Essentials of Health and Safety at Work (HSE)
Health and Safety at Work (HSE) is a critical aspect of every workplace, aimed at ensuring the well-being of employees, contractors, visitors, and the surrounding environment. The core principles of health and safety management are to prevent accidents, injuries, and occupational diseases while fostering a culture of safety within organizations. By focusing on risk assessment, preventive measures, legal compliance, and employee engagement, organizations can significantly reduce workplace hazards and improve productivity. This article outlines the key elements that make up the essentials of health and safety at work, providing an overview of the necessary measures for maintaining a safe working environment.
Legal Framework and Compliance
The foundation of workplace health and safety lies in legal frameworks established by local and international regulations. These laws define the responsibilities of employers, employees, and contractors in ensuring safe working conditions. The most prominent regulations include the Occupational Safety and Health Act (OSHA) in the U.S., Health and Safety at Work Act in the UK, and various international standards such as the ISO 45001 for occupational health and safety management systems.
Employers are required to comply with these regulations by providing a safe work environment, conducting regular risk assessments, and taking necessary actions to minimize health and safety risks. Additionally, they must ensure that workers are adequately trained, provided with personal protective equipment (PPE), and made aware of potential hazards in the workplace. Regular audits and inspections are conducted to assess compliance and rectify any violations.
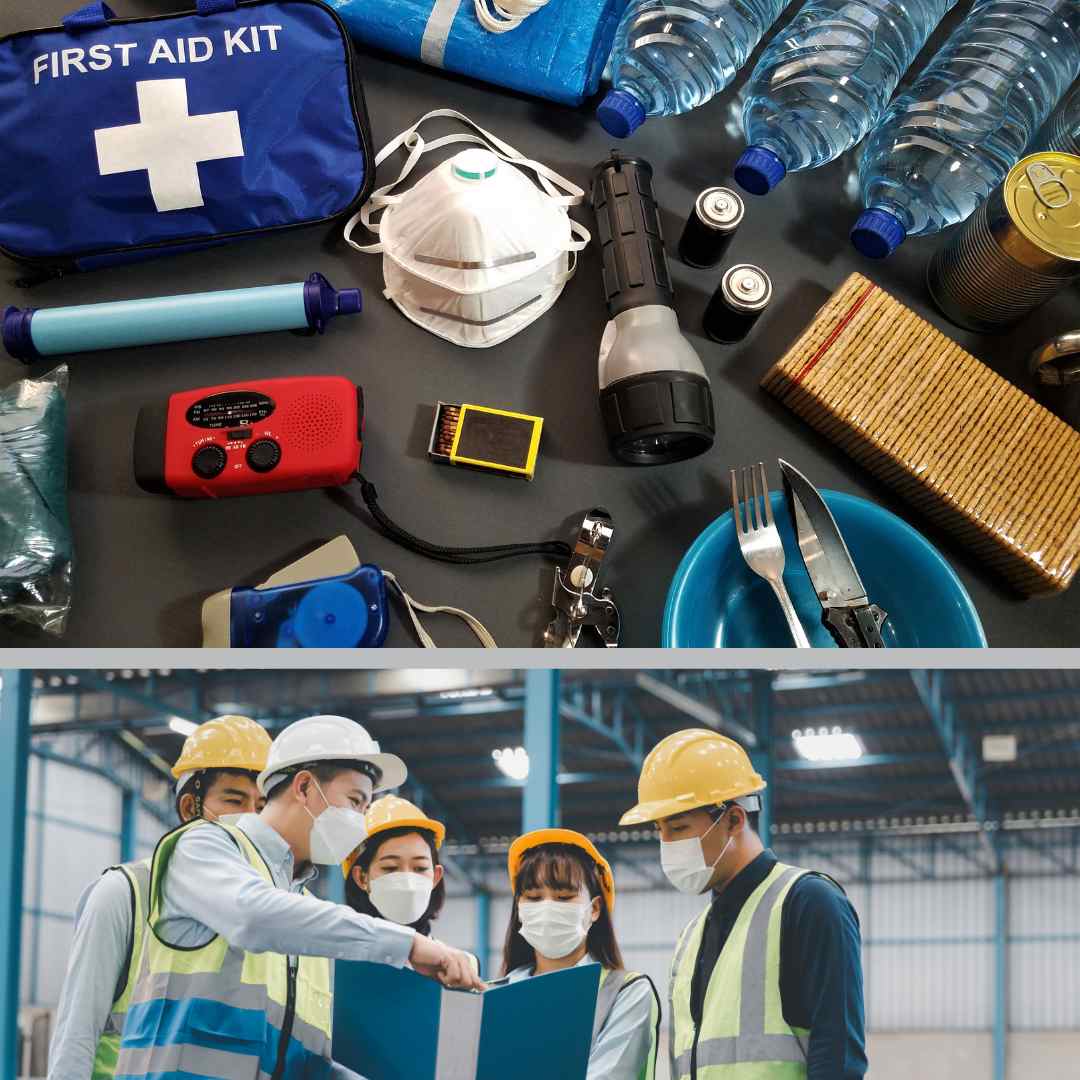
Risk Assessment and Hazard Identification
A cornerstone of any effective health and safety program is identifying potential hazards and assessing risks associated with workplace activities. Risk assessments must be systematic and thorough, focusing on both physical and environmental hazards, as well as human factors. These assessments typically involve the following steps:
- Hazard Identification: This includes identifying anything in the workplace that could cause harm, such as machinery, chemicals, electrical equipment, or ergonomic issues.
