Introduction to Compressor Technology
Compressor technology is central to a wide range of industries—power generation, manufacturing, HVAC, oil & gas, and even daily tools like refrigerators and air conditioners. Compressors serve one fundamental purpose: to increase the pressure of a gas by reducing its volume. But the variety of compressor types and their applications make the field both vast and intricate. This guide provides a hands-on overview of compressor types, working principles, selection considerations, and maintenance practices for engineers, technicians, and workshop professionals.
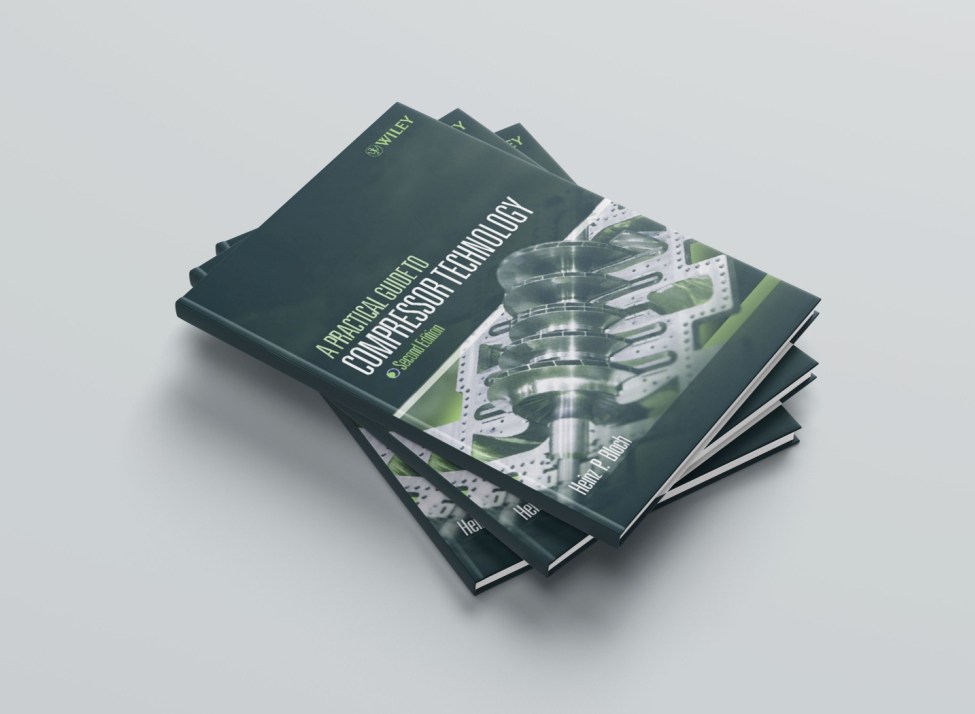
Understanding the Basics
What is a Compressor?
A compressor is a mechanical device that increases the pressure of a gas (often air) by reducing its volume. Unlike pumps, which work on liquids, compressors work exclusively on gases, as gases are compressible and can be squeezed into a smaller volume.
Applications of Compressors
- Pneumatic tools (air drills, grinders)
- Gas transmission pipelines
- Refrigeration and air conditioning systems
- Power plant gas turbines
- Industrial automation systems
Types of Compressors
Compressors are broadly categorized into positive displacement and dynamic types.
1. Positive Displacement Compressors
These compressors trap a fixed amount of gas and then reduce the volume.
a. Reciprocating Compressors
- Operate with a piston-cylinder mechanism
- Suitable for high-pressure, low-volume tasks
- Common in small workshops and gas transmission
- Reciprocating Compressors
b. Rotary Screw Compressors
- Use twin helical screws to compress gas
- Ideal for continuous-duty, industrial-grade air supply
- Quieter and more compact than reciprocating types
c. Rotary Vane Compressors
- Employ a rotor with adjustable vanes inside a cavity
- Simpler design and fewer parts
- Well-suited for mid-pressure applications
2. Dynamic Compressors
These rely on velocity and kinetic energy to compress gas.
a. Centrifugal Compressors
- Use high-speed impellers to impart energy to the gas
- Excellent for high-volume, low-pressure applications
- Common in HVAC systems and process industries
b. Axial Compressors
- Compress gas along the axis of rotation through multiple blade rows
- High efficiency and flow rates
- Found in jet engines and large gas turbines
Thermodynamics of Compression
Compressors work under thermodynamic principles governed by the gas laws:
- Isentropic compression: Ideal scenario (no heat exchange)
- Polytropic compression: Real-world process with heat transfer
- Adiabatic vs. Isothermal: Defines heat interaction during compression
Work required for compression depends on:
- Inlet and outlet pressures
- Gas type and molecular weight
- Number of compression stages
Multistage compressors are often used when the pressure ratio is high, with intercooling between stages to improve efficiency.
Key Components of a Compressor
- Inlet Filter: Removes dust and particles
- Compressor Element: Main mechanical component (piston, screw, impeller)
- Intercooler/Aftercooler: Cools the gas between stages or after compression
- Lubrication System: Ensures smooth movement and minimizes wear
- Control System: Regulates pressure, flow, and safety parameters
Selecting the Right Compressor
When choosing a compressor, consider:
Parameter | Recommendation |
---|---|
Flow Rate (CFM) | Match to tool/system requirements |
Pressure (PSI/Bar) | Choose based on end-use demand |
Duty Cycle | Intermittent (reciprocating) or continuous (screw) |
Energy Source | Electric motor or internal combustion |
Environment | Indoor, outdoor, corrosive, or explosive |
Maintenance Access | Choose designs with easy servicing |
Compressor Maintenance Essentials
Regular maintenance not only extends the life of compressors but also ensures safety and reliability.
Routine Maintenance Tasks
- Check and replace air filters
- Inspect belts and couplings
- Monitor and top-up lubricant levels
- Drain condensate from tanks
- Clean intercoolers and aftercoolers
- Monitor vibration and noise levels
- Inspect safety valves and control systems
Troubleshooting Common Issues
- Low Pressure Output: Check intake restrictions, leaks, and valves
- Overheating: Inspect for clogged coolers, poor ventilation, or low oil
- Noisy Operation: Bearings, loose parts, or internal wear
- Oil Carryover: Damaged seals or improper lubricant type
Energy Efficiency Considerations
Compressed air is one of the most expensive utilities in many industrial plants. Improving energy efficiency can result in substantial cost savings.
- Use variable speed drives (VSD)
- Fix leaks in the distribution system
- Properly size the compressor for the load
- Recover heat from compressor cooling systems
- Use high-efficiency motors
Conclusion 📘
Understanding compressor technology is vital for engineers and technicians working in industrial, energy, and mechanical systems. Whether selecting a compressor for a specific job or maintaining a large-scale gas compression system, the principles of thermodynamics, mechanical design, and operational efficiency all play a role. With the right knowledge, you can ensure optimal performance, safety, and longevity of these essential machines.