releases demand immediate root cause identification to prevent recurrence. This process often includes:
- Evaluating human factors, such as operator errors or inadequate training.
- Analyzing safety-critical equipment, like emergency shutoffs or control systems.
- Reviewing compliance with workplace safety standards, such as OSHA or ISO 45001.
Example: A dust collector in a chemical plant fails, causing an explosion. RCFA may reveal that the root cause was insufficient airflow due to a clogged filter, exacerbated by deferred maintenance schedules and a lack of real-time monitoring.
Regulatory Compliance Issues
Failures in industrial systems often have regulatory implications. Chapter 5 explores how RCFA ensures compliance with environmental, safety, and quality standards. Key considerations include:
- Environmental Regulations: Identifying root causes of emissions or spills to prevent violations.
- Product Quality Standards: Analyzing failures in production systems to meet quality certifications like ISO 9001.
- Legal Implications: Addressing recurring failures to avoid litigation or penalties.
Use Case: A steam trap in a refinery malfunctions, causing excessive steam leaks. RCFA uncovers inadequate trap sizing during installation as the root cause, prompting a review of design standards to comply with energy efficiency regulations.
Process Performance Root Cause Failure Analysis Methodology
Chapter 6 outlines the step-by-step methodology for conducting RCFA in industrial processes:
- Define the Scope: Clearly identify the affected process or system.
- Develop a Hypothesis: Use historical data and expert input to form initial failure hypotheses.
- Conduct Investigations: Perform physical inspections, simulations, and tests to validate or rule out hypotheses.
- Implement Corrective Actions: Address root causes by modifying designs, procedures, or materials.
- Validate Results: Monitor the system post-implementation to ensure effectiveness.
Use Case: A gearbox reducer in a paper mill experiences frequent overheating. RCFA reveals that improper lubrication was used, leading to internal wear. The corrective action involves updating lubrication procedures and training maintenance personnel.
Equipment Design Evaluation and Failure Analysis Guide
A critical component of Root Cause Failure Analysis (RCFA) is evaluating the design, operation, and maintenance of equipment to pinpoint root causes of failures. Industrial machinery and equipment are often subjected to diverse operating conditions, making them prone to wear, misalignments, and environmental degradation. This guide provides a comprehensive overview of common issues and analysis techniques for different types of industrial equipment, emphasizing both design considerations and maintenance practices that can help prevent failures.
Fans, Blowers, and Fluidizers
Common Issues: Imbalanced blades, excessive vibration, bearing wear, and airflow disruptions.
Analysis Details: Failures in fans and blowers often result from misalignment, improper blade balancing, or contaminants in the airflow. RCFA for these systems involves using vibration analysis, thermography, and precision alignment tools to detect anomalies. Fluidizers, often used in material handling, may fail due to wear in nozzles or improper air pressure.
Example: A fluidizer in a cement plant shows uneven material flow, leading to production delays. RCFA uncovers blockages in nozzles due to inadequate filtration systems in compressed air lines.
Conveyors
Common Issues: Belt misalignment, motor overheating, overloading, and mechanical wear.
Analysis Details: Conveyors are prone to mechanical stress and misalignment. Failure analysis involves inspecting motor performance, load distribution, and alignment of pulleys and belts. Periodic load monitoring and predictive maintenance tools can help identify potential issues early.
Example: A packaging plant experiences frequent conveyor stoppages. RCFA determines that improper tensioning of the conveyor belt caused slippage, damaging motor components.
Mixers and Agitators
Common Issues: Impeller damage, shaft misalignment, and seal failure.
Analysis Details: Mixers and agitators are subject to high mechanical stresses and corrosive environments. RCFA for these systems includes shaft alignment checks, inspection of impeller integrity, and material compatibility analysis for seals. Improper operation or design can lead to uneven mixing and premature wear.
Example: In a pharmaceutical manufacturing process, a mixer fails due to impeller cracks. RCFA reveals that the impeller material was not compatible with the acidic solution being mixed.
Dust Collectors
Common Issues: Clogged filters, reduced airflow, and structural component failure.
Analysis Details: Dust collectors are critical for air quality management but are prone to filter clogs and wear in structural components. RCFA involves measuring pressure drops across filters, inspecting ductwork for blockages, and analyzing material buildup.
Example: A woodworking facility’s dust collector fails due to excessive heat in the system. RCFA identifies poor airflow caused by undersized ductwork and accumulation of sawdust in filters.
Process Rolls
Common Issues: Surface damage, misalignment, uneven pressure, and thermal fatigue.
Analysis Details: Process rolls are vital in industries like printing, textiles, and paper production. Common failure modes include uneven wear, thermal expansion, and surface cracks. Non-destructive testing methods like ultrasonic inspection or thermal imaging are often used to evaluate damage.
Example: In a paper mill, process rolls develop uneven surfaces, causing print quality defects. RCFA identifies excessive pressure and thermal cycling as the root cause, prompting a redesign of the roll material.
Gearboxes and Reducers
Common Issues: Overheating, excessive noise, oil leaks, and gear wear.
Analysis Details: Gearboxes and reducers often fail due to improper lubrication, misalignment, or contamination in the gear oil. Analyzing oil samples for wear particles and inspecting gear teeth for pitting or cracking are critical steps in RCFA.
Example: A gearbox in a mining conveyor overheats frequently. RCFA reveals contamination in the oil due to a damaged seal, leading to accelerated gear wear.
Steam Traps
Common Issues: Blockages, pressure imbalances, leaks, and premature wear.
Analysis Details: Steam traps, used in steam systems to remove condensate, are prone to malfunction due to debris buildup or incorrect sizing. RCFA involves ultrasonic testing, thermal imaging, and pressure monitoring to identify failure causes.
Example: In a refinery, steam trap failures lead to energy inefficiencies. RCFA reveals that oversized traps caused excessive cycling, leading to internal wear.
Inverters and Control Valves
Inverters: Failures in inverters often involve overheating, electrical component failure, or software glitches. RCFA focuses on power quality analysis, thermal testing, and firmware diagnostics.
Control Valves: Sticking or leaking control valves can disrupt processes. RCFA includes actuator calibration, flow testing, and material compatibility checks for valve components.
Example: A chemical plant faces process variability due to a sticking control valve. RCFA finds improper valve sizing and wear in the actuator mechanism.
Seals and Packing
Common Issues: Leakage, improper installation, and material degradation.
Analysis Details: Failures in seals and packing are often caused by incorrect material selection, environmental exposure, or high-pressure differentials. RCFA involves material compatibility testing, inspection of installation procedures, and pressure testing.
Example: A seal in a high-temperature pump fails prematurely. RCFA determines that the seal material was not rated for the operating temperature, leading to hardening and cracking.
Conclusion
Root Cause Failure Analysis is essential for maintaining the reliability, safety, and efficiency of industrial operations. By systematically identifying and addressing the fundamental causes of failures, businesses can reduce downtime, improve compliance, and enhance overall operational performance. Whether addressing safety-critical systems, regulatory concerns, or process inefficiencies, RCFA provides the tools to tackle challenges at their core, ensuring sustainable improvements in industrial systems.