Positive displacement pumps operate on a different principle than centrifugal pumps. Positive displacement pumps physically entrap a quantity of liquid at the suction of the pump and push that quantity out the discharge of the pump.
A positive displacement pump is one in which a definite volume of liquid is delivered for each cycle of pump operation. This volume is constant regardless of the resistance to flow offered by the system the pump is in, provided the capacity of the power unit driving the pump or pump component strength limits are not exceeded. The positive displacement pump delivers liquid in separate volumes with no delivery in between, although a pump having several chambers may have an overlapping delivery among individual chambers, which minimizes this effect. The positive displacement pump differs from centrifugal pumps, which deliver a continuous flow for any given pump speed and discharge resistance.
Positive displacement pumps can be grouped into three basic categories based on their design and operation. The three groups are reciprocating pumps, rotary pumps, and diaphragm pumps.
Principle of Operation for PD pumps
- The flow delivered by a centrifugal pump during one revolution of the impeller depends upon the head against which the pump is operating. The positive displacement pump delivers a definite volume of fluid for each cycle of pump operation regardless of the head against which the pump is operating.
All positive displacement pumps operate on the same basic principle. This principle can be most easily demonstrated by considering a reciprocating positive displacement pump consisting of a single reciprocating piston in a cylinder with a single suction port and a single discharge port as shown in Figure. Check valves in the suction and discharge ports allow flow in only one direction. During the suction stroke, the piston moves to the left, causing the check valve in the suction line between the reservoir and the pump cylinder to open and admit water from the reservoir. During the discharge stroke, the piston moves to the right, seating the check valve in the suction line and opening the check valve in the discharge line. The volume of liquid moved by the pump in one cycle (one suction stroke and one discharge stroke) is equal to the change in the liquid volume of the cylinder as the piston moves from its farthest left position to its farthest right position.
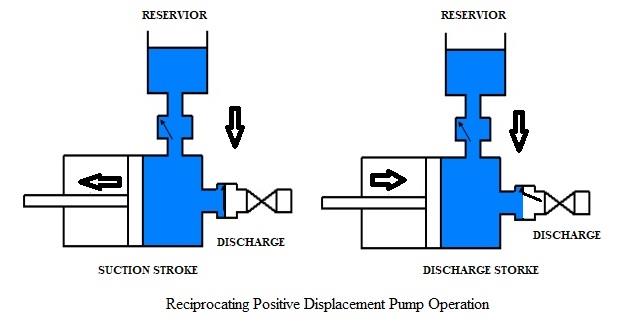
Positive Displacement Pumps types & Classification
Positive Displacement pumps are classified in several ways. Pumps may be classified:
- in terms of fixed or variable displacement or motion (rotary or reciprocating);
- in terms of type of drives (electric motor, gasoline engine, etc);
- in terms of manufacturer’s name, or service application.
Positive Displacement Pump Classification by Displacement or Motion
Positive displacement pumps can be Reciprocating or Rotary in motion. These are employed to produce steady positive displacement of a liquid.
Reciprocating Pumps
Reciprocating positive displacement pumps are generally categorized in four ways: direct-acting or indirect-acting; simplex or duplex; single-acting or double-acting; and power pumps.
Generally PD pumps are categorized as
Direct-Acting and Indirect-Acting Pumps
Simplex and Duplex Pumps
Single-Acting and Double-Acting Pumps
Power Pumps
Rotary Pumps
Simple Gear Pump
Lobe Type Pump
Screw-Type Positive Displacement Rotary Pump
Rotary Moving Vane Pump
Diaphragm Pumps
Positive Displacement Pump Protection
Positive displacement pumps are normally fitted with relief valves on the upstream side of their discharge valves to protect the pump and its discharge piping from over pressurization. Positive displacement pumps will discharge at the pressure required by the system they are supplying. The relief valve prevents system and pump damage if the pump discharge valve is shut during pump operation or if any other occurrence such as a clogged strainer blocks system flow.