Introduction to Internal Combustion Engines
Internal combustion engines (ICEs) are the backbone of modern transportation, power generation, and industrial applications. These engines generate power by burning fuel within a confined space, converting chemical energy into mechanical energy. Understanding their design, operation, and optimization involves exploring various scientific and engineering principles. This article delves into the grouped topics surrounding ICEs, combining related themes into a cohesive discussion.
Fundamentals: Thermodynamics, Combustion, and Fuels
The operation of an internal combustion engine is deeply rooted in thermodynamic principles. The engine’s working cycle—whether Otto, Diesel, or a variant—relies on the laws of thermodynamics to define the conversion of heat into work. The efficiency and power output of the engine depend significantly on the processes of compression, expansion, heat addition, and heat rejection.
Combustion, the chemical reaction between fuel and oxygen, is at the core of power generation in ICEs. The choice of fuel—gasoline, diesel, natural gas, or biofuels—directly affects engine performance, efficiency, and emissions. The combustion process must be carefully managed to optimize energy release while minimizing harmful byproducts such as carbon dioxide (CO2), nitrogen oxides (NOx), and particulate matter. Advances in fuel formulation and alternative energy sources continue to enhance the sustainability and efficiency of internal combustion engines.
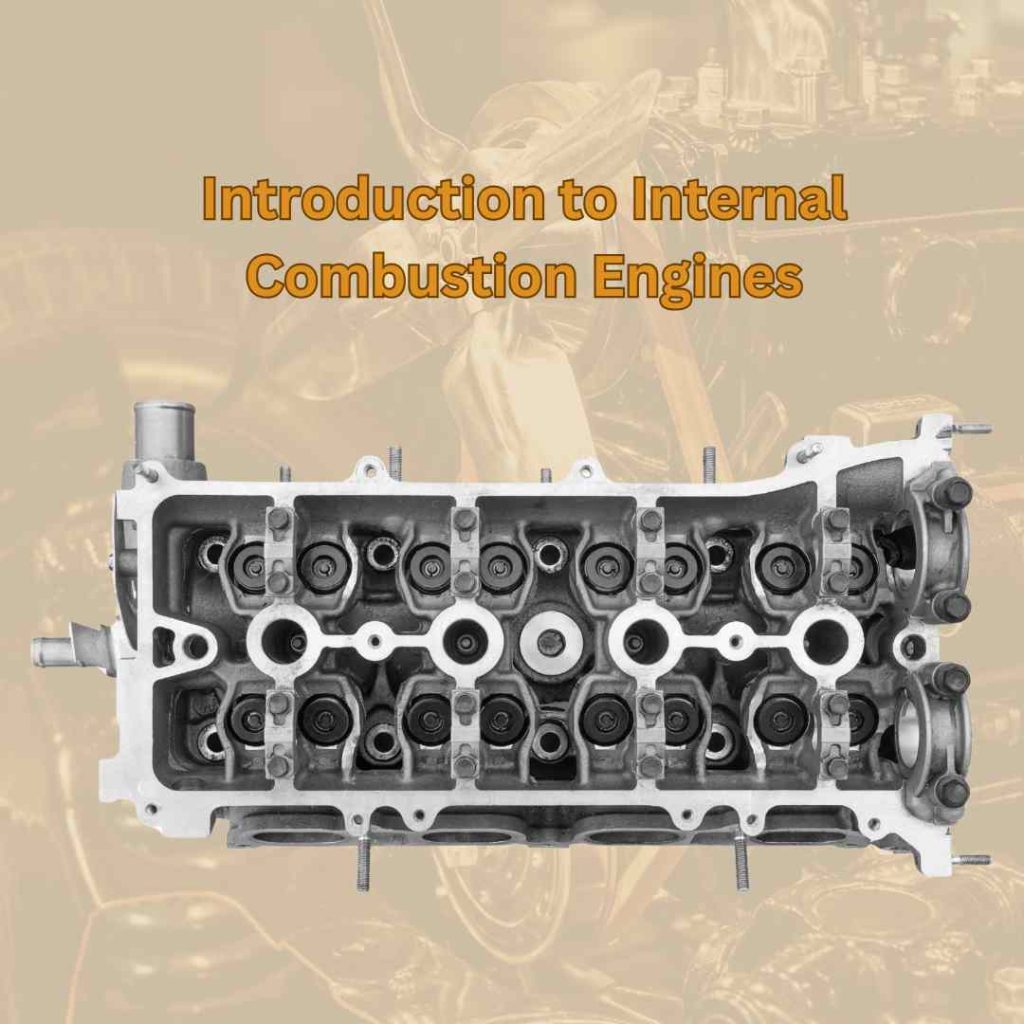
Engine Types and Cycles: Spark Ignition, Compression Ignition, and Two-Stroke Engines
Internal combustion engines are broadly categorized into spark-ignition (SI) and compression-ignition (CI) types. Spark-ignition engines use an electric spark to ignite a fuel-air mixture, typically gasoline, and are commonly used in passenger vehicles. Compression-ignition engines, or diesel engines, ignite fuel through the heat of compressed air, offering superior efficiency and durability, making them ideal for heavy-duty applications.
