Planning and Control of Maintenance Systems
Effective maintenance management is vital for ensuring the smooth and efficient operation of industrial systems, machinery, and equipment. The planning and control of maintenance systems involve organizing, scheduling, and monitoring maintenance tasks to maximize equipment reliability, minimize downtime, and reduce costs. An effective maintenance strategy ensures that assets are well-maintained, which increases productivity, extends the lifespan of equipment, and ensures compliance with safety and regulatory standards.
Key Aspects of Maintenance Planning
- Establishing Maintenance Objectives
The first step in planning a maintenance system is to define the objectives, which may include maximizing uptime, minimizing costs, ensuring safety, or complying with regulatory standards. Clear goals help determine the resources, personnel, and budget required to maintain systems effectively. - Asset Management and Prioritization
Identifying critical assets and determining their maintenance needs is crucial. Not all equipment requires the same level of attention, so prioritizing based on factors such as operational importance, failure risk, and cost implications is essential for efficient resource allocation. - Maintenance Scheduling
Maintenance scheduling is about planning when and how maintenance activities will be carried out. Scheduled maintenance can be either preventive (routine checks and fixes to avoid failures) or predictive (based on condition monitoring). Proper scheduling ensures that maintenance does not interfere with production and that resources are efficiently utilized. - Resource Allocation
This involves determining the necessary manpower, tools, spare parts, and equipment required for maintenance activities. Effective resource allocation ensures that maintenance teams can perform their tasks without delays or shortages.
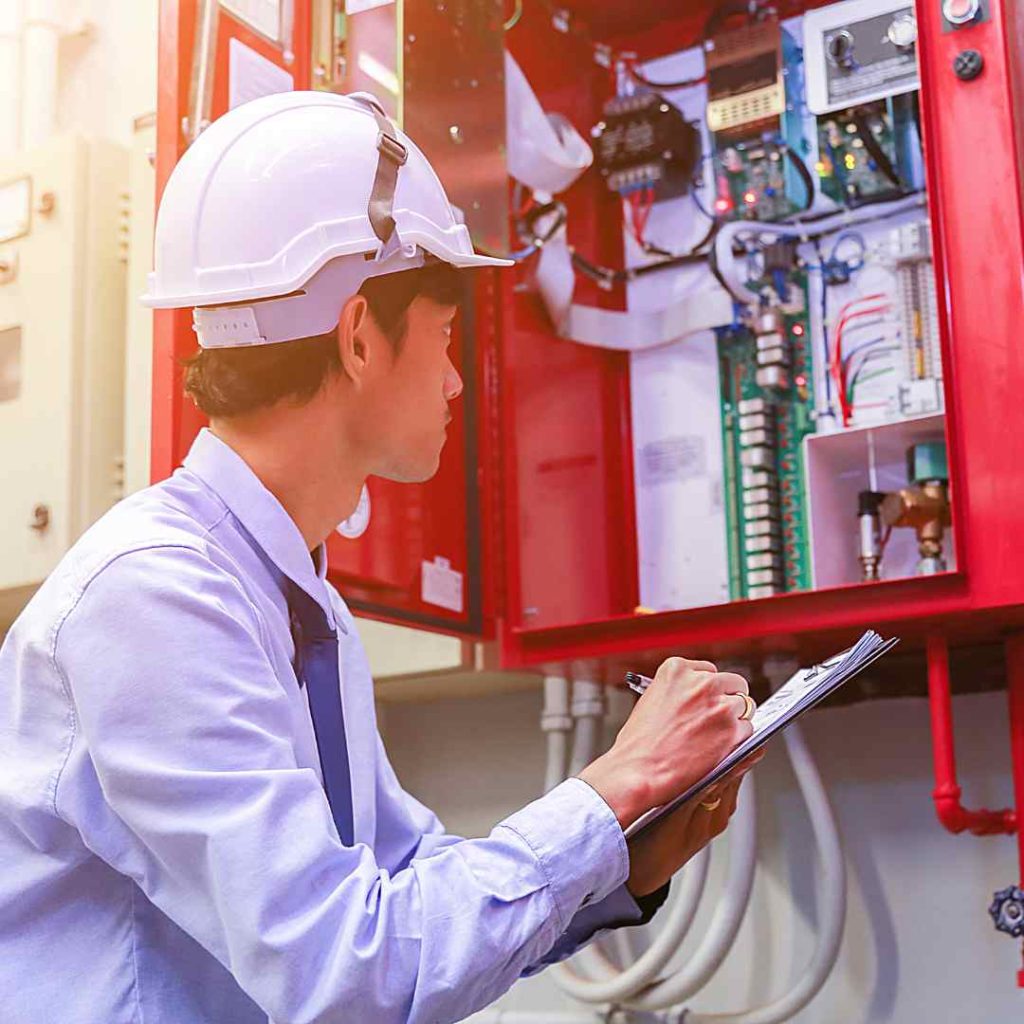
Control of Maintenance Systems
- Monitoring Performance
Monitoring the performance of maintenance activities is key to ensuring that the plan is working as expected. This involves tracking equipment reliability, failure rates, downtime, and overall performance metrics. Key performance indicators (KPIs) such as mean time between failures (MTBF) and mean time to repair (MTTR) help assess the effectiveness of the maintenance strategy. - Maintenance Budgets and Cost Control
Effective control of maintenance systems requires careful budget management. Keeping costs in check involves not only monitoring maintenance expenses but also optimizing processes and minimizing downtime. Proper cost control ensures that maintenance activities align with overall business objectives and financial constraints. - Work Order Management
A work order system is essential for controlling maintenance activities. Work orders allow for the tracking of requests, assigning tasks to technicians, and monitoring completion status. Proper work order management helps maintain a streamlined maintenance process, ensuring tasks are completed on time and within scope. - Data and Analytics
Leveraging data analytics helps improve the control of maintenance systems by identifying trends, predicting potential failures, and suggesting preventive actions. Data can be gathered from various sources, such as equipment sensors, maintenance logs, and performance reports, to drive continuous improvements in the maintenance process.
Types of Maintenance Systems
- Preventive Maintenance
This type of maintenance involves regularly scheduled inspections and interventions aimed at preventing equipment failure before it occurs. It helps reduce unplanned downtime and maintain the equipment in optimal working condition. - Predictive Maintenance
