π Pipe Welding Procedures: A Complete Guide
Pipe welding is a crucial skill in industries such as oil & gas, power generation, chemical plants, and water infrastructure. The integrity and durability of pipe welds directly impact system safety and performance. This guide presents an in-depth overview of essential pipe welding procedures, standards, techniques, and best practices.
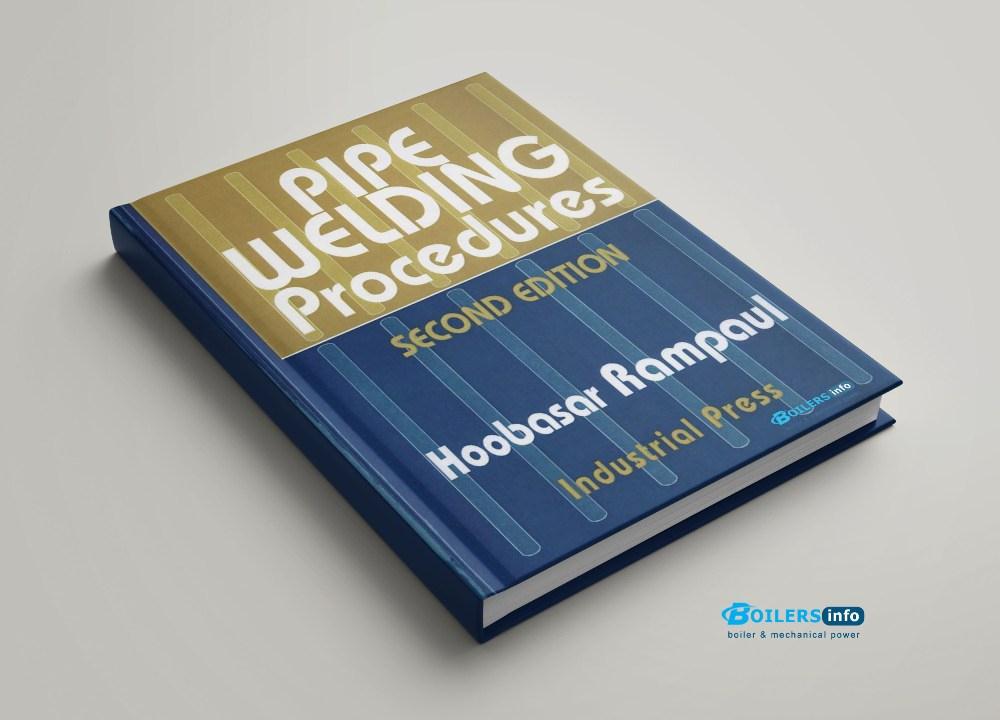
π§ Basic Pipe Welding Procedures
Pipe welding involves joining cylindrical metal sections using various welding processes. The choice of procedure depends on the pipe material, thickness, position, and application. Key steps include:
- Joint preparation
- Root pass welding
- Fill passes
- Cap or cover pass
π Pipe Welding Standards and Codes
Welders must adhere to industry codes such as:
- ASME Section IX
- API 1104
- ISO 9606
- AWS D10.12
These codes define qualification requirements, inspection criteria, and acceptable defect levels.
β‘ Essentials of Shielded Metal Arc Welding (SMAW) Technology
SMAW, or stick welding, is widely used in pipe welding for its versatility. Key elements include:
- Selection of correct electrodes (E6010, E7018)
- Control of arc length and travel speed
- Managing heat input to prevent defects
π‘ Heat Input and Distribution
Proper heat input is essential for weld quality:
- Heat Input: Excessive heat can cause warping or burn-through.
- Heat Distribution: Uneven heating leads to residual stresses.
Controlling amperage, voltage, and travel speed ensures stable heat distribution.
π§© Preparation of the Pipe Joint
Joint preparation is vital for penetration and weld soundness:
- The Keyhole: The small opening created during welding that allows full penetration.
- Whipping Technique: A method to control puddle and arc length.
- Stopping the Weld: Proper techniques avoid crater cracks.
β° Uphill Welding the Root Bead on Heavy-Wall Pipe (5G & 6G)
For heavy-wall pipe, uphill welding provides superior penetration and strength:
- Begin with a uniform keyhole.
- Maintain a steady rod angle.
- Inspect visually for defects and uniformity.
π₯ Welding the Root Bead by GTAW Process (TIG Welding)
Gas Tungsten Arc Welding (GTAW) offers precision:
- Requires clean joints, quality filler rods, and argon shielding gas.
- Pulse current enhances control.
- Caution: Avoid overheating and contamination.
- An Introduction to Practical Welding
β The Intermediate and Cover Passes
- Use correct electrodes for intermediate (fill) and cover passes.
- Maintain interpass temperature.
- Clean slag thoroughly between passes.
π§ͺ Welding Thin-Wall Pipe
- Uphill Welding: Preferred for smaller diameters.
- Downhill Welding: Faster, but requires skill to avoid burn-through.
- Tack Welds: Essential to prevent distortion during welding.
β Horizontal Pipe Welding (2G Position)
2G welding involves horizontal welding with the pipe axis vertical:
- Alloy steels and cryogenic materials require preheat and post-weld heat treatment.
- Control heat input to minimize stress.
π Welding Complicated Pipe Joints
Complex joints include:
- T-Joints
- Y-Joints
- Angular (6G) positions
Each requires tailored techniques and sometimes special jigs or fixtures.
π Introduction to Welding Metallurgy
Understanding metallurgy is crucial:
- Grain structure affects strength and ductility.
- Iron-carbon diagrams explain phase transformations.
- Residual stresses influence cracking and distortion.
π Distortion in Pipe Welding
Distortion is caused by uneven heating and cooling:
- Use balanced welding sequences.
- Apply restraints where necessary.
- Example cases show distortion patterns and correction methods.
β Pipe Welding Defects
Common defects:
- Arc strike cracking
- Under-bead cracking
- Porosity
- Remedies include proper preheat, filler selection, and stress relief.
- Welding Secrets
π Fitting-Up Pipe
Successful welding starts with correct fit-up:
- Tools: Clamps, wedges, gauges.
- Precise alignment reduces stress and improves weld quality.
π Qualification of Welding Procedure & Welder
- Procedure Qualification Records (PQR) ensure the process is sound.
- Welders undergo qualification tests (e.g., bend tests) to certify their skills.
π¦Ί General Welding Safety
Key safety principles include:
- Protective gear: helmets, gloves, jackets.
- Safe gas cylinder handling.
- Ventilation to control fumes.
Welding Procedures Book
β This comprehensive handbook covers the essentials from joint preparation to metallurgical considerations, ensuring welders are well-prepared to produce high-quality, defect-free pipe welds. If youβd like to explore this topic in more depth, you can download the complete PDF guide πΒ for easy reading and future reference.