Guide to Lockout/Tagout (LOTO)
Lockout/Tagout (LOTO) is a critical safety procedure designed to prevent the unexpected release of hazardous energy during equipment maintenance and servicing. This comprehensive guide covers everything you need to know about Lockout/Tagout, from understanding its importance to ensuring compliance with OSHA regulations.
Table of Contents
ToggleUnderstanding Lockout/Tagout
What is Lockout/Tagout and What Does It Mean for You?
Lockout/Tagout (LOTO) refers to the practice of locking and tagging energy sources to prevent accidental start-up or release of energy during maintenance work. The primary objective is to protect workers from potentially hazardous energy while they perform tasks such as servicing machines or equipment.
The “lockout” portion involves using a physical lock to isolate energy sources, ensuring that machinery cannot be inadvertently energized. The “tagout” portion involves placing a tag on the energy-isolating device to alert workers that the equipment is undergoing maintenance and should not be operated.
For both employers and employees, LOTO is an essential safety practice that can save lives. It requires strict adherence to procedures to minimize the risk of electrical, mechanical, hydraulic, and other types of energy-related accidents. Implementing a successful Lockout/Tagout program reduces the risk of workplace injuries and fatalities, making it an indispensable part of any safety plan.
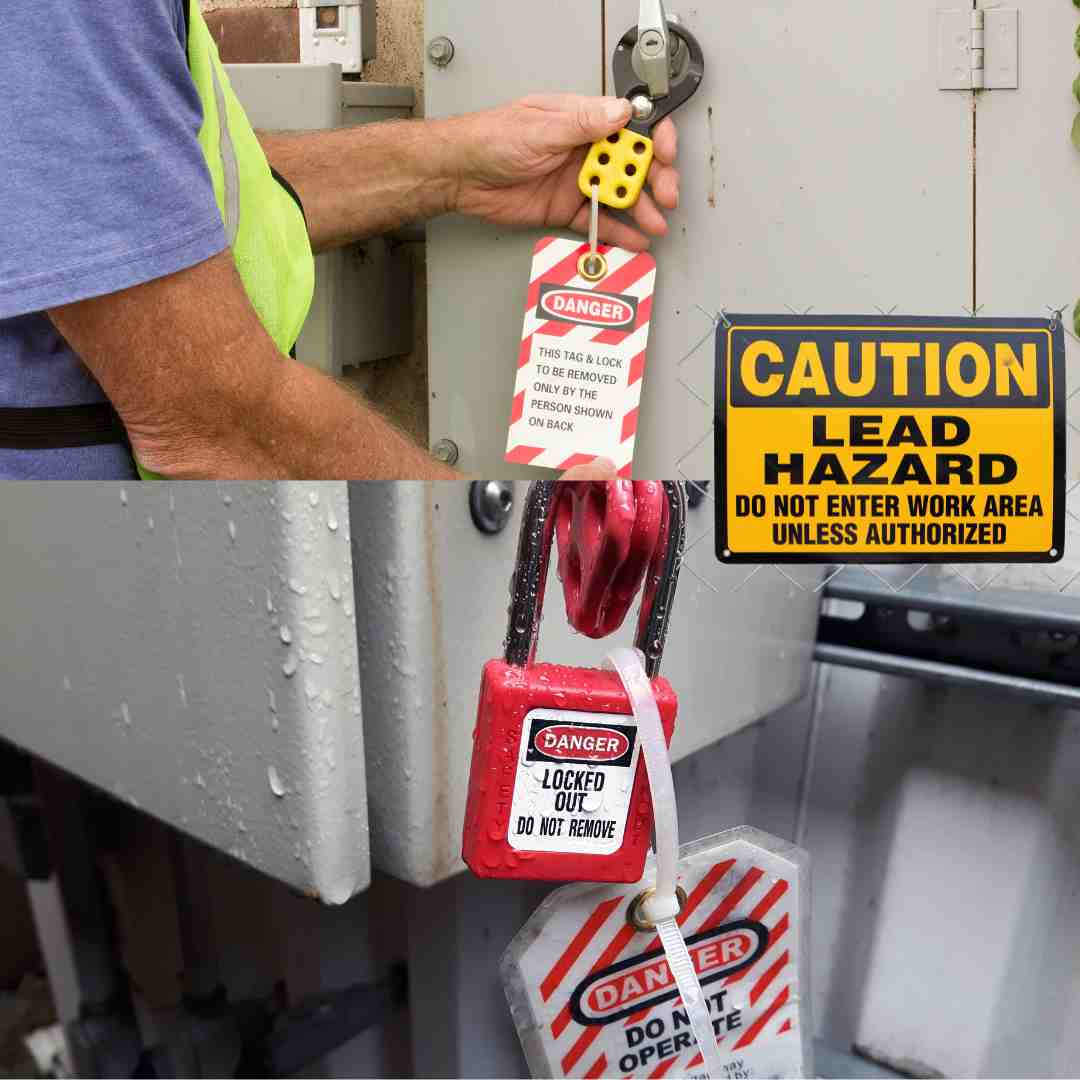
Regulatory Overview
Get to Know the Requirements Behind This Safety Must-Have
Lockout/Tagout is governed by specific OSHA regulations designed to ensure that hazardous energy is properly controlled during maintenance. The key regulation is OSHA standard 1910.147, which sets requirements for the control of hazardous energy sources. This standard is critical for ensuring the safety of workers who maintain machinery and equipment.