Predictive maintenance uses data from sensors, wearables, and monitoring systems to predict when equipment is likely to fail. This allows organizations to perform maintenance just before the failure occurs, reducing unnecessary maintenance activities and minimizing downtime. - Corrective Maintenance
Corrective maintenance is performed after equipment failure has occurred. It focuses on fixing the issue, returning the asset to service as quickly as possible, and identifying the root cause to prevent similar failures in the future. - Condition-Based Maintenance
This approach involves performing maintenance tasks based on the actual condition of equipment rather than on a fixed schedule. Monitoring the health of equipment through various sensors and data points helps determine when maintenance is required.
Challenges in Maintenance Planning and Control
- Unforeseen Downtime
Unexpected breakdowns and equipment failures can disrupt the maintenance schedule and affect production. Having contingency plans and quick response strategies in place is essential for minimizing downtime. - Lack of Skilled Labor
Maintenance activities require skilled workers who are trained in the use of specialized tools and troubleshooting techniques. A shortage of trained personnel can lead to delays, increased downtime, and suboptimal maintenance practices. - Aging Equipment
Older equipment often requires more frequent maintenance and may be more prone to breakdowns. Planning for the eventual replacement of aging assets and having maintenance strategies specific to older machinery can help alleviate these challenges. - Data Overload
As more industries rely on IoT sensors and other technologies to monitor equipment performance, the sheer volume of data can be overwhelming. Proper data management systems and analytics tools are needed to extract meaningful insights and inform decision-making.
Best Practices for Effective Maintenance Planning and Control
- Implementing a CMMS (Computerized Maintenance Management System)
A CMMS is a powerful tool for managing maintenance operations. It allows for scheduling, work order management, tracking asset performance, and maintaining equipment histories, all of which contribute to a more efficient maintenance process. - Continuous Improvement
Regularly reviewing and refining maintenance strategies is essential for ensuring their effectiveness. Involving maintenance teams in feedback loops and fostering a culture of continuous improvement can help identify inefficiencies and enhance the overall process. - Collaborative Approach
Coordination between maintenance, production, and management teams is key to effective planning and control. Open communication ensures that maintenance schedules align with production needs and helps address potential disruptions. - Training and Development
Continuous training programs for maintenance staff are crucial. By keeping technicians updated on the latest tools, technologies, and best practices, organizations can ensure their teams are equipped to handle maintenance challenges efficiently.
Conclusion
Planning and control of maintenance systems are integral to the successful operation of any industrial organization. By implementing structured maintenance plans, allocating resources effectively, and adopting modern tools like CMMS and predictive maintenance technologies, companies can optimize their maintenance processes. This leads to improved equipment reliability, reduced downtime, lower costs, and enhanced safety. Proactive and strategic maintenance planning and control not only extend the life of assets but also drive overall business success, making it a fundamental aspect of operations management.