- Risk Evaluation: Once hazards are identified, the next step is to evaluate the likelihood and severity of the risks they pose to health and safety. This evaluation helps in prioritizing risks that need immediate attention.
- Control Measures: After assessing the risks, appropriate control measures are implemented. These could include elimination of the hazard, substitution with safer alternatives, engineering controls (e.g., ventilation or machine safety guards), administrative controls (e.g., job rotation), or the use of PPE.
Health and Safety Training and Awareness
Education is vital for maintaining a safe workplace. Workers must be trained to recognize potential hazards, use safety equipment properly, and follow safe work practices. Training should be tailored to specific roles and hazards associated with different industries. For example:
- Induction Training: All new employees must receive induction training on health and safety practices, emergency procedures, and the location of safety equipment.
- Task-Specific Training: Employees should be trained to handle specific risks related to their job tasks, such as safe lifting techniques, chemical handling procedures, or machine operation.
- Emergency Response: Training workers in emergency procedures, including fire drills, first aid, evacuation protocols, and the proper use of fire extinguishers, is critical for ensuring quick and effective responses during incidents.
In addition to formal training programs, regular safety briefings and refresher courses should be provided to reinforce knowledge and ensure that safety practices are up-to-date.
Personal Protective Equipment (PPE)
PPE is a vital component of workplace health and safety. It includes protective clothing, helmets, gloves, goggles, hearing protection, and respiratory protection, designed to reduce exposure to various hazards. PPE is typically used when other control measures, such as engineering controls or administrative changes, are not sufficient or feasible.
The selection of PPE should be based on the nature of the hazards present in the workplace. For instance, workers in construction sites or manufacturing plants might require hard hats, steel-toed boots, hearing protection, and respiratory masks, whereas workers in chemical labs may need chemical-resistant gloves, face shields, and aprons.
It is essential to ensure that PPE is maintained in good condition, fits the individual worker properly, and is used consistently in situations where it is required. Training in proper usage, maintenance, and disposal of PPE is necessary to ensure its effectiveness.
Health and Wellness Programs
Beyond physical safety, health and wellness programs play an important role in workplace health. These programs focus on preventing illnesses, promoting physical and mental well-being, and encouraging healthier lifestyles. Examples of health and wellness initiatives include:
- Ergonomics: Implementing ergonomic practices in the workplace to reduce strain and prevent musculoskeletal disorders. This includes providing adjustable desks, seating, and proper tools to minimize repetitive stress injuries.
- Mental Health Support: Offering mental health resources, such as counseling services, stress management workshops, and creating a supportive work environment, can significantly improve employee well-being.
- Occupational Health Surveillance: Regular health checks and screenings, such as hearing tests or lung function tests, help in the early detection of work-related diseases, ensuring that employees receive timely medical care.
Accident Reporting and Investigation
An essential component of a successful health and safety program is the ability to track and analyze accidents and near-misses. Employers should encourage workers to report any incidents, even if they do not result in injury, to prevent future occurrences. Accidents should be investigated thoroughly to determine root causes, such as human error, equipment failure, or environmental factors.
Accident investigations typically involve:
- Root Cause Analysis: Identifying underlying causes beyond the immediate factors leading to the incident.
- Corrective Actions: Implementing changes to prevent similar incidents from occurring, whether through process changes, equipment upgrades, or additional training.
- Documentation: Maintaining detailed records of incidents, including reports, corrective actions, and any lessons learned, is essential for compliance and continuous improvement.
Emergency Procedures and First Aid
Emergency procedures are a crucial part of health and safety at work. Employers must establish clear protocols for responding to accidents, fires, medical emergencies, or natural disasters.
Key elements of emergency procedures include:
- Evacuation Plans: Clear instructions on evacuation routes, assembly points, and protocols for accounting for all employees during an emergency.
- First Aid: Employers should ensure that designated first aiders are available, and first aid kits are stocked and easily accessible.
- Fire Safety: Fire extinguishers, alarms, and fire exits must be in place, and employees should be trained in fire safety procedures.
Continuous Improvement and Safety Culture
A strong safety culture is the cornerstone of an effective HSE program. Safety should be integrated into the organizational values and daily operations, with management leading by example and promoting a proactive approach to health and safety. Regular safety audits, employee feedback, and ongoing training contribute to continuous improvement.
Organizations must:
- Encourage Employee Participation: Involve employees in safety meetings, hazard identification, and decision-making processes regarding safety policies.
- Foster a Reporting Culture: Promote a non-punitive environment where employees feel comfortable reporting hazards or incidents without fear of retaliation.
- Monitor Safety Performance: Use key performance indicators (KPIs) such as injury rates, near-miss reports, and safety audit results to track and improve safety outcomes.
Conclusion
Health and safety at work are essential components of a successful and sustainable workplace. By following established safety regulations, identifying risks, providing the right PPE, and fostering a culture of safety, organizations can ensure that their employees work in an environment that promotes health, well-being, and productivity. A proactive approach to health and safety not only protects workers but also contributes to the long-term success of the organization by reducing accidents, improving employee morale, and maintaining legal compliance.