Combined Cycle Systems for the Utility Industry: Enhancing Efficiency and Performance
The utility industry plays a critical role in supplying electricity to meet the growing global demand. One of the most innovative advancements in power generation is the Combined Cycle Power Plant (CCPP). By integrating both gas turbines and steam turbines, combined cycle systems deliver superior efficiency, reduced emissions, and operational flexibility compared to conventional single-cycle plants. This article explores the components, operational principles, and benefits of combined cycle systems in the utility industry.
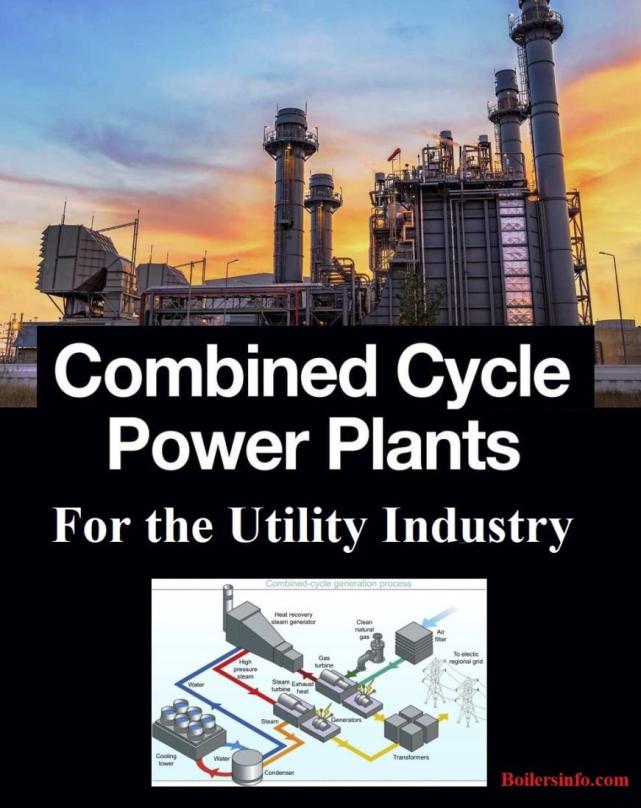
What is a Combined Cycle Power Plant?
A Combined Cycle Power Plant (CCPP) is a highly efficient electricity generation system that combines both gas turbine and steam turbine technologies. The core concept of the combined cycle system involves utilizing two thermodynamic cycles to generate power:
- Gas Turbine Cycle (Brayton Cycle): The gas turbine burns fuel to generate electricity.
- Steam Turbine Cycle (Rankine Cycle): The waste heat from the gas turbine exhaust is used to produce steam, which drives a steam turbine to generate additional electricity.
By harnessing the exhaust heat from the gas turbine to produce steam, the combined cycle system significantly improves overall efficiency, making it one of the most energy-efficient ways to generate power in the utility industry.
Components of a Combined Cycle Power Plant
1. Gas Turbine
The gas turbine is the first key component in a combined cycle system. It burns fuel (typically natural gas or oil) in a combustion chamber, generating hot gases that drive the turbine. The turbine is connected to a generator that produces electricity.
- Operation: The combustion gases pass through the turbine, where their thermal energy is converted into mechanical energy. The exhaust gases then exit at high temperatures, which are used for the steam cycle.
- Fuel: Natural gas is the preferred fuel due to its lower emissions compared to coal or oil.
2. Heat Recovery Steam Generator (HRSG)
The Heat Recovery Steam Generator (HRSG) is a crucial component that captures the exhaust heat from the gas turbine to produce steam. It essentially functions as a heat exchanger, transferring the thermal energy from the exhaust gases to water or feedwater to create steam.
- Operation: The hot exhaust gases from the gas turbine pass through the HRSG, where they heat water in tubes. This process produces steam, which is directed to the steam turbine.
- Efficiency: The HRSG significantly increases plant efficiency by utilizing waste heat that would otherwise be wasted.
3. Steam Turbine
Once the steam is generated by the HRSG, it is directed to the steam turbine. The steam turbine operates on the Rankine Cycle, where the steam expands in the turbine, generating mechanical energy that drives a generator to produce additional electricity.
