Boiler refractory dry out is a critical process to ensure the longevity and optimal performance of the refractory lining within a boiler. It involves a controlled heating schedule to remove moisture, cure the refractory, and allow it to achieve its designed strength and integrity.
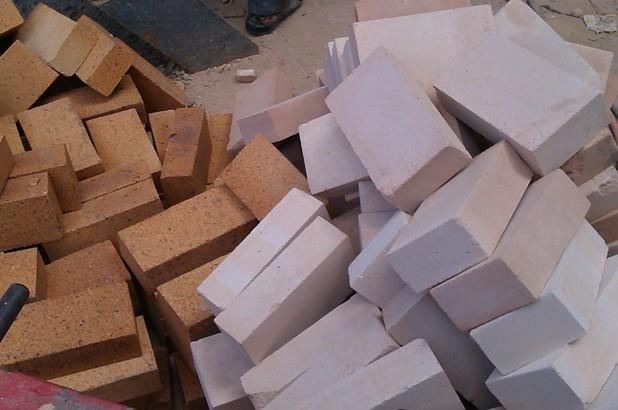
The article provides a good overview of the dry-out procedure, emphasizing the importance of slow and controlled heating. Here’s an expanded version with additional details and considerations:
Boiler Refractory Dry Out Procedure: Expanded Guidelines
Boiler refractory dry out is to ensure proper drying and curing of refractory applied on furnace and other components. The refractory usually undergoes considerable chemical changes during initial heating. Controlled heating, through these reactions, ensures maximum strength. While heating, there must be free air flow over the system to ensure removal of moisture.
Prior to Commencing Refractory Dry Out:
In order to commence refractory dry out, the following pre-requisites and inputs have to be ensured:
- Pre-commissioning Checks: All pre-commissioning checks for the boiler and its auxiliary systems should have been completed and verified. This includes, but is not limited to, hydro testing, cleaning, and flushing of boiler tubes and headers.
- Resource Availability:
- Feed Water: Ensure the availability of adequate feed water as per the recommendation of the boiler supplier. The water quality must meet boiler manufacturer specifications to prevent scaling or corrosion during the dry-out process.
- Fuel: Adequate dry wooden logs of the required sizes (typically 2-3 inches diameter and 2-3 feet length), free from nails, packing metal strips, or any other contaminants, must be readily available. If alternative fuels are to be used (e.g., natural gas, oil), ensure the respective firing equipment is operational and fuel supply is secured.
- Draft System: The ID (Induced Draft) and FD (Forced Draft) fans, along with their associated controls and dampers, must be fully functional and tested.
- Instrumentation: All instruments required for boiler firing and monitoring, such as pressure gauges, temperature indicators (flue gas, drum, refractory surface), oxygen analyzers, and flow meters, must be calibrated and in good working order.
- Personnel: Ensure the availability of adequate qualified boiler operating staff and supervisors who are experienced in boiler operation and refractory dry-out procedures. They should be thoroughly familiar with the dry-out schedule and safety protocols.
- Ventilation: Keep all vent lines (100% open) on the boiler drum, top superheater header, and any other high points throughout the refractory dry-out period. This is crucial for releasing steam and preventing pressure build-up within the boiler.
- Safety Precautions:
- Implement a strict lock-out/tag-out procedure for all relevant equipment.
- Ensure proper ventilation in the boiler house to prevent accumulation of combustion gases.
- Have fire-fighting equipment readily available and personnel trained in its use.
- Establish clear communication protocols among the operating team.
- Ensure all personnel wear appropriate personal protective equipment (PPE).
Procedure for Boiler Refractory Dry Out:
Refractory baking and dry out cycle requires very slow and controlled heating of refractory as recommended by the refractory manufacturers. Thermal stresses will be produced if heating rate is too rapid, leading to cracking and spalling. Longer periods of low-temperature drying cause more even heat distribution, resulting in better refractory dry out.
- Boiler Filling: Fill the drum with the specified quality feed water to approximately 50mm below the normal water level. The water level in the gauge will rise as heat is absorbed, so monitoring is crucial. Maintain a consistent water level in the drum throughout the dry-out period, adding feed water as needed.
- Initial Firing: Place dry firewood evenly on the grate. Avoid stacking too much wood initially to prevent rapid temperature spikes. Start ID and FD fans at minimum load to establish a slight negative draft and provide combustion air for lighting up the boiler.
- Controlled Heating Schedule (Example – always follow manufacturer’s curve):
- Stage 1: Initial Drying (Moisture Removal)
- Heating Rate: Ensure that the rate of heating is maintained at a very slow and controlled rate, typically 25°C per hour (or as specified by the refractory manufacturer). This slow rate is critical for allowing moisture to evaporate gradually without causing internal pressure build-up within the refractory, which can lead to explosive spalling.
