Basic Concepts Of Industrial Hygiene
The Historical View and Basis of Industrial Hygiene
Industrial hygiene traces its roots to ancient times when early physicians and scholars observed the relationship between work and health. Hippocrates recognized the hazards of lead exposure, and Pliny the Elder noted the dangers of inhaling toxic dust. However, the discipline truly evolved during the Industrial Revolution as mechanized factories introduced new hazards. Today, industrial hygiene is a well-established field supported by scientific research and regulatory frameworks that prioritize worker health and safety.
Understanding Toxic Effects and Risk Assessment
Toxic substances in the workplace can cause a wide range of health issues, from acute effects like chemical burns and poisoning to chronic conditions such as organ damage and cancer. The severity of these effects depends on factors like exposure duration, dosage, and the route of entry, whether inhalation, ingestion, or skin absorption. Measuring relative toxicity through dose-response studies and conducting risk assessments are essential to understanding and mitigating these dangers, ensuring safer workplace practices.
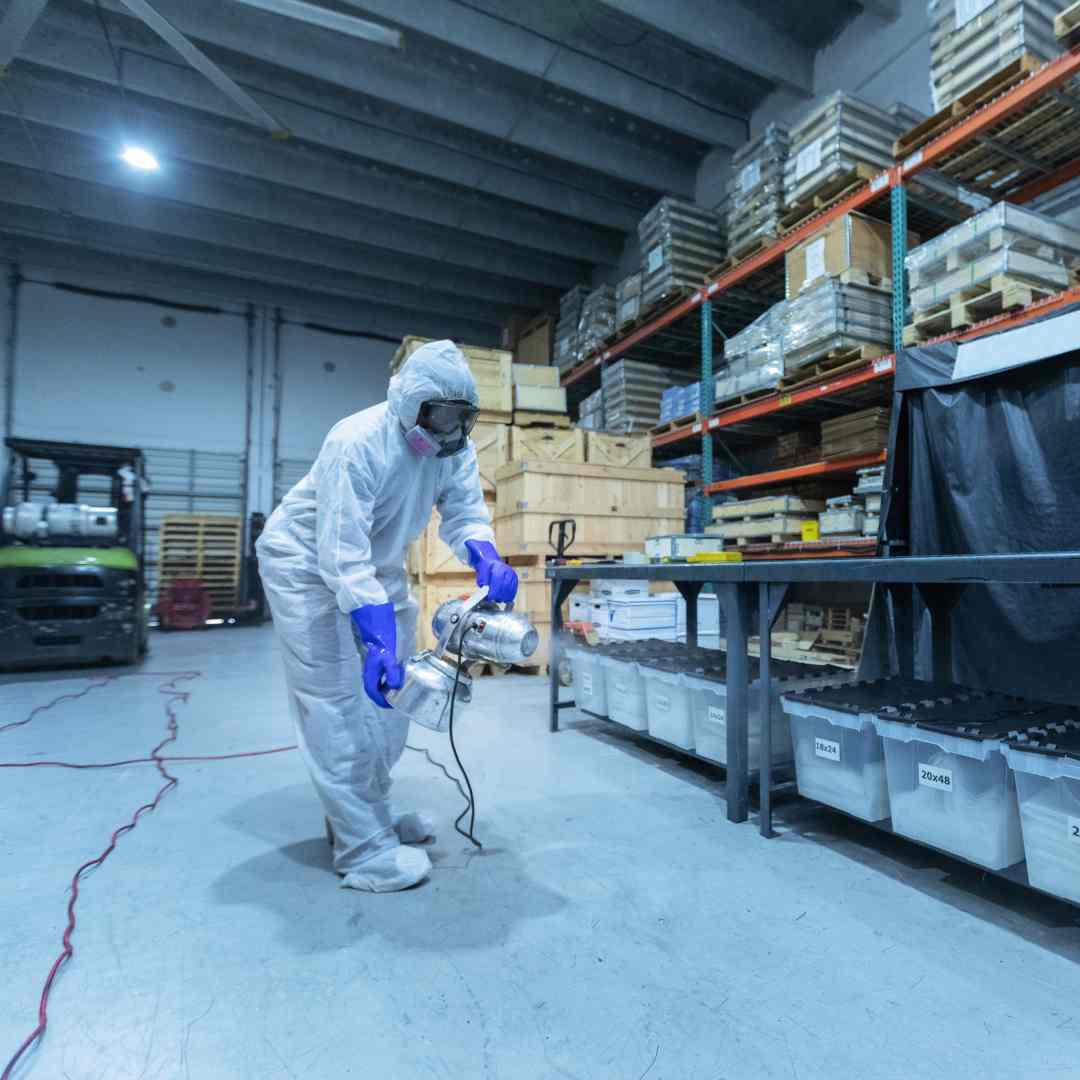
Protecting Workers: Clean Air and Monitoring
Monitoring workplace air quality is crucial in identifying and controlling harmful exposures. Regular air sampling and the use of gas detectors help assess the levels of toxins, ensuring timely interventions. Equally important is providing clean air through advanced ventilation systems, air purifiers, and local exhaust controls. These measures not only protect workers from respiratory hazards but also promote a healthier and more productive work environment.
Occupational Dermatosis and Eye Hazards
Workers in many industries face risks of skin and eye exposure to harmful chemicals, irritants, and allergens. Occupational dermatosis, such as contact dermatitis, arises from repeated contact with hazardous substances. Similarly, eye hazards include exposure to chemical splashes, dust, and UV radiation. Mitigating these risks involves using protective gear like gloves, goggles, and face shields, along with training workers on safe handling practices.
Ergonomics and Cumulative Trauma
Ergonomic risks, such as repetitive strain injuries and musculoskeletal disorders, are common in workplaces with poorly designed tasks or workstations. Conditions like carpal tunnel syndrome arise from repetitive motions or awkward postures over time. Addressing these issues requires ergonomic interventions, including adjustable workstations, proper training on body mechanics, and tools designed to reduce strain. By improving workplace ergonomics, employers can enhance employee comfort, reduce injury rates, and boost overall efficiency.
Ergonomics and Accident Prevention
Prevention of Accidents
- Safety programs emphasizing hazard identification, worker training, and equipment maintenance reduce accident rates.
Cumulative Trauma
- Repetitive strain injuries, like carpal tunnel syndrome, arise from poorly designed workstations or repetitive tasks.
- Ergonomic interventions improve workplace design to prevent such injuries.
Radiation Protection and Extreme Temperatures
Workers exposed to radiation, whether ionizing or non-ionizing, face significant health risks, including cancer and tissue damage. Protective measures, such as the use of lead shielding, dosimeters, and maintaining a safe distance from radiation sources, are essential. Similarly, extreme temperature environments, whether hot or cold, pose risks like heat stroke, hypothermia, or frostbite. Engineering controls such as climate-controlled facilities and providing suitable PPE help protect workers in these challenging conditions.
Industry-Specific Hazards
Metals: Metals Preparation and Manufacturing
- Metalworking exposes workers to risks such as heavy metal toxicity and physical injuries from sharp edges.
- Proper ventilation, protective gear, and process controls are essential.
Welding and Cutting Safety
- Welding processes generate harmful fumes, heat, and UV radiation.
- Engineering controls like local exhaust ventilation and PPE like welding helmets are critical.
Polymers
- Polymer manufacturing involves chemical processes that may release hazardous monomers or byproducts.
- Continuous monitoring and the use of closed systems reduce exposure risks.