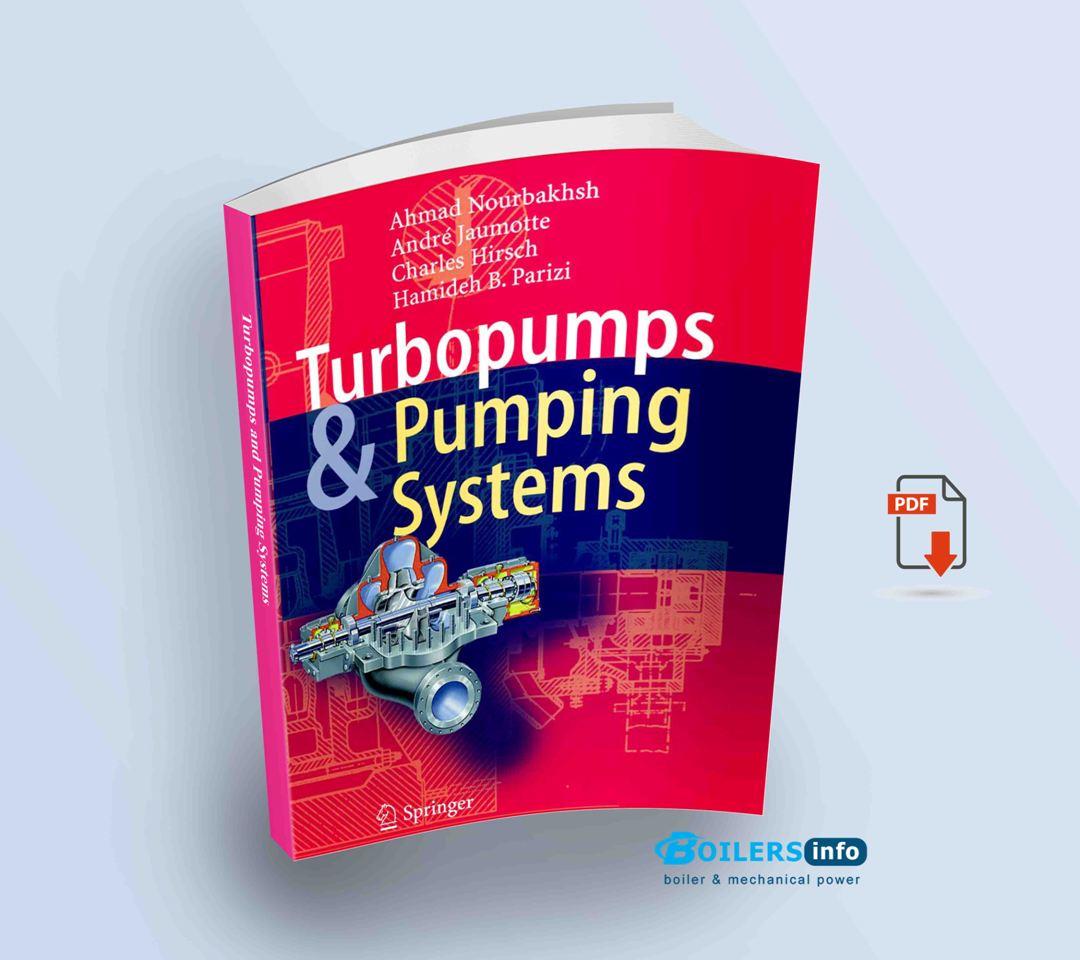
Turbopumps and Pumping Systems: An Overview
Pumping systems are integral components in various industries, from energy and chemicals to water treatment and aerospace. Turbopumps, in particular, are specialized pumps used in high-demand environments such as rocket propulsion systems and industrial processes. This article explores the fundamentals, design principles, operational characteristics, and best practices associated with turbopumps and centrifugal pumping systems.
Introduction to Turbopumps
Turbopumps are a category of pumps designed to transfer liquids, typically at high flow rates and pressures, using a turbine to impart kinetic energy to the fluid. They are used in critical systems where reliable and high-performance fluid transfer is required, including rocket propulsion, chemical processing, and industrial applications. Turbopumps are a combination of turbines and pumps that are often used to transfer fuels and coolants.
Fundamental Concepts
The working principle of a turbopump is based on the conversion of mechanical energy into fluid kinetic energy. The pump component of the turbopump is typically a centrifugal pump, which utilizes the high rotational speed of an impeller to accelerate and pressurize the fluid. The turbine component drives the impeller, and the design aims to maximize energy transfer efficiency while minimizing mechanical losses.
Key components include:
- Impeller: Transfers energy to the fluid.
- Turbine: Drives the impeller, powered by a high-pressure gas or fluid.
- Bearings and seals: Support the rotating components and ensure a tight seal to prevent leakage.
Similarity Laws
Similarity laws are fundamental in scaling pump designs and ensuring performance consistency. These laws relate geometric, kinematic, and dynamic similarities between models and full-scale pumps. The three main similarity criteria include:
- Geometric similarity: All dimensions are scaled in proportion.
- Kinematic similarity: Flow patterns and velocities are consistent between models.
