Maintenance Management for Water Utilities
Efficient maintenance management is essential for water utilities to ensure the uninterrupted delivery of clean and safe water to communities. The complexity of water distribution and treatment systems demands a comprehensive and proactive maintenance strategy. This article delves into the critical components of maintenance management, emphasizing organizational structure, predictive maintenance, personnel roles, inventory control, and modern technological approaches.
The Need for Maintenance
Maintenance in water utilities is crucial to ensuring the reliability and efficiency of infrastructure, including pipes, pumps, treatment plants, and storage facilities. Poorly maintained systems can lead to leaks, contamination, equipment failure, and regulatory non-compliance. Proactive maintenance not only extends the lifespan of equipment but also minimizes costly emergency repairs.
Example: A water utility detects a small leak in its distribution system through routine inspections. Addressing it promptly saves the utility from a major pipe burst and water loss.
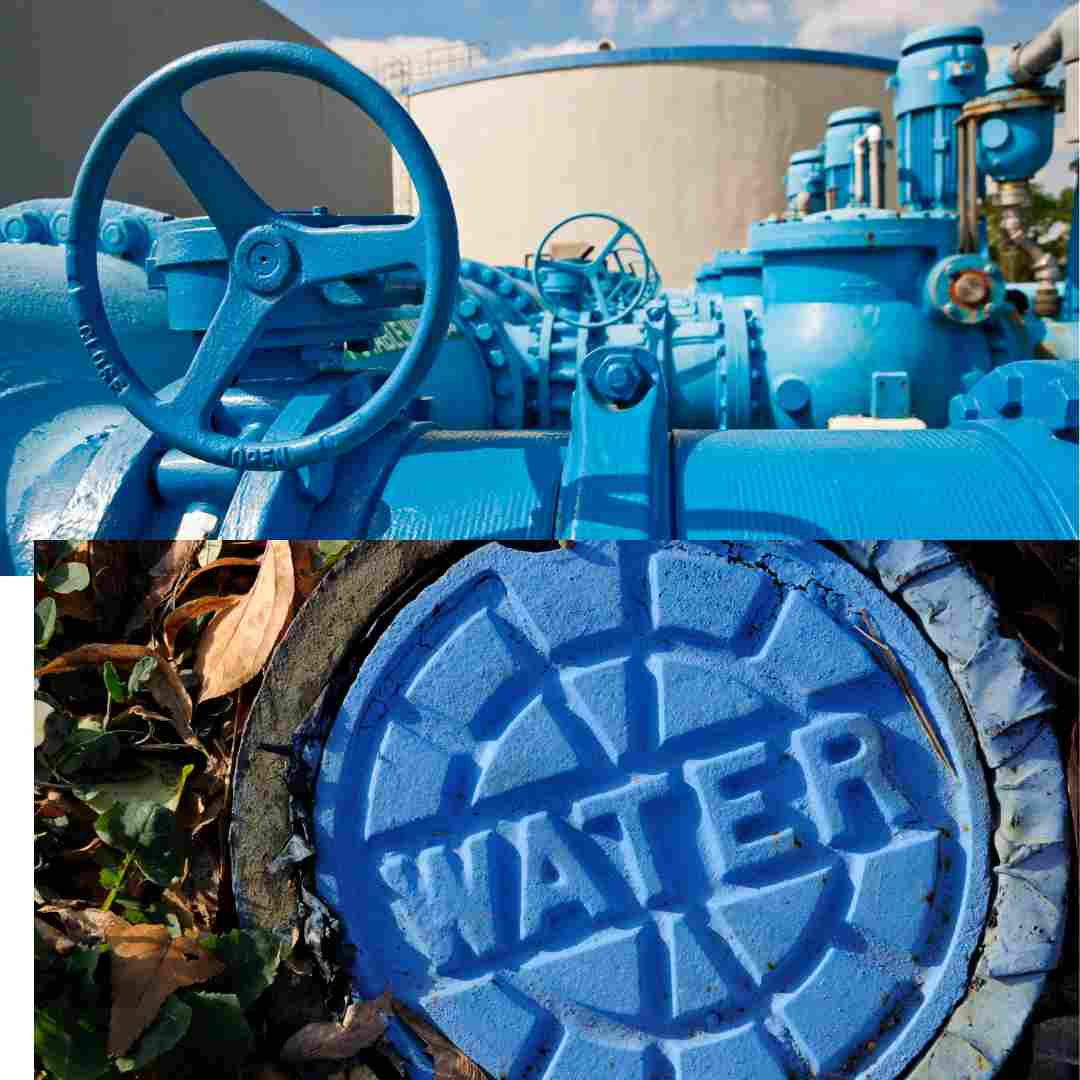
Maintenance Department Management
Effective maintenance begins with a well-structured department. This involves clearly defining roles, responsibilities, and workflows to streamline operations. Key elements include:
Leadership: A maintenance manager oversees operations, sets priorities, and ensures regulatory compliance.
Coordination: Close collaboration with other departments, such as operations and engineering, to align maintenance efforts with overall utility goals.
Organization of the Utility
The organizational structure of the utility plays a critical role in maintenance efficiency. Utilities often adopt centralized or decentralized approaches:
Centralized Maintenance: A dedicated team handles maintenance across the utility.
Decentralized Maintenance: Maintenance responsibilities are distributed among various facilities or regions.
Example: A large metropolitan utility with multiple treatment plants benefits from a centralized approach to standardize procedures, while smaller utilities might rely on decentralized management to address localized needs.
