Hoisting and Rigging Safety: A Comprehensive Guide
Hoisting and rigging operations are critical in various industries, from construction to manufacturing, as they involve the safe lifting and transportation of heavy loads. These activities can present numerous hazards if not managed properly. This comprehensive guide provides an overview of hoisting and rigging safety, including common hazards, procedures, equipment, and safety practices.
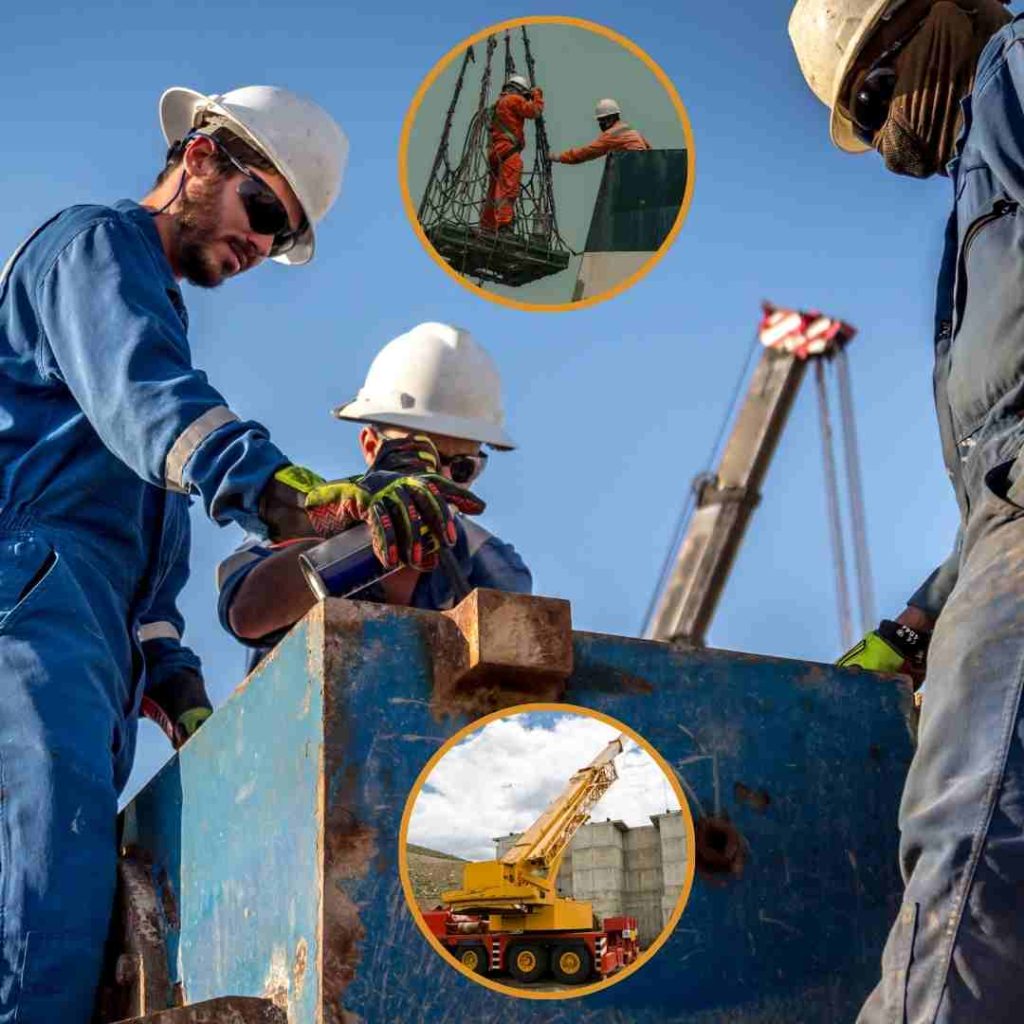
Hoisting and Rigging Hazards
Hoisting and rigging hazards are inherent in lifting and moving heavy loads. If safety is compromised, the results can be catastrophic. The following outlines common hazards in hoisting and rigging operations:
Common Hazards:
- Falling Loads: One of the most significant risks in hoisting operations is the falling of loads. This can result in severe injuries or fatalities. The load must be properly secured before lifting, and the area beneath the load should always be clear of personnel.