- Dynamic similarity: Forces acting on the system (e.g., pressure, velocity) are similarly distributed.
The Affinity Laws are derived from these similarity principles and govern the relationships between pump parameters such as flow rate, head, and power with changes in speed and size.
Centrifugal Pump Design and Application
Centrifugal pumps, the most common type used in turbopump systems, operate by converting kinetic energy into pressure. The design elements of a centrifugal pump include:
- Impeller Design: Impeller blades are key to energy transfer, with design variations including radial, mixed-flow, and axial types, depending on the application.
- Pump Casing: Directs fluid flow efficiently into and out of the pump, often designed to reduce turbulence.
- Suction and Discharge Volutes: Enclose the impeller and help guide the fluid into and out of the pump.
These pumps are ideal for applications requiring high flow rates and moderate pressures, like in irrigation, water supply, and industrial fluid handling.
Cavitation Process in Impeller Pumps
Cavitation occurs when the local pressure in a pump falls below the vapor pressure of the liquid, leading to the formation of vapor bubbles. These bubbles collapse when they reach regions of higher pressure, creating shock waves that can damage the pump’s components.
Preventing cavitation is critical to maintaining pump efficiency and longevity. Measures to avoid cavitation include:
- Maintaining sufficient inlet pressure
- Controlling pump speed and operating conditions
- Selecting materials that resist cavitation erosion
Axial and Radial Flow Pumps
Axial flow pumps move fluid along the axis of the pump, similar to how a propeller moves water. These pumps are used in applications requiring high flow rates and low to moderate pressure, such as flood control and wastewater treatment.
Radial flow pumps, on the other hand, direct fluid radially outward from the impeller. They are more efficient in generating higher pressures and are commonly used in industrial processes, including turbopumps in rocket engines.
Operational Properties of Characteristic Curves
Each pump, whether centrifugal or turbopump, has a characteristic curve that represents its performance. The curve plots the relationship between:
- Flow rate (Q) and Head (H)
- Efficiency (η) and Power consumption
The characteristic curve helps in understanding the pump’s behavior under various operational conditions, and it is essential for:
- Selecting the right pump for an application
- Optimizing system performance
- Preventing undesirable operating conditions (e.g., cavitation or overloading)
Pipeline Calculations
Proper pipeline design is crucial in ensuring that fluid is transported efficiently from the pump to its destination. Pipeline calculations consider factors like:
- Frictional losses due to pipe material, diameter, and length
- Pressure drop over the length of the pipeline
- Flow rate requirements and the resulting energy demands
These calculations are essential for sizing the pump, selecting the correct pipe material, and ensuring the overall system is balanced and efficient.
Pump Performance in a Piping System
When a pump is integrated into a piping system, it must overcome the resistance presented by the system. The pump’s ability to meet the required flow rate and pressure depends on:
- System curve: Describes the relationship between the flow rate and the pressure drop across the system.
- Pump curve: Describes how the pump performs at different flow rates.
By analyzing the interaction between the system curve and the pump curve, operators can determine the optimal operating point, maximizing efficiency and minimizing energy consumption.
Water Hammer
Water hammer refers to the pressure surge or shock wave that occurs when the flow of water in a pipeline is suddenly stopped or changed. This phenomenon can damage pumps, valves, and pipes.
Preventing water hammer involves:
- Using slow-closing valves
- Installing air chambers or surge tanks
- Maintaining proper pressure control within the system
Pump Stations
A pump station is a facility designed to house one or more pumps to move water, chemicals, or other fluids within a system. Key elements of a pump station include:
- Pumps (either centrifugal or positive displacement)
- Motors or turbines that drive the pumps
- Control systems to monitor and regulate performance
- Pressure vessels for flow regulation
Pump stations are vital for large-scale water distribution, wastewater management, and irrigation.
Turbopump’s Elements
Turbopumps in high-pressure and high-flow applications, such as in aerospace and rocket propulsion, include the following elements:
- Turbine: Typically a radial-flow turbine that drives the impeller.
- Pump Impeller: Accelerates the fluid to high velocities.
- Bearing System: Ensures smooth rotation at high speeds.
- Seals: Prevent fluid leakage and maintain pressure.
- Nozzles and Diffusers: Control the flow of the pumped fluid.
These elements must be designed for high efficiency, reliability, and resistance to extreme conditions such as high temperatures, vibration, and pressure fluctuations.
Centrifugal Pump Operation
Centrifugal pumps operate by using the rotational energy of the impeller to accelerate the fluid and convert the energy into pressure. Key operational considerations include:
- Flow rate: The volume of fluid the pump can move.
- Head: The energy imparted to the fluid, typically measured in meters.
- Efficiency: A measure of how well the pump converts input energy into useful work.
Proper operation requires attention to system conditions, maintenance, and proper selection of pump size and type.
Open and Closed Impellers
- Open Impellers: Have no shroud around the blades, which allows for easy handling of solid-laden fluids but can suffer from cavitation.
- Closed Impellers: Have a shroud surrounding the blades, which provides better suction and higher efficiency, but they are more complex and may not handle solids as well as open impellers.
The choice between open and closed impellers depends on the application and the nature of the fluid being pumped.