Two-stroke engines, though less common than four-stroke engines, are widely used in small-scale applications such as motorcycles and chainsaws due to their simplicity and high power-to-weight ratio. However, they face challenges in emissions and efficiency, driving research into cleaner and more efficient two-stroke technologies.
Flow Dynamics: Induction, Exhaust, and In-Cylinder Motion
Efficient air-fuel mixture preparation and evacuation of exhaust gases are crucial for optimal engine performance. The induction process governs the entry of air or an air-fuel mixture into the cylinder, while the exhaust process ensures the removal of combustion byproducts.
In-cylinder motion, including swirl, tumble, and squish, plays a vital role in mixing the fuel-air charge and facilitating complete combustion. Advanced computational tools and experimental techniques are employed to study and optimize these flow patterns, enhancing engine performance and reducing emissions. Turbocharging further improves airflow by compressing the intake air, increasing engine power and efficiency without increasing engine displacement.
Thermal and Mechanical Considerations: Heat Transfer, Temperature, and Pressure
Temperature and pressure dynamics are integral to engine design and operation. High temperatures and pressures during combustion impose significant stresses on engine components. Effective heat transfer management is critical to prevent thermal damage, ensure consistent operation, and maintain efficiency.
Heat dissipation occurs through various pathways, including conduction, convection, and radiation. Modern engines employ advanced cooling systems, thermal coatings, and heat-resistant materials to manage thermal loads. Pressure dynamics, on the other hand, influence the force exerted on the piston and dictate the mechanical design of the engine.
Advanced Topics: Engine Modeling, Turbocharging, and Experimental Facilities
Engine modeling has revolutionized the design and analysis of internal combustion engines. Computational models simulate engine performance under various operating conditions, reducing the need for costly prototypes and enabling rapid iteration. These models integrate fluid dynamics, thermodynamics, and combustion chemistry to predict engine behavior accurately.
Turbocharging is another transformative technology, improving engine efficiency and power output by utilizing exhaust gases to drive a turbine that compresses intake air. This process boosts engine performance without increasing fuel consumption, making it a key technology in modern ICE development.
Experimental facilities, such as engine test benches and flow visualization labs, play a critical role in validating theoretical models and optimizing engine design. These facilities enable researchers to study engine behavior under controlled conditions, paving the way for innovations in fuel efficiency, emissions reduction, and overall engine performance.
Mechanical Design: Durability and Innovation
Mechanical design considerations are paramount in ensuring the durability and reliability of internal combustion engines. Components such as the crankshaft, connecting rods, pistons, and valves must withstand high stresses and temperatures while operating efficiently. Modern materials, including lightweight alloys and composites, are increasingly used to reduce engine weight and improve performance.
Innovations in design, such as variable valve timing (VVT) and advanced fuel injection systems, further enhance engine efficiency and adaptability. These technologies allow engines to operate optimally across a range of speeds and loads, reducing fuel consumption and emissions.
Conclusion
Internal combustion engines are a marvel of engineering, combining principles of thermodynamics, fluid dynamics, material science, and mechanical design to power the modern world. While challenges such as emissions and sustainability persist, ongoing advancements in fuel technologies, turbocharging, engine modeling, and experimental research continue to push the boundaries of ICE performance. As the global energy landscape evolves, the integration of cleaner fuels and hybrid technologies ensures that internal combustion engines remain a vital part of the energy mix for years to come.