Essential Practices for Process Safety Culture
Process safety culture is a critical component in the successful and safe operation of industries dealing with hazardous materials and complex systems. It encompasses the shared values, attitudes, and behaviors of employees and management toward identifying, managing, and mitigating process safety risks. A robust process safety culture helps organizations prevent accidents, protect employees and the community, and ensure compliance with regulatory standards. This article delves into the essential practices for developing and sustaining a strong process safety culture, emphasizing practical steps, leadership involvement, and continuous improvement.
Introduction to Process Safety Culture
Process safety focuses on preventing catastrophic accidents related to the release of hazardous substances. Unlike occupational safety, which emphasizes personal safety issues like slips and falls, process safety involves systemic risks such as explosions, toxic releases, and structural failures. Process safety culture integrates these considerations into the organizational ethos, ensuring that safety is a priority at every level.
A strong process safety culture requires:
- Leadership commitment to safety values.
- Employee engagement in safety practices.
- Transparent communication of risks and incidents.
- Continuous learning and improvement in safety processes.
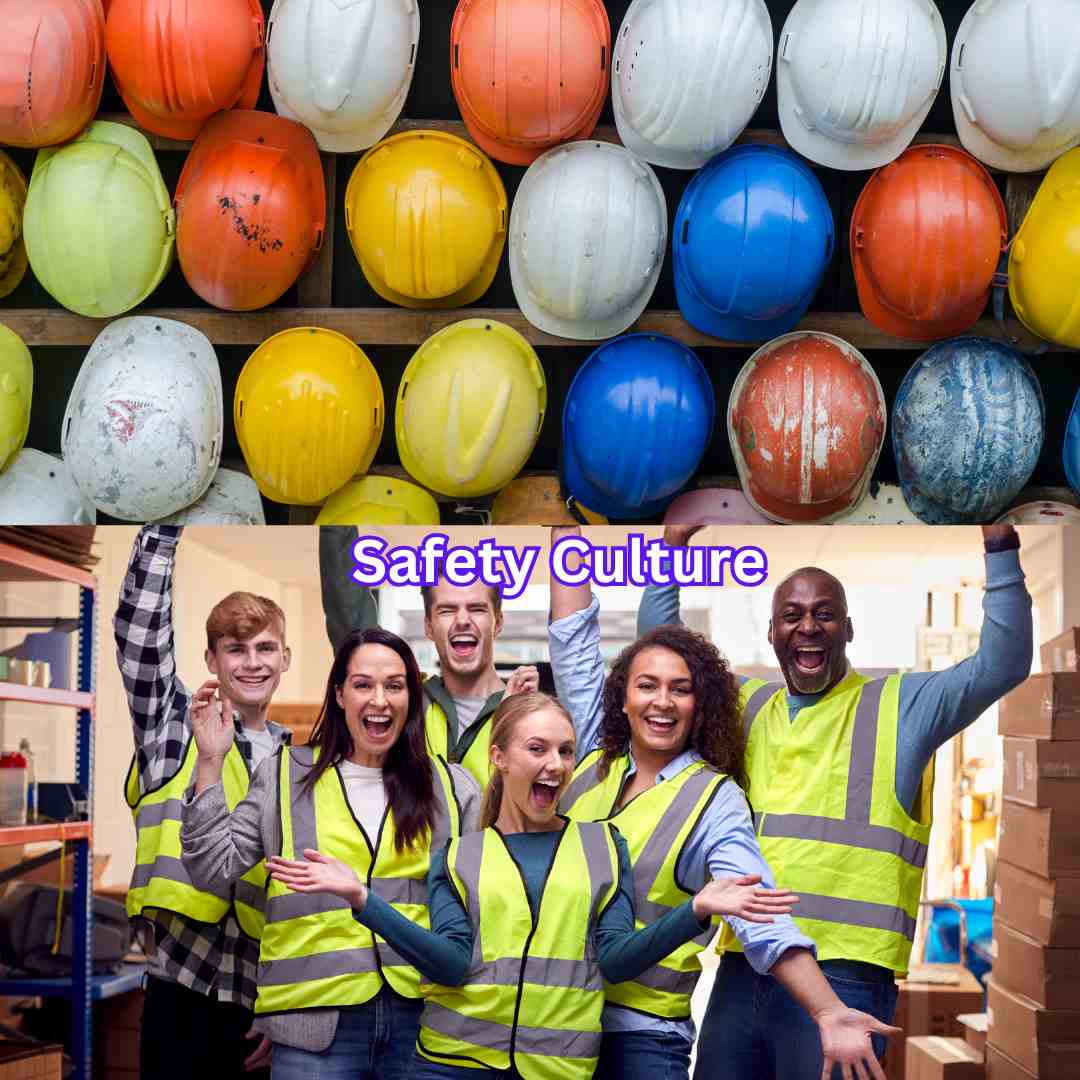
Key Elements of Process Safety Culture
- Leadership and Commitment
- Leadership sets the tone for process safety culture. Managers and executives must actively demonstrate their commitment to safety through policies, actions, and resource allocation.
- Visible leadership involvement, such as participating in safety meetings and incident investigations, reinforces the importance of process safety.
