Introduction to Centrifugal pumps
Centrifugal pumps are the most common type of pumps found in industrial applications. Centrifugal pumps enjoy widespread application partly due to their ability to operate over a wide range of flow rates and pump heads.
The centrifugal pump, as the name implies, uses centrifugal force to transfer fluids from one pressure to a higher pressure. Fluid enters the pump at the center of a rotating impeller. The rotating action literally flings the water to the outside of the impeller, thereby imparting a velocity or kinetic energy to it. This velocity or kinetic energy must now be converted to a pressure energy or more commonly known as pressure head.
Centrifugal pumps basically consist of a stationary pump casing and an impeller mounted on a rotating shaft. The pump casing provides a pressure boundary for the pump and contains channels to properly direct the suction and discharge flow. The pump casing has suction and discharge penetrations for the main flow path of the pump and normally has the small drain and vent fittings to remove gases trapped in the pump casing or to drain the pump casing for maintenance. Figure 1 is a simplified diagram of a typical centrifugal pump that shows the relative locations of the pump suction, impeller, volute, and discharge. The pump casing guides the liquid from the suction connection to the center, or eye, of the impeller. The vanes of the rotating impeller impart a radial and rotary motion to the liquid, forcing it to the outer periphery of the pump casing where it is collected in the outer part of the pump casing called the volute. The volute is a region that expands in cross-sectional area as it wraps around the pump casing. The conversion of the velocity head to pressure head is done in one of two ways, either by the use of a volute or diffuser vane rings. The volute is simply a scroll of increasing diameter around the periphery of the impeller. Due to this increasing volume, the velocity energy imparted to the fluid decreases and, since it cannot be destroyed, a pressure is developed. The purpose of the volute is to collect the liquid discharged from the periphery of the impeller at high velocity and gradually cause a reduction in fluid velocity by increasing the flow area. This converts the velocity head to static pressure. The fluid is then discharged from the pump through the discharge connection.
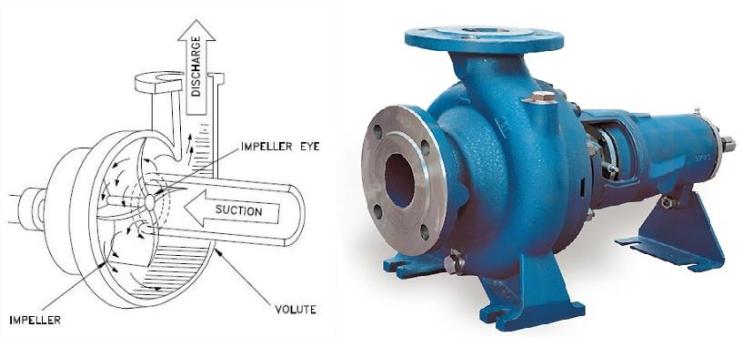
Centrifugal pumps can also be constructed in a manner that results in two distinct volutes, each receiving the liquid that is discharged from a 1800 region of the impeller at any given time. Pumps of this type are called double volute pumps (they may also be referred to a split volute pumps). In some applications, the double volute minimizes radial forces imparted to the shaft and bearings due to imbalances in the pressure around the impeller. A comparison of single and double volute centrifugal pumps are shown
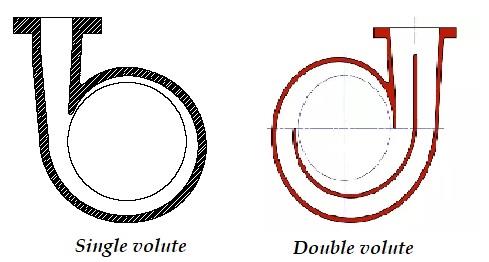
This method of producing a pressure head using volutes at one time was inefficient. However, improved design has raised its efficiency to that of a diffuser pump.
A diffuser is a set of stationary vanes that surround the impeller. The purpose of the diffuser is to increase the efficiency of the centrifugal pump by allowing a more gradual expansion and less turbulent area for the liquid to reduce in velocity. The diffuser vanes are designed in a manner that the liquid exiting the impeller will encounter an ever increasing flow area as it passes through the diffuser. This increase in flow area causes a reduction in flow velocity, converting kinetic energy into flow pressure.
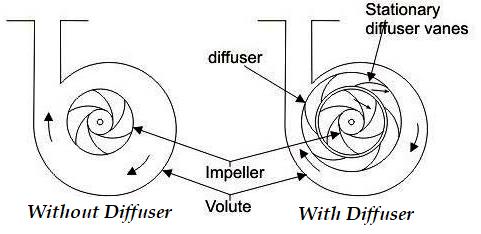