Job Hazard Analysis: A Guide for Voluntary Compliance and Beyond
Introduction
In any workplace, safety is paramount. Employers, employees, and stakeholders all have a vested interest in minimizing risks and ensuring that work environments are as hazard-free as possible. Job Hazard Analysis (JHA), also referred to as Job Safety Analysis (JSA), is a systematic approach to identifying, assessing, and controlling workplace hazards. This comprehensive tool not only addresses potential risks but also fosters a proactive culture of safety and operational efficiency. While many organizations adopt JHA to meet regulatory compliance requirements, its benefits extend far beyond legal obligations, offering a pathway to continuous improvement and enhanced workplace morale. This article serves as a detailed guide to understanding JHA, implementing it effectively, and leveraging its potential to transform workplace safety.
Understanding Job Hazard Analysis
Job Hazard Analysis is a structured process that evaluates tasks within a job to identify hazards and implement appropriate controls. It involves a detailed breakdown of each job into individual steps, with a thorough assessment of associated risks. This process focuses on:
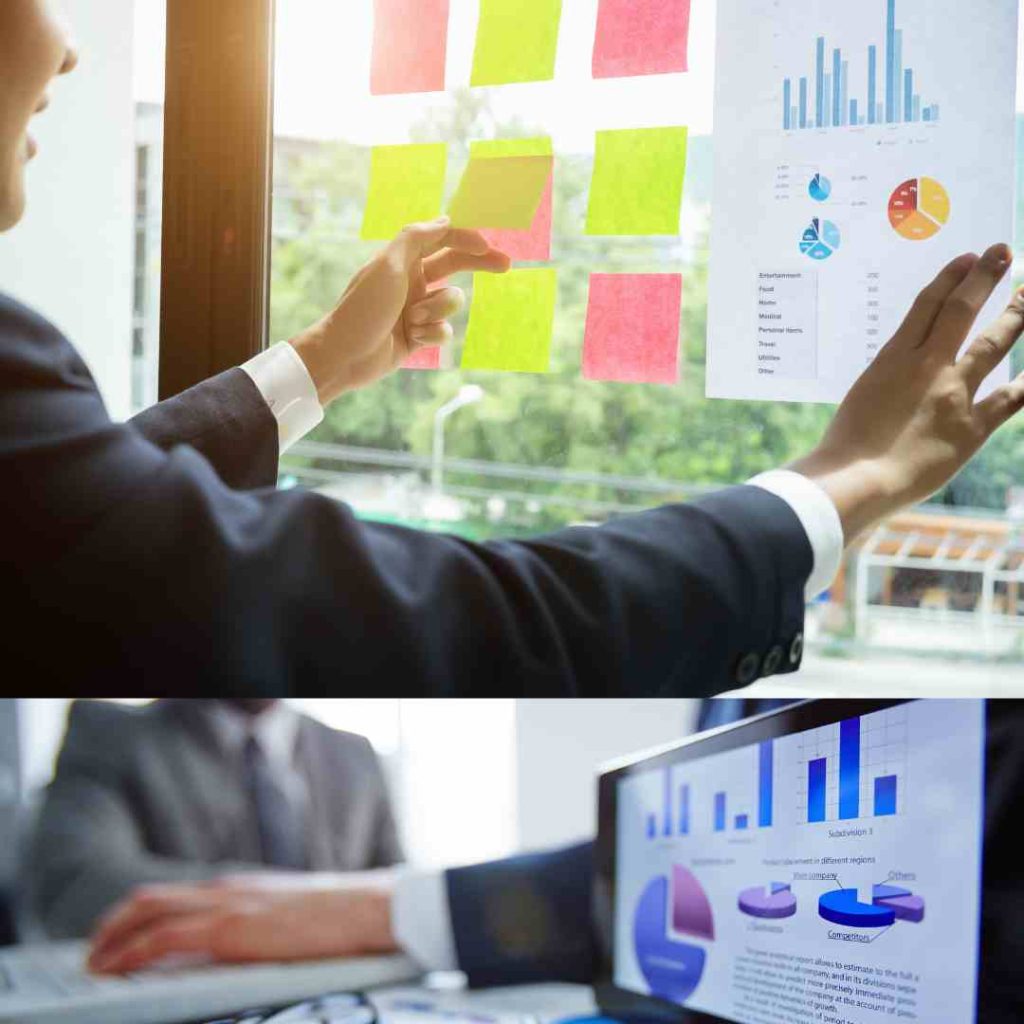
- Task Identification: Breaking down a job into its constituent tasks, ensuring every step is analyzed.
