Thermodynamics and Heat Powered Cycles
Thermodynamics is the study of energy, its transformations, and how it affects matter. This branch of physics plays a vital role in understanding the principles behind many mechanical systems and processes, particularly heat-powered cycles. These cycles are integral to machines like engines, refrigerators, and power plants. This article delves into the basic concepts of thermodynamics, the properties of thermodynamic substances, the laws governing energy transfer, and various heat-powered cycles that drive modern machinery and industry.
Table of Contents
ToggleBasic Concepts of Thermodynamics
At its core, thermodynamics involves the study of heat and work and their relationship to energy and matter. The central tenets of thermodynamics are energy conservation, energy degradation, and the transfer of energy through heat, work, and matter. Thermodynamic systems are categorized as either closed, open, or isolated, depending on whether or not they exchange matter or energy with their surroundings. The laws of thermodynamics provide the framework for understanding how energy flows within systems and governs processes like heat transfer and mechanical work.
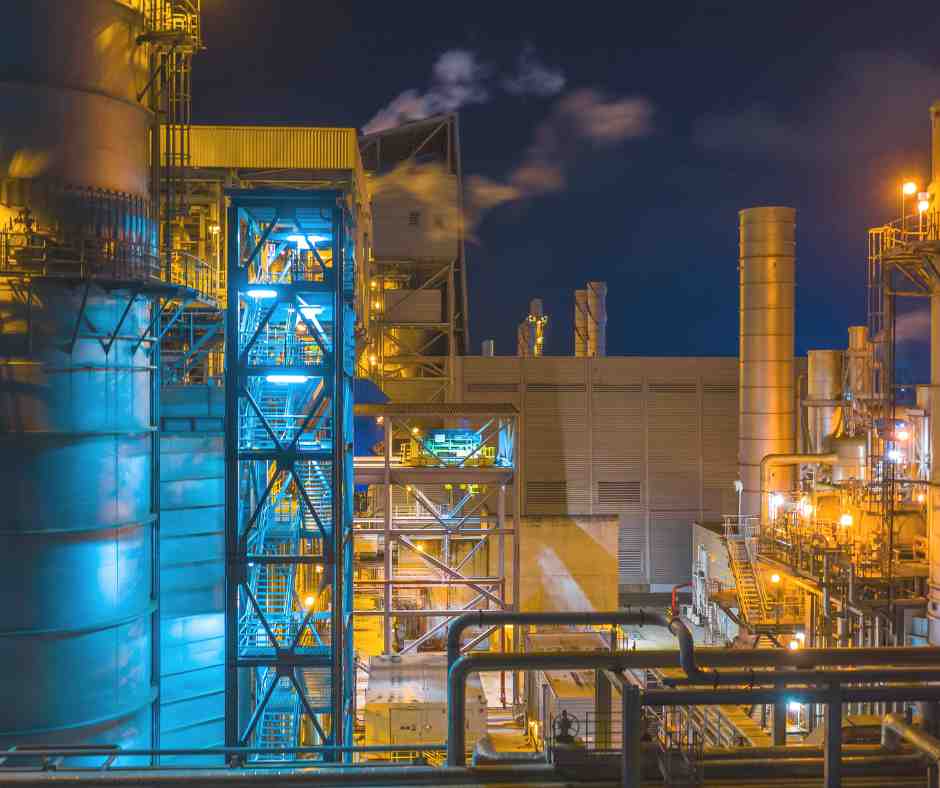
Properties of Thermodynamic Substances
Thermodynamic substances are materials whose properties can be quantified and used to analyze energy systems. These substances, which include gases, liquids, and solids, exhibit characteristics such as pressure, volume, temperature, and internal energy, which are key parameters in thermodynamic processes. By measuring these properties, engineers can model and design efficient systems for converting energy.
For example, water is a commonly used thermodynamic substance in power generation and refrigeration cycles, thanks to its high specific heat capacity and phase change properties (liquid to gas and vice versa). The properties of thermodynamic substances determine how efficiently heat and energy can be transferred or converted in a system.
First Law of Thermodynamics for Closed Systems
The First Law of Thermodynamics, also known as the Law of Energy Conservation, states that energy cannot be created or destroyed, only converted from one form to another. In a closed system (a system that does not exchange matter with its surroundings but can exchange energy), the change in the internal energy of the system is equal to the heat added to the system minus the work done by the system.
This law underpins much of the analysis of heat-powered cycles and energy efficiency.
First Law of Thermodynamics for Open Systems
For open systems, which can exchange both energy and matter with their surroundings, the First Law is modified to account for mass flow. In such systems, the change in internal energy is influenced by both the heat added to the system and the work done by the system, as well as the mass and energy entering or leaving the system.
This law is crucial for understanding the operation of engines, turbines, compressors, and other machinery where fluids (gases or liquids) are continuously entering and leaving the system.
