Introduction to Risk and Failures
Risk and failure are inherent aspects of any system, process, or activity. Understanding and managing these elements is critical to ensuring the safety, reliability, and efficiency of operations across industries. This article explores the fundamental concepts of risk and failure, their causes and consequences, and effective strategies to minimize their impact.
Understanding Risk
Risk is the probability of an event occurring that could result in harm, loss, or negative consequences. It arises from uncertainty in processes, systems, or external conditions. In the industrial context, risks are associated with safety hazards, financial losses, operational disruptions, and environmental impacts.
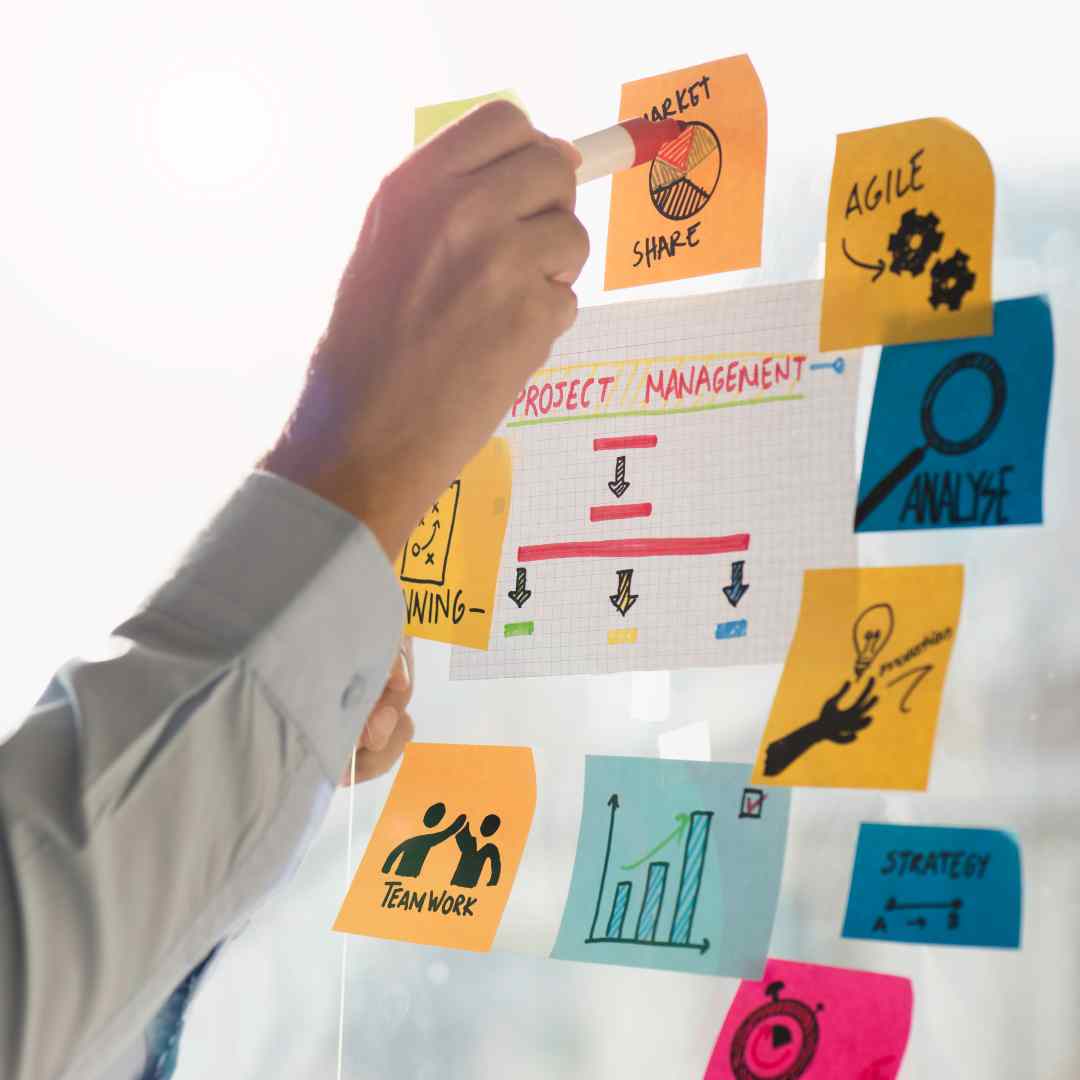
Effective risk management involves:
- Identifying potential risks.