An Introduction to Predictive Maintenance
Predictive maintenance uses advanced technologies to anticipate equipment failures before they occur. This approach reduces unplanned downtime and optimizes resource allocation. Common predictive maintenance techniques include:
Vibration Analysis: Identifying issues in pumps and motors.
Thermography: Detecting temperature anomalies in electrical systems.
Ultrasonic Testing: Locating leaks in pipelines.
Example: By monitoring pump vibration data, a utility predicts and replaces a failing bearing, avoiding a system-wide shutdown.
Maintenance Personnel
The success of any maintenance program hinges on skilled personnel. Maintenance teams must include:
Technicians: Trained in specific equipment and systems.
Supervisors: Ensuring tasks are completed efficiently and safely.
Specialists: Handling advanced diagnostic or predictive maintenance tools.
Maintenance by Operations Personnel
Operations staff play a crucial role in day-to-day maintenance activities, such as monitoring equipment performance, conducting visual inspections, and performing basic troubleshooting.
Example: Operators at a treatment plant notice unusual noise in a pump and report it to the maintenance team, leading to early intervention.
Maintenance by Outside Contractors
For specialized tasks or when in-house capacity is insufficient, utilities may rely on outside contractors. Outsourcing can be cost-effective for complex repairs, such as large-scale pipeline rehabilitation or advanced electrical diagnostics.
Planning a Maintenance Management System
A well-designed maintenance management system (MMS) integrates planning, scheduling, execution, and monitoring. Steps to develop an MMS include:
- Assessing Assets: Inventory all equipment and infrastructure.
- Defining Goals: Establish maintenance priorities based on criticality.
- Developing Schedules: Create preventive and predictive maintenance plans.
Information Management and System Monitoring
Modern maintenance relies heavily on data. Utilities must implement robust information management systems to monitor performance and track maintenance activities. Key tools include:
Supervisory Control and Data Acquisition (SCADA): Provides real-time system data.
Computerized Maintenance Management Systems (CMMS): Tracks work orders, schedules, and asset histories.
Work Order Systems
Work order systems ensure that maintenance tasks are tracked and executed efficiently. Components of an effective work order system include:
Prioritization: Categorize tasks by urgency.
Documentation: Record all actions for future reference.
Accountability: Assign tasks to specific personnel or teams.
Maintenance System Monitoring Techniques
System monitoring identifies potential issues before they escalate. Techniques include:
Pressure Monitoring: Detects leaks or blockages in pipelines.
Flow Rate Analysis: Identifies inefficiencies in distribution.
Condition Monitoring: Tracks wear and performance of mechanical components.
Inventory Management
Effective inventory management is vital for water utilities to maintain operational continuity and minimize downtime. Spare parts, tools, and critical materials must be readily accessible to address routine maintenance and emergency repairs. Overstocking ties up capital and storage space, while shortages can delay repairs and jeopardize system reliability. A balanced inventory strategy requires categorizing parts by priority, ensuring high-demand items are consistently available while managing low-turnover items judiciously.
Example Use Case: A water utility maintains an optimal stock of pump seals and motor bearings, as these components frequently wear out during high-demand periods. This minimizes operational delays caused by supply chain disruptions.
Inventory Accountability
Accountability ensures that every item in the inventory is tracked from procurement to usage. Utilities must establish robust tracking systems that record material movement, usage patterns, and restocking timelines. This prevents unauthorized use, reduces waste, and ensures critical components are available when needed. Regular audits and reconciliation reports help utilities maintain accurate records and avoid discrepancies.
Example Use Case: An automated inventory system flags discrepancies between recorded and actual stock of pipeline valves during a quarterly audit, prompting an investigation that uncovers inefficiencies in manual logging procedures.
Determining Quantities in Inventory
Calculating the optimal inventory levels involves analyzing historical usage data, equipment maintenance schedules, and lead times for procurement. Utilities must also account for seasonal demand fluctuations and emergency requirements. Forecasting methods can be used to predict future needs, ensuring that the inventory aligns with operational demands without overstocking.
Example Use Case: During summer months, a utility increases stock of water meters and pipe fittings due to higher installation and repair demands, based on historical data from previous years.
Automated Inventory Systems
Automated inventory systems leverage technology to enhance efficiency and accuracy in inventory management. These systems use real-time tracking to monitor stock levels, generate alerts for replenishment, and streamline ordering processes. Integration with maintenance management systems enables better coordination between inventory and maintenance tasks, reducing delays caused by unavailable parts.
Example Use Case: A CMMS (Computerized Maintenance Management System) integrated with an automated inventory module alerts the procurement team when the stock of chlorine injectors falls below the reorder threshold, ensuring timely restocking and uninterrupted water treatment operations.
Maintenance Group Requirements
The maintenance group requires adequate resources, including skilled staff, diagnostic tools, and sufficient budget allocations. Training programs ensure that personnel are up-to-date with the latest maintenance techniques and regulatory requirements.
Engineering Maintenance: A Modern Approach
Engineering maintenance incorporates advanced methodologies such as reliability-centered maintenance (RCM) and total productive maintenance (TPM) to enhance system reliability.
Conclusion
Effective maintenance management is the backbone of water utilities, ensuring reliable service delivery, regulatory compliance, and cost efficiency. By adopting modern practices like predictive maintenance, leveraging data-driven tools, and optimizing inventory management, utilities can achieve sustainable operations and long-term reliability.