What is Deaeration?
The process through which the dissolved corrosive gases are removed from the Boiler Feed water is called deaeration. The equipment, which is used in this method, is called Deaerator. Today we will discuss Boiler Deaerator Working Principle.
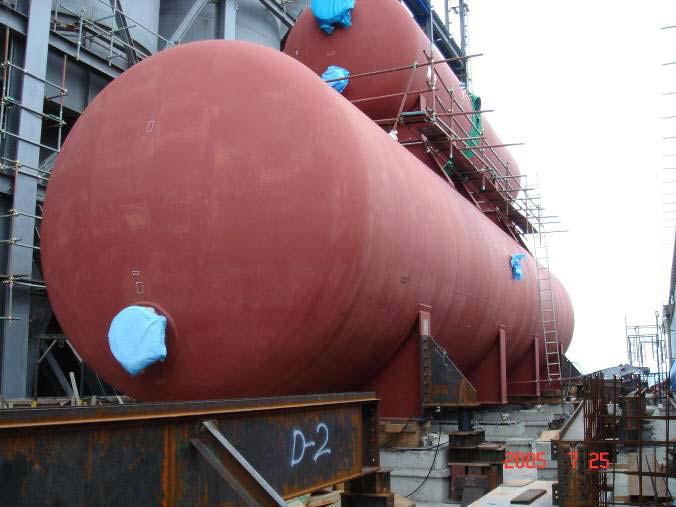
The necessity of deaeration:
Deaeration is needed to control the corrosion processes in the downstream system. In water, the presence of dissolved gases, particularly oxygen and carbon dioxide, causes accelerated corrosion. Oxygen is the most violent. The elimination of oxygen cannot be ignored. Even little concentrations of oxygen gas cause serious corrosion and pitting problems. The primary function of the deaeration and deaerator is to prevent this corrosion by removing the dissolved gases from all sources of water entering the downstream system such as lines, piping, especially boilers, condensate lines, etc.
Types of Deaerator:
Deaerator equipment is designed to reduce dissolved corrosive gases in the boiler feed water. This is done at times by heating the water to the temperature closed to the saturated temperature at the pressure within the deaerating equipment. A deaerator, generally, reduces the oxygen level to 7ppb. There are basically two types of deaerators in common use:
Deaerator Working Principle :
In the Boiler deaerator Working Principle Water is heated close to saturation temperature with a minimum pressure drop and minimum vent. This ensures the best thermal operating efficiency. Deaeration is done by spraying the boiler feed water over multiple layers of trays designed to provide large contact area of the liquid surface to Pegging steam. This scrubbing steam is fed from the bottom of the deaerator when it contacts with BFW, it heated up to saturation temperature dissolved corrosive Gases released from feed water with some vapors from the vent valve. Then treated water falls to the storage tank below the deaerator.
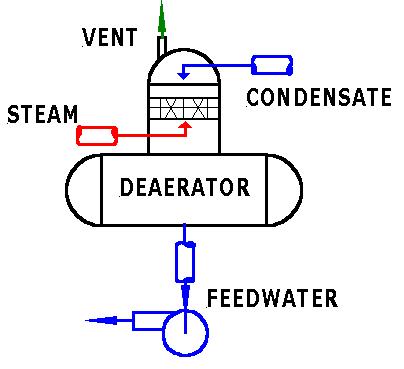
Location: Boiler feed water pump takes suction from DA Storage tank. some of the saturated water can be flash into steam due to suction pressure, which may cause cavitation Problem in BFW Pump. To prevent this deaerator should be placed at sufficient height So it provides NPSHA to pump. Another advantage of this location is that “ According to Hennery law the solubility of non-condensable gases decreases at low pressure.” So the gases can be removed more efficiently at height.
Deaerator put into operation:
Confirm that all the instrument of the system has been put into operation and operates normally according to your plant procedure. Confirm that all the equipment has been energized and Confirm the level of the deaerator water tank is normal, The state of valves is normal. Confirm that the auxiliary steam pressure is normal. Gradually open deaerator pressure control valve and maintain the deaerator temperature 110 °C. After the startup/shutdown feed water pump startup, regulate the inlet valve to keep the deaerator water tank level through the condensate system. (If the condensate quality is not qualified, the feed water may be supplied directly from the soft water (water treatment system).
Safety Precautions
After deaerator has been installed and overhauled, the actuation test of safe valve should be carried out in the local for avoiding being stuck.
When the turbine operates at any condition, two deaerator water tanks should be operated in parallel. And its steam pressure, water level, and temperature should be kept as same as possible and could not be operated individually.
Before supplying water and steam to the deaerator, the deaerator vent valve should be opened first.
One set of the pressure regulating device and the water level regulator is used in common for two deaerator.
Before the vacuum has not been established in the condenser, avoid the steam and water of deaerator drain to the condenser.
After the turbine shuts down and the main feed water pump is stopped, the plant start-up and shutdown feed-water pump should keep operation for some time to cool the main coolant system, at this time, the deaerator should be operated continuously until the plant start-up and shutdown feed water pump stops.
To prevent exceeding the design pressure the deaerator has been equipped with two safety valves and to prevent the vacuum the deaerator should be equipped with vacuum breakers.