Some welding processes resemble both soldering and brazing and molten metal is applied to produce a joint between the two pieces. However, in welding, the added metal is, more often than not, of similar composition to the metals being joined, and the joined pieces are melted locally so differences between the weld metal and the pieces being joined are structural rather than compositional.
Welding calls for rather different techniques to those employed in brazing and soldering. The speed of working is particularly important if complete melting of the metal near the joint is to be avoided. Some welding processes rely on pressure to affect the joining of the two halves and in such cases, no metal is added to form a joint, the weld metal being provided by the two parts being joined. Thus we have both fusion and pressure-welding processes, as indicated in the picture.
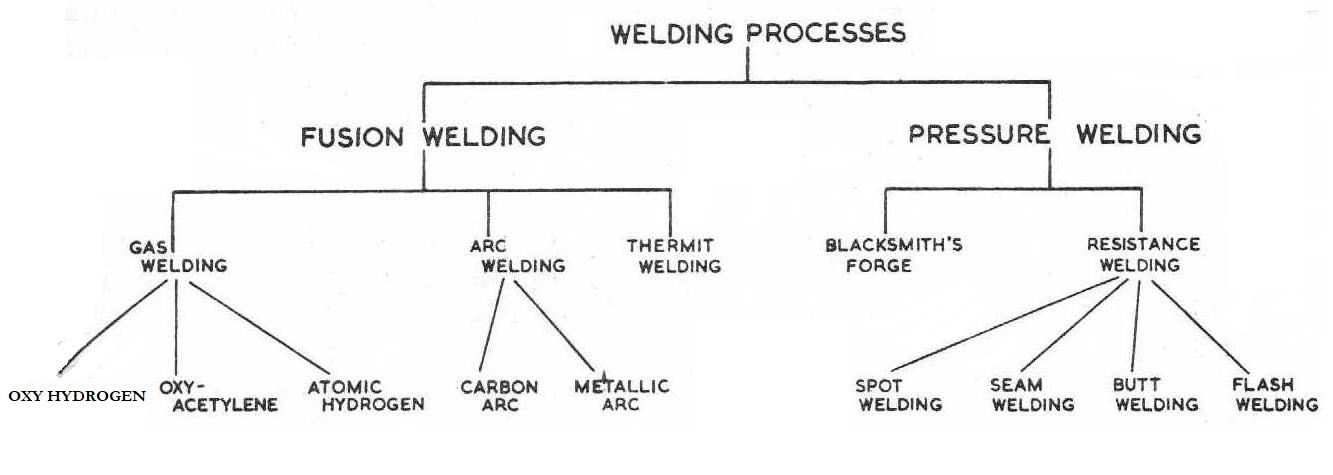
- Fusion Welding Processes
In all fusion welding, high temperatures are employed in or to melt the parts quickly. In this way damage to the unmelted metal near the weld is minimized since the time at high tempera is reduced. Also, heat must be supplied fast because the pieces being joined will conduct heat away from the weld area at a quite high rate.
Fusion welding can be classified according to the source of heat. The most common sources are gas flame and electric arc, chemical reactions, laser beams, and electron beams are also used in special applications.
Gas flames usually use acetylene and oxygen, since both gases are readily available and very high temperatures are easily attained Hydrogen and oxygen can be used to get even higher temperatures by the atomic hydrogen welding torch, which uses an electric arc to supplement the heat of combustion.
Electric arcs can be struck between two non-consumed elects a non-consumed electrode and the work, or between a consumed electrode and the work. The third is, perhaps, the most common; the electrode is continually melted to supply the weld metal needed to fill the weld. When non-consumable electrodes are used (carbon and tungsten are common), a separate filler rod is melted in the arc to fill the weld.
In all welding, the molten metal is shielded by non-reactive gas to prevent oxidation. In gas flame welding the combustion products form this shield, but in electric arc methods, it must h provided either by a continuous supply of gas (such as argon or helium) from a cylinder or by including a combustible material in the flux.
Flux is used in most welding processes to slag off oxides and impurities in the molten metal as well as to burn and provide an unreactive gas shield around the molten metal. While flux is usually supplied to the joint by coating it on filter rods, it is sometimes applied as a loose powder that is piled on the area being welded. Read the welding processes handbook.
- Pressure Welding Processes
In pressure welding, no extra metal is added to the joint. These processes can be divided into two classes according to whether r not the joint is ever molten.
The blacksmith’s forge is the most common example of pressure welding without melting. The pieces to be joined are heated above their recrystallization temperature and forced together by hammering. At the joint, any oxide on the surface gets broken up, and direct metal-to-metal contact is established. A metallic bond is formed wherever there is direct contact, and the metal recrystallizes across the joint forming a continuous crystal structure. A more modern version of this is ultrasonic welding, where the two surfaces to be joined are rubbed together by high-frequency sound waves. This rubbing breaks up the oxide film and friction supplies the heat. Fine wires are welded to microscopic electronic circuits in his way.
Other common pressure welding processes depend on electric current to heat the weld area until it is soft or even molten. The parts to be joined are then pushed together and the hot met cooled. All such methods rely on the electrical resistance of the weld area (caused by oxide on the surfaces and the irregularity of the surfaces) to localize the heating. Such processes include spot welding, seam welding, and butt welding.
A welder may boast that his weld is stronger than the parent metal. He backs up this statement by the fact that welds seldom fail before metal near a weld. Read more Welding Secrets.