- Equipment Failure: Rigging equipment such as slings, hooks, shackles, and hoists can degrade over time due to wear and tear, leading to equipment failure during use. Regular inspection and maintenance are essential to ensure the reliability of this equipment.
- Improper Use of Rigging Gear: The selection and use of incorrect rigging equipment can lead to accidents. Using a sling that is too small for the load, or incorrectly tying knots, can compromise the safety of the lift.
- Pinch Points and Crush Hazards: Rigging operations often involve moving parts, such as winches and pulleys. Without adequate safety awareness, workers can get caught in pinch points, resulting in crush injuries.
- Electrocution from Power Lines: Working near power lines is a common hazard. If rigging equipment comes into contact with high-voltage power lines, workers can be electrocuted. It is essential to maintain a safe distance from power lines and ensure that all rigging operations are carried out within safety guidelines.
Identifying and Preventing Hazards:
- Routine Inspections: Rigging equipment should be inspected regularly for signs of damage or wear. Damaged equipment should be replaced immediately.
- Training and Certification: All workers involved in hoisting and rigging operations should be trained and certified. This ensures they understand the potential hazards and are equipped with the skills to prevent accidents.
- Safe Operating Procedures: Establishing clear, documented operating procedures for rigging and hoisting is critical. These procedures should address all potential hazards and outline step-by-step safety protocols for every phase of the lift.
Procedures and Precautions
Pre-Lift Procedures:
- Risk Assessment: Before any lift, it is vital to conduct a thorough risk assessment to identify potential hazards. This includes evaluating the load, the rigging equipment, the lifting method, and the work environment.
- Choosing the Right Equipment: The correct rigging gear must be selected based on the weight, shape, and type of load being lifted. It’s essential to ensure the equipment is rated for the specific load and is in good condition.
- Clear Communication: Clear and concise communication between the rigging crew and the crane operator is vital for safe hoisting operations. Use radios or other communication tools to maintain contact throughout the operation.
During the Lift:
- Monitor the Load: During the lift, always keep an eye on the load to ensure it remains stable and is not shifting. Any sign of instability should prompt an immediate halt to the operation.
- Proper Load Angle: The angle of the load should be checked continuously to ensure that it remains within safe limits. Lifting at an angle too steep can increase the risk of equipment failure.
- Avoid Sudden Movements: When lifting loads, avoid sudden or jerky movements that could cause the load to swing or shift unpredictably.
Post-Lift Procedures:
- Safe Unloading: Once the load has been lifted, it should be unloaded and stored safely. Rigging equipment should be inspected again after use, and any damage should be reported and repaired.
- Debriefing: After the operation, it’s crucial to debrief the team, discussing what went well and what could be improved for future operations. This helps build a culture of continuous safety improvement.
Weights of Common Materials
Knowing the weight of materials commonly hoisted is essential for selecting appropriate rigging equipment. Below are the typical weights for several common construction materials:
- Steel Beams: A standard I-beam can weigh anywhere from 40 to 80 pounds per foot, depending on the size and grade of steel.
- Concrete Blocks: Concrete blocks vary in weight based on size, but a typical 8x8x16 concrete block weighs about 35 pounds.
- Machinery: The weight of heavy machinery such as forklifts or industrial machines can range from several hundred pounds to several tons.
Understanding the weight of materials allows riggers to determine the correct equipment to use, such as slings, hooks, or hoists, to safely move these materials.
The Health and Safety Handbook
A Health and Safety Handbook serves as a crucial guide for workers and supervisors, outlining best practices, procedures, and emergency protocols to ensure safety in the workplace. Key areas covered typically include:
- General Safety Guidelines: Information on personal protective equipment (PPE), safe lifting techniques, and hazard identification.
- Emergency Procedures: Instructions on how to respond to various types of accidents, including falls, equipment failures, and fire hazards.
- Risk Management: How to identify potential risks before they become hazardous and how to mitigate those risks effectively.
Health and Safety Law
Health and safety laws are in place to ensure that workers are protected from hazards in the workplace. In many countries, these laws are enforced by regulatory agencies, such as OSHA (Occupational Safety and Health Administration) in the United States or HSE (Health and Safety Executive) in the UK.
Key regulations often include:
- General Duty Clause: Employers are required to provide a workplace free from recognized hazards that could cause serious injury or death.
