Welding is a precise and skill-intensive process used across industries for joining metals. However, even skilled welders may encounter defects that compromise the strength, safety, or appearance of welded joints. This article explores a wide range of common and critical welding defects, their causes, and tips for prevention.
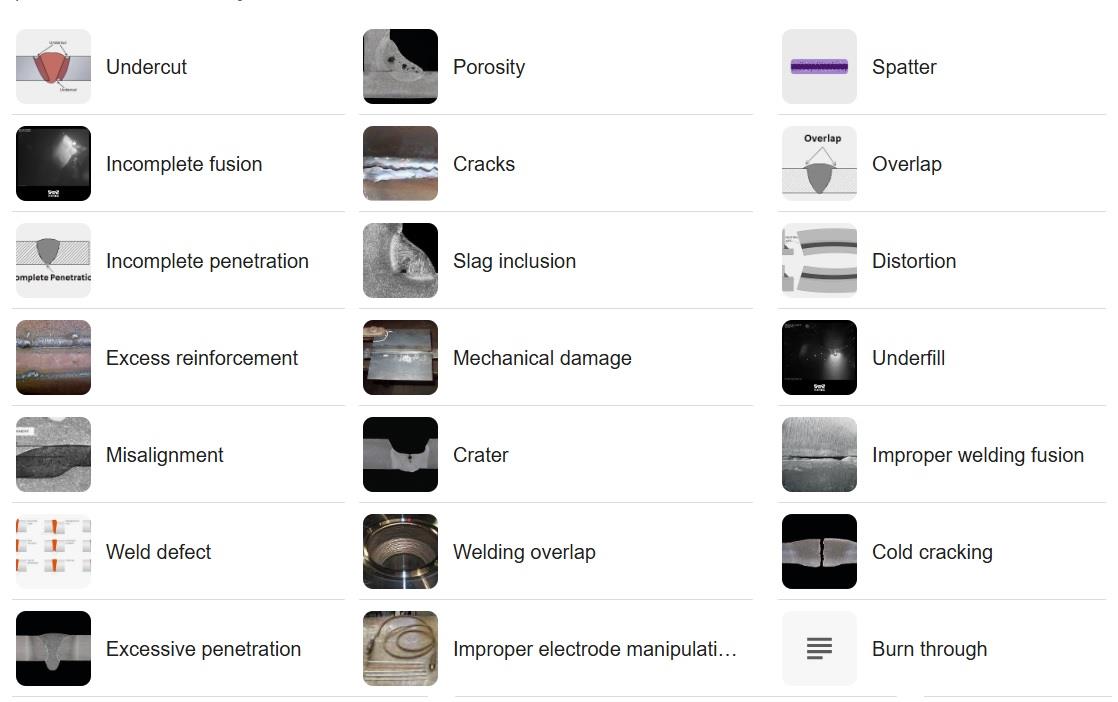
1. Cracks
Cracks are among the most serious welding defects. They indicate a complete separation in the weld or base metal and are often caused by stress, contamination, or poor material choice.
-
Hot Cracks: Form at high temperatures (above 1,000°C) during solidification due to contamination or poor base material selection.
-
Cold Cracks: Develop after cooling, often driven by hydrogen diffusion and high residual stress.
-
Crater Cracks: Occur at the end of a weld bead due to insufficient filler material in the weld pool.
Prevention: Use proper materials, clean surfaces, preheat as necessary, and fill craters properly before stopping the weld.
2. Porosity
Porosity refers to small cavities or holes in the weld caused by trapped gas bubbles. These weaken the weld and often result from contamination or moisture.
Causes: Rust, oil, wet electrodes, improper shielding gas.
Prevention: Clean all surfaces, use dry consumables, and maintain proper shielding gas flow.
3. Undercut
An undercut is a groove melted into the base metal adjacent to the weld toe, not filled with weld metal, reducing joint strength.
Causes: Excessive current, fast travel speed, or poor technique.
Prevention: Adjust current, reduce travel speed, and maintain proper electrode angle.
4. Welding Spatter
Spatter consists of droplets of molten metal expelled during welding that stick to nearby surfaces. Though often cosmetic, excessive spatter can interfere with coatings or assembly.
Causes: Excess current, long arc, or poor shielding gas coverage.
Prevention: Optimize voltage and current, maintain a short arc length, and use anti-spatter spray if needed.
5. Overlap
Overlap occurs when molten metal flows beyond the weld toe and fails to fuse with the base material. It creates weak joints and a poor appearance.
Causes: Improper travel speed or angle, excess filler.
Prevention: Improve torch control and adjust heat input.
6. Incomplete Fusion
Incomplete fusion happens when the weld metal fails to fuse properly with the base metal or previous weld beads.
Causes: Insufficient heat, poor joint preparation, or incorrect technique.
Prevention: Use appropriate heat input and clean joints thoroughly.
7. Incomplete Penetration
Occurs when the weld metal does not fully penetrate the joint thickness, resulting in a weak bond.
Causes: Low current, improper joint design, or poor access.
