In the water tube boiler the upper drum (Boiler steam drum) provides for separation of steam from water. It also provides liquid holdup capacity (typically 10 to 60 seconds) to allow for a dynamic response to load changes without losing liquid in the downcomer and riser tubes. The size of the steam drum is determined by the volume required for a clean separation between steam and water to produce a dry saturated steam, it also provides an adequate amount of steam storage. The steam drum is also called the upper drum.
Steam drum internals for typical type of boiler are shown. The internals include separation devices to assist in separating small droplets of boiler water from the steam. Boiler water in the steam will cause scaling of the superheater and steam turbines. Baffles, chevron types separators and demister pads are used to minimize boiler water carryover. The demisters coalesce the smaller drops into larger drops so that they will settle back into the water phase. An alternate separation uses a cyclone separators as the first separating device followed by demister pads. Saturated steam from the steam drum contain no more than 0.5% moisture and 0.5 ppm solids.
Other steam drum internals include feedwater piping, blowdown piping, and chemical injection piping. The feedwater inlet must be baffled so that changes in BFW Boiler Feed Water rate do not set up waves that affect level measurement.
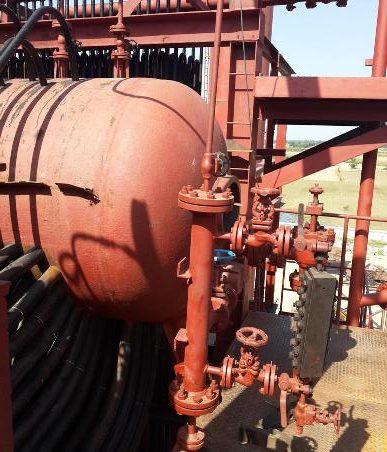
Note that the steam drum plate into which the downcomer and riser tubes are connected is thicker than the rest of the drum. The tubes are rolled into this plate like the tubes in an exchanger are rolled into the tube sheet. Expanded tube connections are generally suitable for pressures up to 1200 psia. A typical drum plate was almost 3.5” thick for a design pressure at 800 psig. Sometimes the tubes are also back welded, especially in high pressure boilers. Tubes may be back welded to repair leaks.