- Rigging and Hoisting Regulations: Specific regulations apply to hoisting operations, including the safe use of cranes, slings, hoists, and other rigging equipment. Compliance with these regulations helps ensure the safety of all involved.
- Employee Rights and Responsibilities: Employees have the right to work in a safe environment and are responsible for adhering to safety procedures, reporting unsafe conditions, and using equipment properly.
Fibre Ropes, Knots, and Hitches
Fibre Ropes:
Fibre ropes are commonly used in rigging operations. They come in various types, each with different characteristics:
- Synthetic Fibre Ropes: These are made from man-made fibers such as nylon, polyester, or polypropylene. They are strong, lightweight, and resistant to rot but can stretch under load.
- Natural Fibre Ropes: Made from materials like hemp or cotton, natural fibre ropes are less durable than synthetic ones but may still be used in certain applications.
Knots and Hitches:
- Bowline Knot: One of the most versatile and commonly used knots in rigging. It forms a secure loop that won’t slip under load.
- Clove Hitch: This knot is used to attach a rope to a fixed object like a pole or post, ensuring the load stays secured.
Properly tied knots and hitches are essential for ensuring that loads are secured safely during lifting.
Hardware, Wire Rope, and Slings
Hardware:
Rigging hardware includes shackles, hooks, pulleys, and turnbuckles, all of which must be strong enough to handle the load they’re intended to bear. Regular inspection ensures these components remain in good working order.
Wire Rope:
Wire rope is often used in hoisting operations because it offers strength and flexibility. It comes in various grades, with steel wire rope being the most common. Choosing the correct grade is crucial for ensuring the rope can handle the load.
Slings:
Slings are used to secure the load to the crane or hoist. They can be made from various materials, including wire rope, synthetic fibers, and chain. Proper sling selection, along with periodic inspection, is essential for preventing accidents.
Rigging Tools and Devices
Rigging tools and devices include winches, hoists, and spreaders. These devices are used to control and move heavy loads safely:
- Winches: These are mechanical devices used to pull or lift loads. They come in manual and electric versions.
- Hoists: Hoists are used to lift or lower loads. They can be electric or manual and are often used in conjunction with cranes.
- Spreaders: Spreaders are used to distribute the load evenly, preventing the load from shifting or becoming unstable.
Changing the Workplace Safety Culture
A culture of safety is essential for preventing accidents in hoisting and rigging operations. Steps to foster such a culture include:
- Training and Education: Continuous training programs ensure that workers remain up to date on safety protocols.
- Employee Involvement: Encourage workers to actively participate in safety programs and reporting unsafe conditions.
- Management Commitment: Safety initiatives should be supported and promoted by management to ensure they are taken seriously across the organization.
Blocking and Cribbing
Blocking and cribbing are methods used to stabilize loads during lifting or transporting. Cribbing involves stacking materials like wood or plastic blocks to support the load, while blocking involves using larger pieces of material to stabilize it.
Inclined Planes
Inclined planes are used in rigging to move heavy objects up or down a slope. They provide a mechanical advantage by reducing the amount of force required to move the load. Safety measures should be followed to prevent slippage or instability when using inclined planes.
Electric Hoists and Pendant Cranes
Electric hoists and pendant cranes are widely used in lifting operations. These devices offer precision control and can lift heavy loads with minimal physical effort. Regular maintenance and inspection of these machines are necessary to ensure their continued safety.
Anchorage Points
Anchorage points are critical for the stability of rigging operations. They should be inspected regularly to ensure they can handle the forces exerted during hoisting. Secure anchorage points are necessary to prevent equipment failure or accidents.
Essentials of Health and Safety at Work (HSE)
The HSE provides essential guidelines and regulations for ensuring worker safety. Adhering to HSE standards helps prevent workplace accidents, ensuring a safer working environment for all employees.
Introduction to Crane Operations
Crane operations are often a part of rigging activities. A crane’s role in hoisting operations involves lifting and moving heavy loads. Operators must be trained and certified, and regular maintenance of crane equipment is necessary to ensure the crane functions safely.
Conclusion
Hoisting and rigging safety is essential to protect workers and prevent accidents in any lifting operation. By understanding the hazards, following proper procedures, and using the right equipment, risks can be significantly reduced. Through ongoing training, awareness, and a culture of safety, hoisting and rigging can be performed safely and efficiently in any workplace.