Submerged Arc Welding (SAW) and Welding Automation TIG, MIG/MAG COMPLETE SOLUTIONS IN WELDING AND CUTTING FROM ESAB
Submerged Arc Welding (SAW) is a highly efficient and reliable welding process widely used in heavy industries for joining thick metal plates and producing long, straight welds. With the integration of automation, SAW has become a cornerstone of modern manufacturing, ensuring high productivity, consistency, and superior weld quality.
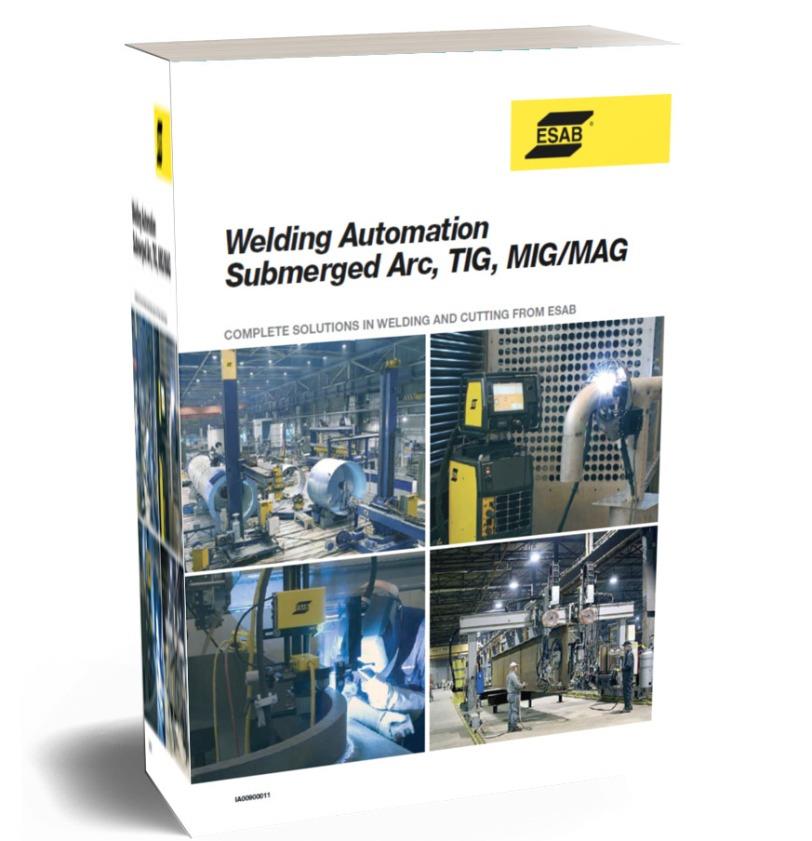
🔧 What is Submerged Arc Welding (SAW)?
Submerged Arc Welding is an arc welding process where the arc is struck beneath a blanket of granular flux, which completely covers the weld zone. This flux shields the molten metal from atmospheric contamination, ensuring high-quality welds. The process uses a continuously fed consumable electrode and typically operates with high currents and voltages, making it ideal for welding large workpieces.
⚙️ Key Components of SAW
- Power Source: Supplies constant voltage or current.
- Electrode Wire: Usually a solid or cored wire made of mild steel, alloy steel, or stainless steel.
- Flux: A granular, fusible material that provides shielding and slag formation.
- Welding Head: Mechanically guides the electrode and delivers flux.
- Travel System: Moves the torch along the joint in automated setups.
🏭 Why Automate Submerged Arc Welding?
Automating SAW enhances the inherent advantages of the process:
✅ Benefits of SAW Automation:
- Increased Productivity: Automation allows for continuous, long welds with minimal downtime.
- Consistent Quality: Robotic and mechanized systems maintain precise travel speed, arc length, and heat input.
- Reduced Labor Costs: One operator can monitor multiple machines, reducing human fatigue and error.
- Improved Safety: Automation removes workers from exposure to arc radiation, heat, and fumes.
- Optimal Deposition Rates: Especially useful in industries like shipbuilding, pipeline, and structural fabrication.
🤖 Types of SAW Automation Systems
- Gantry Systems: For welding large structures like pressure vessels and wind towers.
- Column and Boom Manipulators: Provide reach and flexibility for complex joints.
- Rotators and Positioners: Ensure the workpiece is always in the optimal welding position.
- CNC-Controlled Welders: Allow programmable control of weld paths and parameters.
🔍 Applications of Automated SAW
- Pressure vessels and boilers
- Structural steel fabrication
- Shipbuilding and offshore platforms
- Pipe and pipeline welding
- Wind tower manufacturing
- Bridge construction
🛠 Challenges and Solutions
Challenge | Solution |
---|---|
Initial setup cost | Long-term ROI through productivity gains |
Limited to flat or horizontal welds | Use of manipulators and rotators |
Flux handling and recovery | Integrated flux recovery systems |
Slag removal | Optimized parameters to minimize slag |
🌍 Future of SAW with Industry 4.0
With the rise of digital manufacturing, automated SAW is integrating:
- IoT Sensors for real-time monitoring
- AI/ML Algorithms for Predictive Maintenance
- Cloud Connectivity for centralized control
- AR Interfaces for operator training and diagnostics
🔚 Conclusion & Book
Submerged Arc Welding, when paired with automation, becomes a powerhouse of industrial fabrication. It offers unmatched efficiency, consistency, and quality, essential for meeting modern demands in construction, energy, and infrastructure sectors. As Industry 4.0 continues to evolve, automated SAW will play a pivotal role in shaping the future of welding technology.