- Operation: The steam passes through the steam turbine blades, causing them to spin and convert thermal energy into mechanical energy.
- Energy Recovery: This recovery of waste heat to generate electricity is what gives combined cycle plants their significant efficiency advantage.
4. Generator
Both the gas and steam turbines are coupled to generators that convert mechanical energy into electrical energy. These generators provide the necessary electricity output for the grid.
- Operation: The mechanical energy from the turbines drives the generator’s rotor, which induces a current in the stator, generating electricity.
5. Auxiliary Equipment
The plant’s operation relies on a range of ancillary equipment, including pumps, compressors, cooling systems, and fuel delivery systems. These ensure the turbines, HRSG, and other components operate smoothly and efficiently.
- Fuel Delivery: Natural gas or other fuels are supplied to the gas turbine via a well-designed fuel system.
- Cooling Systems: Condensers and cooling towers help remove waste heat from the system, particularly from the steam cycle, to maintain efficient operation.
The Brayton and Rankine Cycles in Combined Cycle Systems
1. Brayton Cycle (Gas Turbine Cycle)
The Brayton Cycle is the thermodynamic cycle used in the gas turbine. It involves compressing air, mixing it with fuel, and then igniting the mixture in a combustion chamber. The high-temperature, high-pressure gases that result from this combustion process are expanded through a turbine to generate power.
- Efficiency: The Brayton Cycle is efficient at converting energy from high-temperature combustion gases into mechanical energy.
2. Rankine Cycle (Steam Turbine Cycle)
The Rankine Cycle is used in the steam turbine. In this cycle, steam is generated by the HRSG and expanded through the steam turbine to produce mechanical energy. The steam is then condensed back into water in a condenser and recirculated to the HRSG to be reheated.
- Efficiency: The Rankine Cycle allows for additional electricity generation from waste heat, improving the overall efficiency of the combined cycle plant.
Performance Characteristics of Combined Cycle Power Plants
- Efficiency
Combined cycle plants are among the most efficient power generation systems, often achieving efficiency levels of 60% or higher compared to 33-40% for conventional steam-only plants. - Flexibility
Combined cycle plants can quickly adjust to changes in demand, making them ideal for peaking plants and backup power generation. The integration of both cycles allows for quick starts and stops. - Lower Emissions
The higher efficiency and lower fuel consumption in combined cycle systems contribute to reduced greenhouse gas emissions. Natural gas, the most commonly used fuel in CCPPs, produces less CO₂ compared to coal-fired plants.
Advantages of Combined Cycle Power Plants
- High Efficiency
The main advantage of combined cycle systems is their efficiency. By recovering waste heat from the gas turbine, these plants can achieve efficiencies exceeding 60%, making them more cost-effective and environmentally friendly. - Lower Operational Costs
The increased efficiency leads to reduced fuel consumption, lower operational costs, and reduced need for fuel transport, making combined cycle plants highly competitive. - Environmental Benefits
By burning natural gas instead of coal, combined cycle plants produce fewer emissions, contributing to cleaner air and meeting stringent environmental regulations. - Quick Start-Up Times
Combined cycle plants are highly responsive, offering quick start-up times. This makes them suitable for providing peak load power or backup power when needed.
Applications of Combined Cycle Power Plants
- Utility Companies: Combined cycle plants are ideal for utilities seeking to balance base load and peak demand generation efficiently.
- Industrial Applications: Many industries use combined cycle plants to provide on-site power, enhancing energy security and reducing operational costs.
- Energy Storage: The ability to ramp up quickly and efficiently makes combined cycle systems a valuable component in energy storage solutions, particularly in integration with renewable energy sources.
Conclusion
Combined cycle power plants are a cornerstone of modern power generation, offering unmatched efficiency, flexibility, and environmental benefits. By integrating gas and steam turbines, these systems maximize energy output while minimizing waste. Their ability to adapt to demand fluctuations, combined with their high efficiency, positions them as a key technology in the utility industry’s transition towards cleaner, more sustainable energy systems.
As the world moves towards greener energy solutions, the role of combined cycle power plants in reducing emissions and optimizing fuel use will only become more critical.