OSHA Compliance According to OSHA Regulations
The Occupational Safety and Health Administration (OSHA) is the cornerstone of workplace safety in the United States. Established under the Occupational Safety and Health Act of 1970, OSHA sets and enforces standards to prevent workplace injuries, illnesses, and fatalities. Employers who adhere to OSHA regulations not only protect their workers but also create a safer and more productive work environment. This article provides a detailed overview of OSHA compliance by grouping related topics for better understanding.
Introduction to OSHA and Compliance Essentials
OSHA’s mission is to ensure safe and healthy working conditions by setting and enforcing standards and by providing education, training, and assistance. Employers are legally obligated to comply with these standards, which are designed to mitigate workplace risks across all industries. OSHA compliance involves implementing preventive measures, maintaining proper documentation, and conducting regular training to address potential hazards.
OSHA inspections play a critical role in compliance enforcement. Inspectors assess the workplace by reviewing records, observing practices, and interviewing employees. Being prepared for an unannounced OSHA inspection ensures a safer work environment and minimizes the risk of penalties.
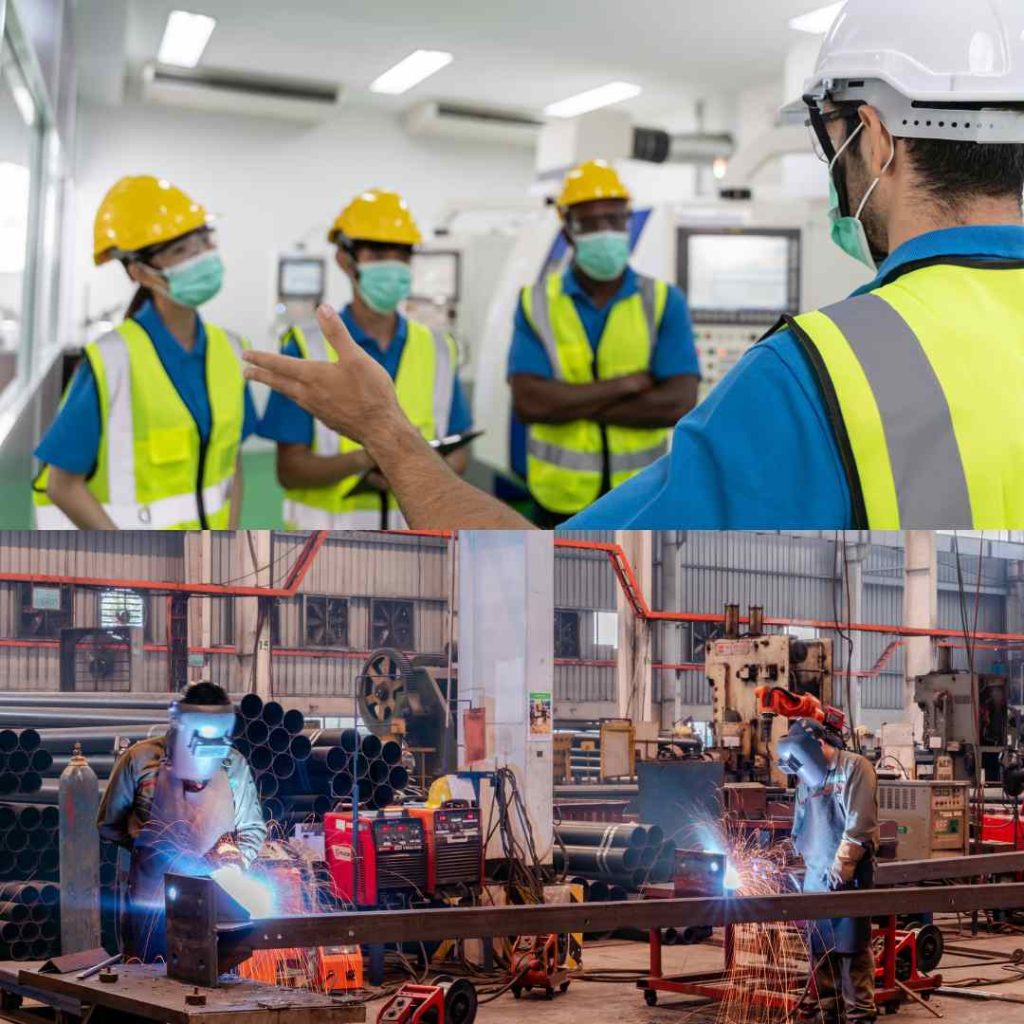
Recordkeeping and Reporting Requirements
Accurate recordkeeping is a cornerstone of OSHA compliance. Employers must document workplace injuries, illnesses, and exposures using OSHA Forms 300, 300A, and 301. These records not only aid in compliance but also help identify patterns that can lead to preventive measures.
Injury and illness logs provide a transparent overview of workplace incidents. Employers are required to display Form 300A annually to inform employees of workplace safety trends. OSHA also mandates preserving medical and exposure records for workers exposed to hazardous substances, ensuring these records are accessible for long-term monitoring.