Second Law of Thermodynamics
The Second Law of Thermodynamics addresses the direction of energy transfer and the efficiency of energy conversion. It states that the total entropy (a measure of disorder) of an isolated system always increases over time. In simple terms, energy spontaneously flows from regions of high concentration to low concentration, and some energy is always dissipated as heat, making the conversion of energy less than 100% efficient.
In practical terms, this law implies that no heat engine can be 100% efficient, as some energy will always be lost as waste heat. The Second Law sets the fundamental limits on the efficiency of thermodynamic systems, such as heat engines and refrigerators.
Entropy
Entropy is a key concept in thermodynamics, representing the degree of disorder or randomness in a system. The Second Law of Thermodynamics dictates that entropy in an isolated system tends to increase, which can be interpreted as the natural tendency of energy to disperse and become more chaotic. Entropy is often used to analyze and predict the efficiency of heat engines and other thermodynamic systems.
Exergy and Irreversibility
Exergy is a measure of the maximum useful work that can be extracted from a system as it comes to equilibrium with its surroundings. Unlike energy, which is conserved, exergy takes into account the quality or usefulness of energy. Irreversibility refers to the loss of exergy due to factors like friction, heat loss, and non-ideal processes.
Understanding exergy is crucial in improving system efficiency, as it helps to identify where energy losses are occurring and how to reduce them. Irreversibility limits the performance of thermodynamic cycles, and by minimizing it, engineers can design more efficient systems.
Vapor Cycles
Vapor cycles, such as the Rankine cycle, are used in steam power plants and refrigeration systems. In these cycles, a liquid (usually water) is heated to produce steam, which then expands and performs work by driving a turbine or piston. After performing work, the steam is cooled, condensed back into liquid form, and returned to the heat source to begin the cycle again.
The Rankine cycle is the most common vapor cycle used in power generation and is widely studied for its efficiency improvements and ability to generate large amounts of power.
Gas Closed System Cycles
In gas closed system cycles, gases are compressed, expanded, heated, and cooled in a closed loop. The most common example of a gas closed system cycle is the Brayton cycle, used in gas turbine engines. In the Brayton cycle, air is compressed, heated by combustion, expanded through a turbine to perform work, and then exhausted.
Gas closed system cycles are crucial in applications like jet propulsion, gas turbines, and power plants, where high efficiency and performance are essential. The efficiency of these cycles is influenced by factors like compression ratios, turbine inlet temperatures, and heat recovery methods.
Gas Open System Cycles
Gas open system cycles involve the continuous flow of gas into and out of the system, typically for heating, cooling, or power generation. These cycles are often used in open-cycle gas turbines, where air is drawn into the system, compressed, mixed with fuel, combusted, and then expanded through a turbine to produce work.
Open system cycles are typically less efficient than closed systems because they expel waste heat to the surroundings, but they are used in applications where continuous operation and quick startup are necessary.
Combined Cycle and Co-Generation
Combined cycle and co-generation systems are designed to improve efficiency by combining different thermodynamic cycles. A combined cycle typically involves a gas turbine system (like the Brayton cycle) followed by a steam turbine system (like the Rankine cycle). The waste heat from the gas turbine is used to produce steam, which drives the steam turbine, increasing the overall efficiency of the system.
Co-generation, or combined heat and power (CHP), refers to systems that produce both electricity and useful heat from a single energy source. These systems are widely used in industries to reduce fuel consumption, minimize waste, and improve energy efficiency.
Refrigeration and Heat Pump Cycles
Refrigeration and heat pump cycles work by transferring heat from one location to another. In refrigeration cycles, heat is extracted from a space or substance and expelled into the environment, lowering the temperature of the refrigerated space. Heat pumps, on the other hand, operate in reverse, absorbing heat from the outside and transferring it indoors to provide heating.
Both cycles rely on the same basic principles: the compression and expansion of a refrigerant, which undergoes phase changes to absorb and release heat. These cycles are used in air conditioning, refrigeration, and heating systems, with modern designs focusing on increasing efficiency and reducing environmental impact.
Finite-Time Thermodynamics
Finite-time thermodynamics is a subfield of thermodynamics that focuses on the performance of systems over a limited time frame. Unlike classical thermodynamics, which assumes that processes occur in infinite time (reaching equilibrium), finite-time thermodynamics considers real-world limitations such as heat transfer rates, friction, and time constraints. This approach is especially relevant for optimizing systems that require quick responses, such as engines and refrigeration units.
By analyzing and optimizing finite-time processes, engineers can design systems that achieve the best possible performance within the given time limitations, improving both efficiency and functionality.
Conclusion
Thermodynamics and heat-powered cycles are foundational to many mechanical and energy systems, from power generation and refrigeration to engines and manufacturing processes. Understanding the basic principles of thermodynamics, such as the laws governing energy, entropy, exergy, and various heat cycles, is crucial for designing efficient and reliable systems. Advances in thermodynamics, including the study of finite-time processes and combined cycles, continue to drive improvements in energy efficiency, environmental sustainability, and cost-effectiveness across industries. By applying these principles effectively, engineers and scientists can optimize performance and push the boundaries of what is possible in energy systems.