Pressure vessels and Boiler Inspection are done to determine the amount of maintenance required to have equipment operate properly until the next turnaround. A comprehensive equipment history must be maintained that includes conditions found during inspection and testing, maintenance work done, changes made, and date of each. ASME Code Standards require boiler inspection to be done at least every year. There is no mandatory inspection requirements for heaters. Inspection intervals are based on service and experience.
Boiler Inspection is not an exact science and requires the use of judgement and experience.
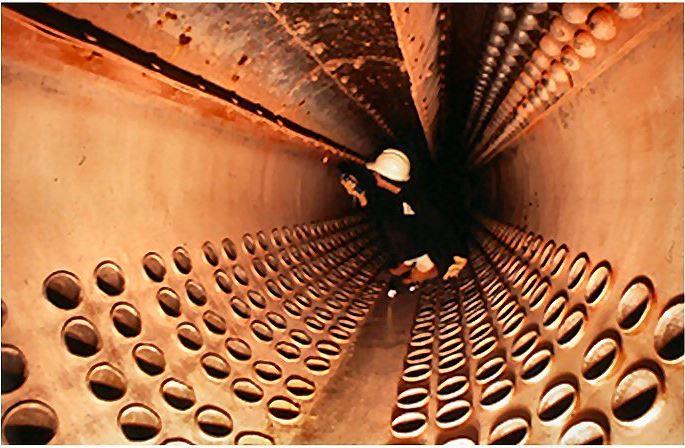
Firebox
Tube and Drum External Inspection
Tubes are inspected externally for excessive fire scale (fireside scale), deformation (bulging) or sagging that may indicate overheating. Sagging roof tubes are especially susceptible to overheating. Drums and shells are inspected externally for excessive fire scale, cracking of joints and any indication of leakage (deposits) at the tube to drum connections.
The tube and drum thickness are measured ultrasonically to determine a corrosion rate. Tube samples may be taken for inspection of the metal deterioration and measurement of deposits.
Tubes and drums are inspected at support points to see if there is any binding or wear. Supports are inspected for corrosion and damage and to make sure they are functioning properly.
Firebox Refractory/Insulation
Refractory and insulation are inspected to determine if there is any deterioration. Refractory is inspected for breakage, slagging, crumbling, spalling, and open joints. Leakage of hot boiler gases through joints when the edges have crumbled or when the tile or insulating concrete has fallen out may expose the supporting steel to high metal temperatures, rapid oxidation, and corrosion.
Fly-ash corrosion may occur when fly-ash and refractory are in contact. Fluxing occurs and produces a slag that may be fluid at boiler operating conditions. Metal oxides found in fuel oil are fluxing agents. The general effect of slagging is to decrease the thickness of the refractory and thereby reduce its insulation properties. Slagging may cause rapid deterioration of boiler hardware such as tube hangers and spacers.
Severe spalling will require repair. Spalling of refractory usually results from a startup heatup being done too rapidly. Spalling can also result from overheating by direct flame impingement. Sagging would indicate problems with the refractory/insulation support. Support problems can be caused by overheating or corrosion of the supports.
External deposits may indicate the need for external water washing. The water washing procedure includes sealing the refractory with a bitumen sealer to prevent water damage of the refractory and the use of 0.5% soda ash solution to minimize stress cracking of austenetic steels such as stainless steels. Under no circumstances is salt or raw water to be used for water washing. The bitumen sealer is burned off in normal operation.
External firebox insulation is inspected for rust spots, cracking and bulging that may indicate corrosion beneath the insulation.
Fire Scale
Tubes are externally inspected for excessive fire scale. Fire scale may indicate the metal has experienced high temperatures and has oxidized. Areas with heavy fire scale should be carefully inspected and monitored for corrosion. Ultrasonic measurements should be taken.
Boiler Convection Section Deposits
The convection section is inspected for deposits especially when oil has been fired. There may be deposits that are not readily removed by water washing. Ash from fuel oil firing can form a glass like deposit which may be very difficult to remove even with chemical cleaning. Sometimes the tubes must be replaced. Any damage to the extended surfaces should be noted for evaluation of required maintenance.
Boiler Steam Mud Drum Deposits
Boiler steam and mud drums and the tube ends are inspected for deposits. The boiler inspection may indicate the need for chemical cleaning to remove deposits. Severe deposits indicate the need to review boiler water treatment and blowdown controls.
Thickness Measurement
Thickness measurements are made to detect corrosion as shown in picture.
Ultrasound – Ultrasound measurements
Ultrasound measurements of boiler tube and drum metal thickness are taken to establish an average corrosion rate of tubes and drums. Normal ultrasound measurements indicate an average metal thickness but may not give any indication of pitting or cracking.
Pitting and Cracking
Boiler Inspection for pitting and cracking includes radiographic examination, magnetic particle examination (magnaflux), and liquid penetrant examination. Welds may be radiographed (x-ray) to determine cracks and penetration of welds. Magnetic particle inspection
and liquid dye penetrant inspections are used to locate small surface cracks especially in autenistic steels. A pit gauge is used to measure the depth of pits.
Tube Deposits scale
Boiler tubes can be internally inspected by a fiberscope type of instrument that can give a TV picture of the inside of the tubes. Sometimes sections or tubes may be cut out for inspection and replacement. Internal boiler scale (deposits) may indicate the need for chemical cleaning. The tube in Figure 3 is in definite need of chemical cleaning.
Boiler Hydrostatic Testing
Once maintenance has been completed the furnace or boiler is hydrotested at 1.5 times the design or maximum allowable working pressure to make sure there are no leaks. Read Boiler Hydrostatic Testing procedure.
Bench Test
The ASME code requires testing of boiler pressure relief valve and safety valves. All boiler PZVs must be tested in place for the final set pressure and blowdown (reseating) adjustments as required by the ASME code. The in-place test is performed as per a written approved operating procedure. The in-place test has provisions to prove full lift capacity and accuracy of adjustments. Read Boiler Books