Additionally, OSHA collaborates with the Bureau of Labor Statistics (BLS) to compile nationwide injury and illness data. These reports offer valuable insights for employers seeking to enhance workplace safety.
Workplace Hazards and Preventive Measures
OSHA compliance is centered on identifying and mitigating workplace hazards. These include physical risks, chemical exposures, and environmental factors. Regular job hazard analyses help employers recognize risks associated with specific tasks, enabling them to implement targeted preventive measures.
Key Hazard Areas:
- Air Contaminants and Asbestos: OSHA sets strict exposure limits for harmful substances like asbestos and airborne contaminants. Employers must monitor air quality and ensure proper ventilation and protective equipment are in place.
- Occupational Noise Exposure: Prolonged exposure to high noise levels requires employers to implement hearing conservation programs, including the use of ear protection and regular hearing tests.
- Combustible Dust: Industries dealing with combustible dust must follow OSHA guidelines to minimize fire and explosion risks through effective dust control measures and equipment maintenance.
- Temperature Extremes: OSHA provides recommendations for managing heat and cold stress, such as hydration protocols, rest breaks, and appropriate clothing.
Employers are also responsible for addressing hazards associated with confined spaces, ensuring proper atmospheric testing, permits, and rescue plans to protect workers in such environments.
Employee Training and Communication
Employee education and training are vital for OSHA compliance. Employers must provide training tailored to job-specific hazards, ensuring workers understand safety protocols, hazard communication, and emergency procedures.
The Hazard Communication Standard (HCS) requires employers to inform workers about the risks associated with hazardous chemicals. This includes proper labeling, providing Safety Data Sheets (SDS), and conducting training sessions to familiarize employees with these materials.
Regular training reinforces safe practices, such as the correct use of personal protective equipment (PPE), lockout/tagout procedures, and the operation of machinery. Employee awareness not only enhances safety but also ensures compliance with OSHA standards.
Machine Safety and Ergonomics
Machinery and equipment pose significant risks if not properly guarded or maintained. OSHA mandates the use of machine guards, safety switches, and emergency stop systems to prevent injuries. Employers must regularly inspect and maintain equipment to avoid mechanical failures and accidents.
Ergonomics, the study of workplace design, is another crucial area of OSHA compliance. Poor ergonomic practices can lead to musculoskeletal injuries, particularly in jobs involving repetitive tasks or improper workstation setups. Employers are encouraged to redesign workstations, provide ergonomic tools, and educate workers on proper posture and movement.
Health Hazards and Medical Monitoring
Health hazards, including bloodborne pathogens, demand strict compliance with OSHA standards. Workers exposed to infectious materials, such as in healthcare settings, must follow exposure control plans, use PPE, and undergo medical monitoring.
Screening and surveillance programs are essential for employees exposed to hazardous substances or high-risk environments. Periodic health checks and record maintenance ensure the early detection of health issues, helping employers implement corrective measures promptly.
Emergency Preparedness and Response
OSHA emphasizes the importance of having robust emergency response plans to address workplace crises, such as fires, chemical spills, and natural disasters. Employers must create and communicate detailed emergency action plans, conduct regular drills, and ensure the availability of necessary equipment, such as fire extinguishers and first aid kits.
Proper labeling, signs, and markings also play a crucial role in emergencies. OSHA requires workplaces to use standardized signs to indicate hazards, emergency exits, and safety equipment locations.
Construction and Industry-Specific Standards
The construction industry, due to its high-risk nature, requires strict adherence to OSHA standards. Key areas of focus include fall protection, scaffolding safety, excavation protocols, and electrical hazard management. Regular inspections and site-specific training programs help maintain compliance in construction environments.
In other industries, such as manufacturing, OSHA’s Lockout/Tagout (LOTO) standard ensures that machinery undergoing maintenance is de-energized to prevent accidental startup. Compliance with LOTO procedures significantly reduces risks associated with energy release.
Environmental Considerations and Safety Programs
OSHA regulations extend to environmental factors affecting workplace safety. Employers must manage air contaminants, asbestos exposure, and temperature extremes to create a safe environment.
Comprehensive safety and health programs form the foundation of OSHA compliance. These programs involve:
- Management Commitment: Leadership actively supports safety initiatives.
- Employee Participation: Workers are engaged in identifying and resolving hazards.
- Hazard Identification: Regular assessments identify risks and preventive actions.
- Continuous Improvement: Employers review and update safety protocols to address emerging challenges.
Conclusion
OSHA compliance is a multifaceted process encompassing recordkeeping, hazard management, employee training, and emergency preparedness. By adhering to OSHA regulations, employers not only safeguard their workforce but also contribute to a culture of safety and accountability. Proactive compliance ensures a healthier, more productive workplace, reducing risks and fostering employee trust. Prioritizing OSHA standards is not just a legal obligation but a commitment to worker welfare and organizational excellence.