Occupational Safety and Health Simplified for the Industrial Workplace
Occupational safety and health (OSH) are crucial aspects of ensuring the well-being of workers in any industrial workplace. By prioritizing safety measures, employers can prevent accidents, reduce health risks, and create a productive and safe environment for employees. This guide simplifies the concepts of occupational safety and health, focusing on key principles, risk management, and best practices for industrial settings.
Table of Contents
ToggleUnderstanding Occupational Safety and Health (OSH)
Occupational safety and health involve protecting workers from hazards that can cause harm during the course of their work. This includes physical hazards, such as machinery and tools, as well as chemical, biological, and ergonomic risks. OSH also encompasses legal and regulatory compliance to ensure that workplaces are safe and employees’ health is protected.
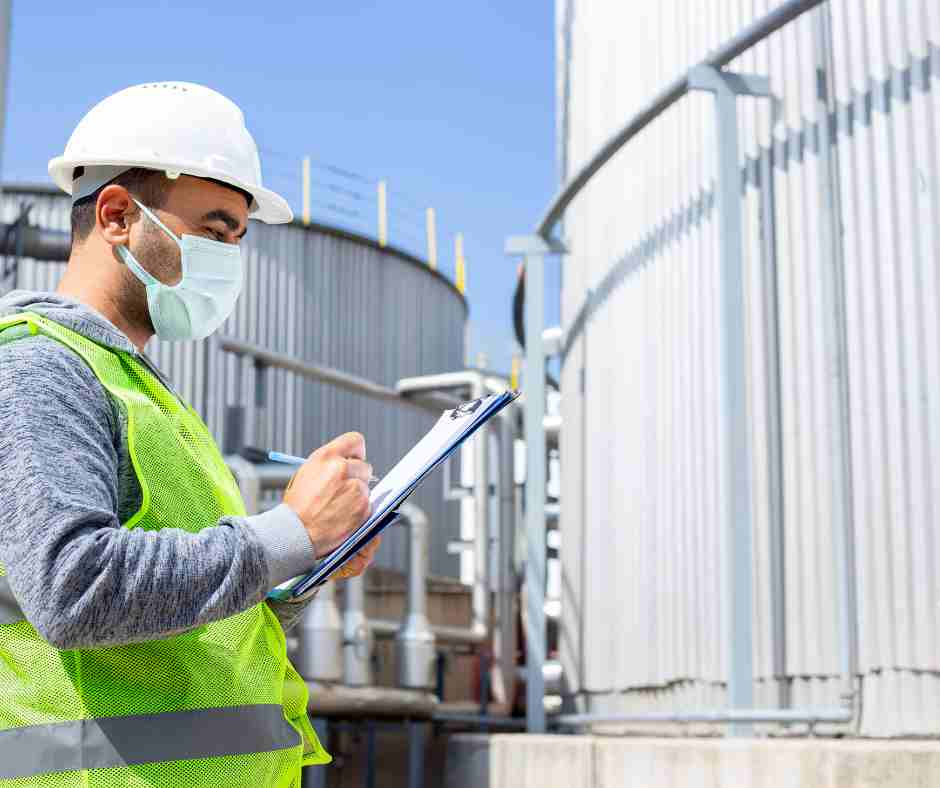
The primary goals of OSH include:
- Preventing workplace accidents and injuries
- Reducing occupational illnesses
- Ensuring compliance with health and safety laws
- Promoting a culture of safety in the workplace
Key Components of Occupational Safety and Health
Risk Assessment
Risk assessment is the foundation of any OSH program. It involves identifying potential hazards in the workplace, assessing their likelihood and severity, and implementing measures to reduce or eliminate risks. A thorough risk assessment helps prioritize safety actions and ensures that the workplace is adequately prepared to handle various hazards.
Key steps in risk assessment:
- Identifying hazards (physical, chemical, biological, ergonomic)
- Evaluating the risk level of each hazard
- Determining control measures to mitigate risks
- Continuously reviewing and updating risk assessments
Safety Regulations and Standards
In industrial workplaces, following safety regulations and standards is essential for maintaining compliance and protecting workers. These regulations are typically set by government agencies, such as OSHA in the U.S. or the HSE in the U.K. Compliance ensures that the workplace meets safety standards related to equipment, training, personal protective equipment (PPE), and emergency protocols.