Prevention: Increase heat input, adjust joint geometry, and ensure proper access during welding.
8. Slag Inclusion
Slag from flux-coated electrodes can become trapped in the weld, reducing its mechanical strength.
Causes: Poor slag removal between passes, improper angle or travel speed.
Prevention: Clean each pass before welding over it and maintain proper technique.
9. Distortion
Distortion refers to warping or bending of the welded parts due to uneven heating and cooling.
Causes: High heat input, thin materials, lack of clamping.
Prevention: Use balanced welding, proper fixturing, and control heat input.
10. Excess Reinforcement
Excessive buildup of weld metal above the weld face, which adds unnecessary stress points.
Causes: Overfilling the joint or incorrect welding technique.
Prevention: Control filler addition and maintain a steady hand.
11. Mechanical Damage
Refers to surface gouges, dents, or scratches caused during or after welding, which may become crack initiation points.
Prevention: Handle welded parts carefully and inspect before service.
12. Underfill
Occurs when the weld metal surface is below the base metal level, weakening the weld.
Causes: Inadequate filler or incorrect technique.
Prevention: Ensure sufficient filler metal and proper arc control.
13. Misalignment
When joined components are not properly aligned before or during welding, resulting in structural issues.
Causes: Poor fit-up or improper clamping.
Prevention: Use proper fixtures and joint preparation.
14. Improper Welding Fusion
A general term for lack of proper bonding between weld layers or with the base material, similar to LOF.
Causes: Incorrect technique, low heat input, or contaminated surfaces.
Prevention: Train welders thoroughly and ensure clean, properly prepared joints.
15. Cold Cracking
Also known as hydrogen-induced cracking, this occurs after cooling, especially in high-strength steels.
Causes: Hydrogen in the weld area, high residual stress, and brittle microstructure.
Prevention: Preheat, use low-hydrogen consumables, and allow slow cooling.
16. Excessive Penetration
Too much penetration can lead to melt-through or weld metal protruding through the back of the joint.
Causes: Excessive heat or current.
Prevention: Use correct amperage and proper joint design.
17. Improper Electrode Manipulation
Poor movement of the electrode during welding can cause defects like lack of fusion, porosity, and irregular bead appearance.
Prevention: Train operators in consistent and controlled electrode manipulation techniques.
18. Burn Through
Occurs when the weld completely melts through thin material, creating holes.
Causes: Too much heat or slow travel on thin material.
Prevention: Lower amperage, increase travel speed, and use backer plates if needed.
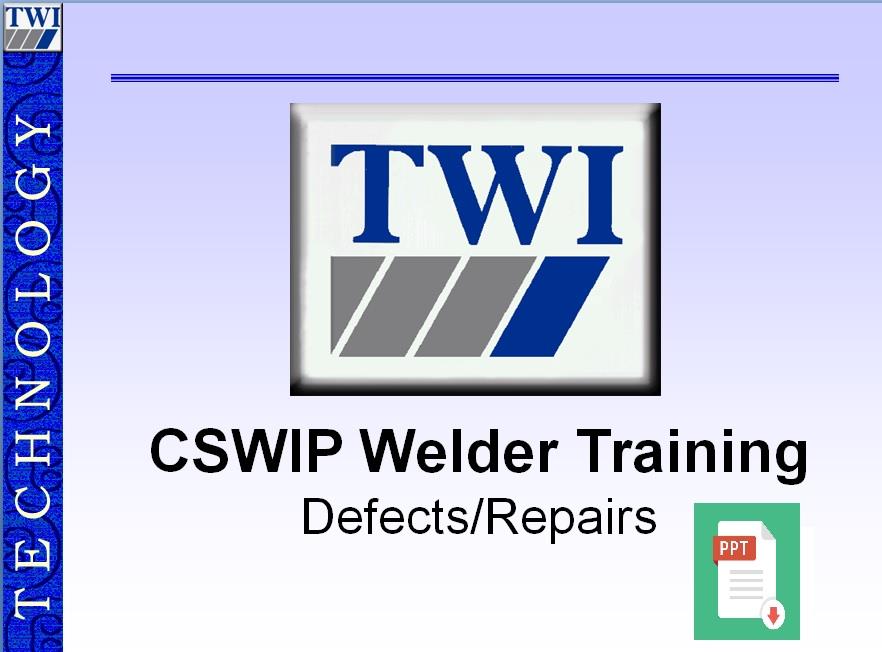
CSWIP Welder Training Welding Defects and Repairs
Welding defects can significantly impact the performance and reliability of structures. Identifying their causes and implementing preventive measures, such as proper technique, correct parameters, material cleanliness, and post-weld inspection, are key to producing high-quality, defect-free welds.
This training covers common welding defects such as porosity, cracks, and lack of fusion, their causes, and visual identification. It also explains standard repair techniques and preventive measures to ensure weld quality and structural integrity. Practical examples and inspection methods are included to enhance welder skill and awareness.
By understanding each defect and its origin, welders and engineers can ensure structural safety, cost-effectiveness, and long-term performance in welded components.