- Hold Temperature 1: Raise the temperature of the flue gas at the boiler outlet to 100°C (212°F).
- Hold Time 1: Hold this temperature for 8-12 hours (or as per manufacturer’s recommendation) for soaking refractory castables. During this phase, free water within the refractory evaporates. Ensure continuous monitoring of flue gas temperature. If the temperature falls, slightly increase the firing rate to maintain the required temperature.
- Stage 2: Dehydration and Curing (Chemical Water Removal)
- Heating Rate: Continue to raise the flue gas temperature at the boiler outlet at the controlled rate of 25°C per hour.
- Hold Temperature 2: Raise the flue gas temperature at the boiler outlet to 250°C (482°F).
- Hold Time 2: Hold this temperature for 6-8 hours for further soaking and the initial stages of chemical water removal. This phase addresses chemically bound water within the refractory.
- Stage 3: Sintering and Strengthening
- Heating Rate: Continue to raise the flue gas temperature at the boiler outlet at the controlled rate of 25°C per hour.
- Hold Temperature 3: Raise the flue gas temperature at the boiler outlet to 350°C (662°F).
- Hold Time 3: Hold this temperature for 10-12 hours (or as per manufacturer’s recommendation) for final soaking and sintering of the refractory castables. This stage allows the refractory to achieve its maximum strength and density.
- Stage 4: Final Soaking (Optional, higher temperatures for specific refractories)
- Some refractory types may require a higher final hold temperature (e.g., 450-500°C) for a shorter duration (e.g., 4-6 hours) to ensure complete curing and sintering. Always refer to the refractory manufacturer’s specific dry-out curve.
- Stage 1: Initial Drying (Moisture Removal)
- Monitoring During Dry Out:
- Flue Gas Temperature: Continuously monitor the flue gas temperature at the boiler outlet using a calibrated thermocouple or RTD. This is the primary parameter for controlling the heating rate.
- Refractory Surface Temperature: Where possible, monitor the surface temperature of the refractory at various locations using infrared thermometers or embedded thermocouples. This helps in understanding the heat distribution and identifying any localized overheating.
- Steam/Moisture Observation: Observe the boiler stack for the presence of steam. As the dry-out progresses, the visible steam plume should diminish, indicating successful moisture removal.
- Draft Monitoring: Ensure stable draft conditions throughout the process to facilitate proper combustion and removal of combustion products.
- Water Level: Continuously monitor and maintain the drum water level.
- Cool Down: Once the heating schedule is completed and all hold times have been observed, the fire is extinguished. The boiler must be allowed to cool down naturally. Do not use fans (FD, ID, SA) during cooldown unless explicitly recommended by the manufacturer for specific reasons, as rapid cooling can induce thermal shock and cracking. Fan auxiliary dampers should be in a fully closed condition to minimize cold air ingress.
- Post-Dry Out Inspection:
- After the boiler has completely cooled down to ambient temperature, a thorough visual examination is to be made to check the refractory condition.
- Look for any signs of cracking, spalling, or debonding.
- Minor cracks (typically up to 3mm in width) are generally acceptable and can be filled with suitable castable refractory as per manufacturer guidelines. Larger cracks or widespread damage may indicate issues during the dry-out process and require more extensive repairs or even reapplication of refractory.
- Tap the refractory surface gently with a light hammer to check for any hollow sounds, which could indicate delamination.
Important Considerations and Best Practices:
- Refractory Manufacturer’s Curve: Always, without exception, follow the specific refractory dry-out curve provided by the refractory manufacturer. This curve is tailored to the specific chemical composition and properties of the refractory material used. Deviating from it can lead to permanent damage and reduced refractory life.
- Documentation: Maintain a detailed log of the entire dry-out process, including:
- Start and end times of each heating stage and hold period.
- Flue gas temperatures at regular intervals.
- Any observations (e.g., steam evolution, unusual sounds, visible cracks).
- Actions taken (e.g., firing rate adjustments, feed water additions).
- Personnel involved.
- Atmospheric Conditions: While dry out is primarily about controlled heating, extremely humid external conditions can sometimes affect the efficiency of moisture removal.
- Multi-Zone Refractory: If the boiler has different types of refractory in various zones (e.g., furnace floor, walls, roof), ensure that the dry-out procedure adequately addresses the requirements of all refractory types, often driven by the most sensitive or critical refractory.
- Emergency Procedures: Have clear emergency procedures in place in case of unexpected events during the dry-out, such as rapid temperature excursions or equipment malfunctions.
By meticulously following these expanded guidelines, boiler operators can ensure a successful refractory dry-out, leading to enhanced boiler reliability and operational efficiency.
Refractory dry out should be carried out as per the curve given by Refractory manufacturer.