- Employee Involvement
- A strong safety culture relies on employee participation in identifying risks, reporting hazards, and contributing to safety solutions.
- Encouraging open communication and eliminating fear of reprisal for reporting concerns fosters trust and engagement.
- Risk Awareness and Understanding
- Employees and management must have a clear understanding of the hazards associated with their processes and the potential consequences of failures.
- Regular training and education ensure that all personnel are equipped with the knowledge to manage risks effectively.
- Learning from Incidents
- An organization’s ability to learn from near misses, incidents, and external events is essential for improving process safety.
- Establishing a robust incident investigation process helps identify root causes and implement preventive measures.
- Accountability
- Accountability at all levels ensures that safety responsibilities are clearly defined and upheld.
- Regular audits and performance reviews help reinforce accountability and drive improvements.
Essential Practices for Developing Process Safety Culture
1. Leadership Engagement
Leadership engagement is the cornerstone of any successful safety culture. Executives and managers must prioritize safety by:
- Allocating sufficient resources for safety initiatives.
- Setting clear safety goals and objectives.
- Leading by example and adhering to safety protocols.
- Recognizing and rewarding safety achievements.
2. Training and Competence Development
Ensuring that employees are knowledgeable and competent in process safety practices is vital. Training programs should include:
- Hazard identification and risk assessment techniques.
- Emergency response and incident management.
- Process-specific safety standards and procedures.
- Regular refresher courses to maintain competence.
3. Open Communication and Reporting
An effective safety culture encourages open communication about safety concerns, near misses, and incidents. Organizations can achieve this by:
- Implementing anonymous reporting systems.
- Regularly sharing safety performance data and lessons learned.
- Conducting open forums and discussions on safety issues.
4. Risk Assessment and Management
Robust risk assessment and management practices are essential for identifying and mitigating hazards. Key steps include:
- Conducting comprehensive hazard identification studies such as HAZOP (Hazard and Operability Study).
- Prioritizing risks based on severity and likelihood.
- Implementing engineering and administrative controls to reduce risks.
5. Continuous Improvement
Continuous improvement is central to sustaining a strong safety culture. This involves:
- Regularly reviewing and updating safety policies and procedures.
- Monitoring safety performance indicators.
- Benchmarking against industry best practices.
6. Empowering Employees
Employees should feel empowered to act on safety concerns and take ownership of their role in maintaining process safety. Strategies include:
- Providing tools and resources for risk mitigation.
- Encouraging employees to stop work if they observe unsafe conditions.
- Including employees in decision-making processes related to safety.
7. Learning from External Events
Studying incidents and best practices from other organizations provides valuable insights. This can be achieved by:
- Reviewing industry reports and case studies.
- Participating in industry safety forums and conferences.
- Adopting proven safety technologies and methods.
Challenges in Building a Process Safety Culture
Developing and sustaining a strong safety culture is not without challenges. Common obstacles include:
- Resistance to Change
- Employees and management may resist changes to established processes and practices.
- Overcoming this requires clear communication of the benefits and involving stakeholders in the change process.
- Balancing Productivity and Safety
- Pressure to meet production targets can sometimes overshadow safety priorities.
- Establishing safety as a non-negotiable value ensures it is not compromised for productivity.
- Lack of Resources
- Limited budgets and personnel can hinder the implementation of safety initiatives.
- Organizations must prioritize safety investments to achieve long-term benefits.
- Inconsistent Practices
- Inconsistent application of safety practices across teams or sites undermines safety culture.
- Standardizing safety procedures and conducting regular audits help address this issue.
Case Studies: Lessons from Process Safety Culture
Case Study 1: The Oil Refinery Incident
An oil refinery experienced a catastrophic explosion due to a failure to identify and mitigate corrosion in critical equipment. Key lessons included:
- The importance of thorough risk assessments and inspections.
- The need for a robust incident investigation process to prevent recurrence.
- Enhancing employee training on recognizing signs of equipment degradation.
Case Study 2: Chemical Plant Success Story
A chemical plant implemented a process safety management system that led to significant improvements in safety performance. Key practices included:
- Establishing a safety leadership team to oversee initiatives.
- Regularly engaging employees through safety workshops and training.
- Leveraging data analytics to predict and prevent incidents.
Measuring and Monitoring Safety Culture
To ensure continuous improvement, organizations must measure and monitor their process safety culture. Tools and methods include:
- Surveys and Questionnaires: Gather employee feedback on safety attitudes and practices.
- Safety Audits: Assess compliance with safety standards and identify gaps.
- Incident Metrics: Track leading and lagging indicators such as near misses, unsafe conditions, and incidents.
- Employee Participation Rates: Monitor involvement in safety meetings, training, and initiatives.
Conclusion
Developing and sustaining a strong process safety culture is essential for minimizing risks, protecting lives, and ensuring operational efficiency. By prioritizing leadership engagement, fostering open communication, empowering employees, and committing to continuous improvement, organizations can create a culture that values safety as a core principle. Overcoming challenges and learning from past incidents further strengthens the foundation for a resilient safety culture. A proactive and inclusive approach to process safety not only prevents accidents but also enhances organizational performance and reputation.