Common standards include:
- OSHA guidelines for workplace safety
- National Fire Protection Association (NFPA) codes
- ISO standards for health and safety management
Personal Protective Equipment (PPE)
PPE is essential in protecting workers from various hazards, such as chemicals, machinery, and falling objects. Proper use of PPE can significantly reduce the risk of injury or illness in the workplace. Employers must ensure that workers are properly trained in the selection, use, and maintenance of PPE.
Types of PPE commonly used in industrial settings:
- Hard hats and helmets
- Safety glasses and face shields
- Hearing protection (earplugs, earmuffs)
- Respirators and protective clothing
- Steel-toed boots and gloves
Workplace Safety Training
Training is a critical element in promoting a safe workplace. Workers must be trained on identifying hazards, using safety equipment, and responding to emergencies. Ongoing safety education helps employees stay informed about the latest safety protocols and encourages a culture of safety throughout the organization.
Key training areas include:
- Hazard recognition and reporting
- Safe use of machinery and equipment
- Emergency response and evacuation procedures
- First aid and CPR training
- Ergonomics and safe lifting techniques
Emergency Preparedness and Response
Emergency preparedness is essential for minimizing the impact of accidents or unexpected incidents in the workplace. A well-prepared workforce can respond quickly and efficiently to emergencies, such as fires, chemical spills, or medical emergencies.
Key components of emergency preparedness:
- Clear emergency procedures and evacuation plans
- Regular fire drills and safety simulations
- Accessible first aid kits and trained responders
- Clear communication channels during emergencies
Common Workplace Hazards and Their Control
Physical Hazards
Physical hazards in the industrial workplace can include machinery, noise, and working at heights. Proper guarding of machinery, regular equipment maintenance, and ensuring safety protocols for working at heights are critical in controlling physical risks.
Control measures for physical hazards:
- Machine guards and safety interlocks
- Regular maintenance and inspections
- Use of appropriate fall protection systems
- Noise reduction strategies and hearing protection
Chemical Hazards
Chemical hazards are common in many industrial workplaces, where workers may be exposed to toxic substances such as solvents, acids, and gases. Managing chemical hazards requires proper labeling, storage, and handling practices to prevent exposure.
Control measures for chemical hazards:
- Proper labeling and safety data sheets (SDS)
- Safe storage of chemicals in well-ventilated areas
- Use of appropriate PPE, such as gloves and respirators
- Regular monitoring of air quality for hazardous fumes
Biological Hazards
Biological hazards, such as bacteria, viruses, and fungi, can pose significant health risks, particularly in industries like healthcare, agriculture, and food production. Employers must implement safety measures to protect workers from biological exposures.
Control measures for biological hazards:
- Proper sanitation and hygiene practices
- Use of PPE like gloves, masks, and gowns
- Vaccination programs for at-risk workers
- Effective waste disposal systems to handle biological materials
Ergonomic Hazards
Ergonomic hazards occur when workers perform repetitive tasks or work in awkward postures, leading to musculoskeletal disorders (MSDs). Implementing ergonomic solutions can reduce the risk of these injuries and improve overall productivity.
Control measures for ergonomic hazards:
- Designing workstations to minimize awkward postures
- Providing adjustable chairs and desks
- Offering tools that reduce repetitive motion
- Implementing job rotation and breaks to avoid strain
Safety Culture in the Workplace
A strong safety culture is essential for fostering a work environment where health and safety are prioritized. Workers should feel empowered to report safety concerns, and safety should be a shared responsibility across all levels of the organization. Leadership plays a crucial role in shaping this culture by demonstrating a commitment to safety.
Steps to improve safety culture:
- Management leading by example and prioritizing safety
- Encouraging open communication about safety concerns
- Recognizing and rewarding safe behavior
- Involving workers in safety decision-making processes
Health and Wellness in the Workplace
In addition to physical safety, promoting the overall health and wellness of employees is important for creating a safe work environment. This includes addressing mental health, promoting healthy lifestyles, and providing access to wellness programs.
Health and wellness initiatives can include:
- Employee assistance programs (EAPs) for mental health support
- Access to fitness programs or wellness challenges
- Healthy food options in the workplace
- Ergonomic programs to prevent injury and discomfort
Conclusion
Occupational safety and health are essential components of a productive and sustainable industrial workplace. By understanding and addressing hazards, complying with safety regulations, and promoting a culture of safety, employers can protect their workers and ensure a safer work environment. Risk assessment, training, and preparedness are key to preventing accidents, improving health, and promoting well-being in the workplace. Through these efforts, both employers and workers can contribute to a safer, healthier, and more efficient workplace.