- Hazard Identification: Pinpointing risks associated with each task, considering potential causes and effects.
- Risk Assessment: Evaluating the likelihood and severity of these risks to prioritize mitigation measures.
- Control Measures: Implementing strategies to eliminate or minimize the identified risks, such as using protective equipment or redesigning processes.
By addressing hazards proactively, JHA serves as a foundation for building safer work environments. It also integrates seamlessly with broader occupational health and safety (OHS) programs, enabling organizations to achieve compliance while fostering innovation in safety practices.
The Importance of Voluntary Compliance
Voluntary compliance with JHA principles goes beyond fulfilling minimum legal requirements. It reflects an organization’s commitment to employee welfare and operational excellence. The key advantages of embracing JHA voluntarily include:
Enhanced Workplace Safety: Proactively identifying and addressing hazards reduces the likelihood of accidents and injuries, creating a safer work environment for everyone.
Improved Operational Efficiency: A safer workplace minimizes disruptions caused by incidents, leading to smoother operations and improved productivity.
Boosted Employee Morale: Demonstrating a commitment to safety fosters trust among employees, making them feel valued and supported.
Preparedness for Regulatory Inspections: Organizations that adopt JHA voluntarily are better equipped to meet and exceed regulatory requirements, reducing the risk of penalties or compliance issues.
Voluntary compliance is not just a strategy for legal adherence but also a core component of organizational resilience and sustainability.
Key Steps in Conducting a Job Hazard Analysis
Step 1: Select the Jobs to Analyze
The first step in JHA is identifying which jobs to analyze. This involves prioritizing tasks with the highest potential risks or those that have led to incidents in the past. Key considerations include:
High-Risk Tasks: Jobs with a history of frequent or severe injuries should be analyzed first.
Complex Procedures: Tasks involving intricate procedures or multiple steps often harbor hidden risks.
New Equipment or Materials: Jobs that incorporate unfamiliar tools or substances may introduce new hazards.
Unusual Working Conditions: Tasks performed under extreme weather conditions or during emergencies require special attention.
By focusing on these areas, organizations can allocate resources effectively and address the most critical risks.
Step 2: Break the Job into Steps
Once the job is selected, it should be broken down into manageable steps. Each step should represent a specific action or sequence, such as:
- Starting machinery.
- Moving materials from one location to another.
- Operating control panels or monitoring systems.
Clarity is crucial during this phase. Avoid overly detailed or overly vague descriptions, as these can hinder the identification of hazards. The goal is to ensure that every critical action is accounted for while keeping the process manageable.
Step 3: Identify Hazards
Hazard identification is the heart of JHA. For each task step, the team should consider potential hazards by asking the following questions:
- What could go wrong during this step?
- What are the consequences of an error or failure?
- Are there environmental, mechanical, or human factors contributing to these risks?
- Are existing controls effective, or are additional measures needed?
Common hazards include:
Physical Hazards: Slips, trips, falls, or contact with moving machinery.
Chemical Hazards: Exposure to harmful substances such as solvents, acids, or fumes.
Ergonomic Hazards: Repetitive motions, awkward postures, or excessive force.
Environmental Hazards: Noise, extreme temperatures, or inadequate lighting.
A thorough hazard identification process ensures that no risk is overlooked, laying the groundwork for effective mitigation.
