Introduction
The design of rotating electrical machines is fundamental to the fields of power generation, industrial automation, and electric transportation. These machines, including motors and generators, convert electrical energy to mechanical energy and vice versa. Their design involves careful consideration of electromagnetic, thermal, and mechanical aspects to ensure efficiency, durability, and performance. With advances in materials, computer-aided design, and simulation tools, modern machine design focuses on compact, energy-efficient, and high-performance solutions. Applications span across electric vehicles, renewable energy systems, and industrial machinery, making expertise in rotating machine design vital for modern electrical and mechanical engineers.
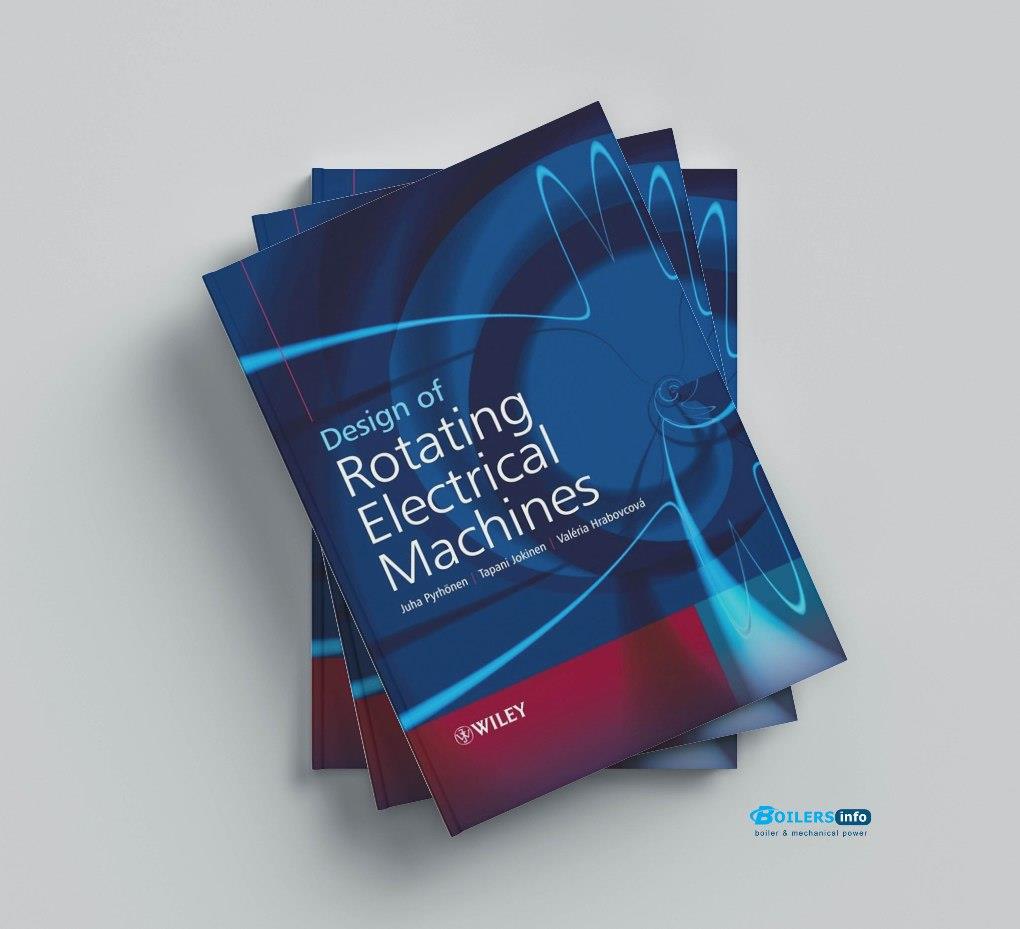
What Are Rotating Electrical Machines?
Rotating electrical machines are electromechanical devices that rely on electromagnetic principles to convert energy. They are broadly classified into:
- Electric Motors: Convert electrical energy into mechanical energy.
- Electric Generators: Convert mechanical energy into electrical energy.
These machines are used in applications ranging from household appliances and industrial drives to power plants and electric vehicles.
Key Components of Rotating Electrical Machines
Understanding the key parts is essential before diving into the design process:
- Stator: The stationary part that houses windings and produces a magnetic field.
- Rotor: The rotating part that responds to the magnetic field.
- Shaft: Transmits mechanical energy.
- Bearings: Support the shaft and ensure smooth rotation.
- Cooling System: Regulates temperature during operation.
- Frame and Housing: Provide mechanical support and protection.
Design Objectives for Electrical Machines
As an electrical design engineer, your primary goals include:
- High efficiency
- Thermal stability
- Mechanical strength
- Cost-effectiveness
- Compliance with IEC/IEEE standards
- Ease of manufacturing and maintenance
Step-by-Step Design Process of Rotating Electrical Machines
1. Define Machine Specifications
Start with application-specific requirements:
- Power rating (kW/HP)
- Speed (RPM)
- Voltage & current
- Duty cycle
- Environmental conditions (temperature, humidity, etc.)
2. Select Machine Type
- DC machines for variable speed and torque control
- Induction motors for rugged, maintenance-free operation
- Synchronous machines for high-precision and power factor correction
3. Magnetic Design
- Use electromagnetic simulations (e.g., FEM tools like ANSYS Maxwell) to design the magnetic circuit.
- Optimize flux paths and core geometries.
- Choose high-permeability core materials to reduce iron losses.
4. Electrical Design
- Select appropriate winding configurations (lap, wave, distributed, or concentrated).
- Decide the number of poles and slots.
- Calculate winding resistance, leakage reactance, and insulation class.
5. Thermal Design
- Estimate power losses: copper loss, core loss, stray loss.
- Ensure proper heat dissipation using air, water, or oil cooling.
- Use thermal analysis software to verify that the temperature rise stays within limits.
6. Mechanical Design
- Determine shaft size, bearing type, and rotor dynamics.
- Analyze vibrations and critical speed.
- Use CAD tools for 3D modeling of frame, housing, and rotor-stator assembly.
7. Material Selection
- Core: CRGO steel or amorphous metal
- Winding: Copper (preferred) or aluminum
- Insulation: Class F/H depending on ambient temperature
- Bearings: Ball or roller depending on load type
8. Prototyping and Testing
- Build a prototype to validate design.
- Perform type tests (no-load, locked rotor, temperature rise, vibration, noise).
- Iterate based on test results.
Modern Tools for Electrical Machine Design
- Finite Element Analysis (FEA): For magnetic and thermal simulations
- MATLAB/Simulink: For dynamic and control modeling
- CAD Software: For mechanical layout
- Digital Twin Technology: For predictive maintenance and real-time performance monitoring
Common Design Challenges and Solutions
Challenge | Solution |
---|---|
Overheating | Improve cooling systems, use better insulation |
Low Efficiency | Optimize the magnetic circuit, reduce losses |
Vibration/Noise | Rotor balancing, precision machining |
High Manufacturing Cost | Use modular design, simplify assembly |
Applications of Rotating Electrical Machines
- Industrial drives
- HVAC systems
- Wind and hydro turbines
- Electric vehicles
- Aerospace and robotics
Conclusion and 📚⬇️
Designing rotating electrical machines is a multi-disciplinary task requiring knowledge of electromagnetics, thermodynamics, mechanics, and control systems. As an electrical design engineer, leveraging simulation tools, following international standards, and staying updated with modern manufacturing technologies will empower you to deliver reliable and high-performance machines for diverse industries.