- Assessing their likelihood and potential impact.
- Implementing measures to mitigate, transfer, or accept the risks based on strategic priorities.
Defining Failures
Failure occurs when a system, component, or process does not perform as intended. Failures can result from design flaws, human errors, material degradation, or unexpected external conditions. The consequences of failures range from minor inconveniences to catastrophic events, such as equipment breakdowns, financial losses, or safety hazards.
Failures are generally categorized as:
- Functional Failures: Inability to meet required performance standards.
- Catastrophic Failures: Sudden and complete breakdowns causing severe damage.
- Degradation Failures: Gradual deterioration over time leading to reduced performance.
The Relationship Between Risk and Failure
Risk and failure are interconnected, with failure often being the result of unmitigated risks. Understanding this relationship is essential for predicting and preventing failures through risk analysis. By identifying and mitigating risks, organizations can reduce the likelihood and impact of failures, ensuring smoother operations and enhanced safety.
Causes of Failures
- Human Errors
Mistakes in operation, maintenance, or design can lead to failures. Lack of training, miscommunication, or over-reliance on manual processes often exacerbates these errors. - Design and Engineering Defects
Poorly designed systems or components can fail under expected operating conditions. This includes issues like insufficient load capacity, material weaknesses, or inadequate testing. - Material and Component Degradation
Over time, materials may wear out, corrode, or fatigue, leading to failure. Regular inspections and timely replacements are crucial to avoid such outcomes. - Environmental Factors
External conditions, such as extreme temperatures, humidity, or exposure to chemicals, can accelerate the failure of systems or components. - Unforeseen Circumstances
Natural disasters, power outages, or unexpected operational demands can disrupt systems and lead to failures.
Risk and Failure Analysis Techniques
- FMEA (Failure Mode and Effects Analysis)
This method systematically identifies potential failure modes, their causes, and consequences to prioritize risk mitigation actions. - Fault Tree Analysis (FTA)
FTA involves creating a diagrammatic representation of the events leading to a failure, helping identify root causes and preventive measures. - Hazard and Operability Study (HAZOP)
This qualitative technique identifies potential hazards and operational issues in complex systems. - Reliability-Centered Maintenance (RCM)
RCM focuses on identifying critical assets and implementing maintenance strategies to prevent failures and optimize system reliability. - Root Cause Analysis (RCA)
RCA investigates the underlying reasons for failures to prevent their recurrence.
Risk Mitigation and Failure Prevention Strategies
- Proactive Maintenance Programs
Implementing preventive and predictive maintenance reduces the likelihood of equipment failure. Regular inspections and condition monitoring ensure that issues are addressed before they escalate. - Robust Design and Testing
Ensuring systems and components are designed to withstand expected conditions and rigorously tested minimizes design-related failures. - Training and Competency Development
Equipping employees with the necessary skills and knowledge reduces the likelihood of human error. Ongoing training ensures teams stay updated on best practices and safety standards. - Implementing Safety and Risk Management Systems
Comprehensive safety programs, risk assessment frameworks, and incident reporting mechanisms enhance an organization’s ability to identify and address risks effectively. - Contingency Planning
Developing and practicing emergency response plans ensures readiness to address unexpected failures or crises.
Learning from Failures
Failures, when analyzed effectively, provide valuable lessons for future risk management. Organizations that embrace a culture of continuous improvement and open reporting are better equipped to identify weaknesses, enhance processes, and prevent recurring failures.
Conclusion
Understanding the dynamics of risk and failure is crucial for maintaining operational efficiency, safety, and reliability. Through robust risk assessment, proactive maintenance, and a commitment to learning from failures, organizations can minimize the impact of uncertainties and achieve long-term success. By integrating these principles into their operations, businesses can safeguard their assets, protect their employees, and enhance overall performance.