Step 4: Develop Control Measures
Once hazards are identified, control measures must be developed to address them. These measures should follow the hierarchy of hazard control:
- Elimination: Remove the hazard entirely, such as discontinuing a risky procedure.
- Substitution: Replace hazardous materials or processes with safer alternatives.
- Engineering Controls: Isolate workers from the hazard through design solutions, such as machine guards or ventilation systems.
- Administrative Controls: Implement policies, training, or scheduling changes to reduce risk exposure.
- Personal Protective Equipment (PPE): Provide equipment such as gloves, helmets, or respirators to shield workers from residual hazards.
Employing multiple controls often delivers the most robust protection, ensuring that risks are mitigated comprehensively.
Step 5: Implement and Review
Implementation involves putting the identified controls into practice and ensuring that all affected workers are trained to use them correctly. Regular reviews and updates are essential to maintaining the effectiveness of the JHA. Changes in job tasks, equipment, or conditions may introduce new hazards, requiring adjustments to the analysis and control measures.
Beyond Compliance: The Broader Benefits of JHA
While regulatory compliance is a critical motivator, JHA offers broader benefits that enhance organizational performance and culture. These include:
Fostering a Safety Culture: JHA encourages employees to take an active role in identifying and mitigating risks, creating a collective sense of responsibility for safety.
Enhancing Communication: The collaborative nature of JHA promotes open dialogue between management and workers, strengthening trust and understanding.
Driving Continuous Improvement: By regularly revisiting and updating JHAs, organizations can identify opportunities to refine processes and adopt best practices.
Reducing Costs: Preventing accidents not only protects workers but also reduces costs associated with insurance claims, legal fees, and lost productivity.
JHA serves as a cornerstone for building safer, more efficient, and more resilient workplaces.
Challenges in Implementing JHA
Despite its advantages, implementing JHA can present challenges. These include:
Limited Resources: Small organizations may struggle with time or expertise to conduct thorough analyses.
Resistance to Change: Employees or managers may be reluctant to adopt new procedures, viewing them as burdensome or unnecessary.
Overwhelming Data: Excessive detail in analyses can lead to information fatigue, making it difficult to prioritize actions.
Overcoming these challenges requires strong leadership, effective training, and a focus on practicality. Involving employees and aligning JHA efforts with broader organizational goals can also help address resistance and resource constraints.
Practical Tips for Effective JHA
- Involve Frontline Workers: Employees who perform the tasks daily are invaluable sources of insight into potential hazards.
- Maintain Comprehensive Documentation: Detailed records of JHAs and their updates ensure consistency and accountability.
- Provide Regular Training: Continuous education ensures that all employees understand their roles in maintaining a safe workplace.
- Integrate JHA with Other Programs: Align JHA efforts with existing safety, quality, and operational initiatives to maximize impact.
- Leverage Technology: Digital tools can streamline data collection, analysis, and reporting, making JHA more efficient and accessible.
Case Studies: Success Stories
Organizations that have successfully implemented JHA often see significant improvements in safety and productivity. Examples include:
Manufacturing Industry: A plant reduced machinery-related injuries by 40% by incorporating JHA into its equipment maintenance procedures.
Construction Sector: A firm achieved zero incidents over two years by conducting regular JHA workshops and engaging employees in hazard identification.
Healthcare Sector: A hospital minimized ergonomic injuries among staff by redesigning lifting tasks based on JHA findings.
These case studies demonstrate the transformative potential of JHA across various industries.
Conclusion
Job Hazard Analysis is a versatile tool that goes beyond regulatory compliance to enhance workplace safety, operational efficiency, and employee well-being. By systematically identifying and mitigating risks, organizations can create environments where workers feel secure and valued. Whether starting from scratch or refining existing processes, embracing JHA offers a pathway to sustainable safety excellence and continuous improvement. It is not merely a procedural requirement but a strategic asset for any organization committed to long-term success.