Key requirements of OSHA’s Lockout/Tagout standard include:
- Energy Control Procedures: Employers must develop, document, and implement energy control procedures for machinery and equipment.
- Training and Education: Workers must be trained to understand and apply lockout/tagout procedures. They should be able to recognize hazardous energy sources and know how to de-energize equipment safely.
- Inspection: Employers must periodically inspect their lockout/tagout program to ensure it is being properly followed.
- Use of Proper Devices: Lockout devices, including locks, tags, and other energy-isolating tools, must be durable, standardized, and clearly identifiable.
6 Essential Elements for Compliance
Find Out What You Need to Get Your Lockout Program on the Right Path
To ensure Lockout/Tagout compliance, employers must incorporate several key elements into their safety program. These essential elements are foundational to keeping workers safe and meeting regulatory requirements. Here are the six core components:
- Energy Control Procedures: Develop clear, written procedures to control hazardous energy. These procedures should identify energy sources, how to isolate them, and how to lockout and tagout equipment.
- Employee Training: All employees involved in the Lockout/Tagout process must receive comprehensive training. They should understand the energy control procedures and the potential risks associated with their jobs.
- Periodic Inspections: Regular inspections are necessary to ensure the lockout/tagout procedures are being followed. These inspections should be conducted by qualified personnel and should focus on evaluating whether workers are correctly applying the procedures.
- Proper Lockout Devices: Ensure that locks, tags, and other energy isolation devices are standardized, durable, and easily identifiable. These devices should not be removed or bypassed without proper authorization.
- Program Documentation: Document all procedures, training, and inspections as part of the Lockout/Tagout program. This ensures accountability and provides a reference for future evaluations and audits.
- Employee Involvement: Involve workers in the development and review of lockout procedures. Their hands-on experience can offer valuable insights and help improve safety practices.
By adhering to these six essential elements, you can create a robust Lockout/Tagout program that keeps workers safe and helps you comply with OSHA regulations.
The Cost of Non-Compliance
Not Sure It’s Worth It? Think Again!
Failing to comply with Lockout/Tagout regulations can result in significant costs—both financial and human. The penalties for non-compliance can be severe, including hefty fines, legal fees, and possible shutdowns of operations.
However, the true cost of non-compliance goes beyond fines. Workplace accidents resulting from improper energy control can lead to serious injuries or fatalities. This not only impacts the affected workers but can also damage a company’s reputation, decrease employee morale, and result in lost productivity.
Additionally, the legal ramifications of non-compliance can be far-reaching. OSHA inspections and subsequent citations for Lockout/Tagout violations can lead to costly legal battles and long-term damage to your company’s standing in the industry.
On the flip side, implementing a comprehensive LOTO program can save money by preventing accidents, reducing downtime, and avoiding expensive legal penalties. When viewed through this lens, investing in a proper Lockout/Tagout system is a smart, cost-effective decision that safeguards both employees and company assets.
Lockout/Tagout Program Checklist
Evaluate the Current State of Your Program and See How It Stacks Up
To ensure your Lockout/Tagout program is effective, it’s crucial to regularly evaluate its implementation. Use the following checklist to assess whether your program meets compliance standards:
- Are energy control procedures documented and up-to-date?
- Is there a designated team responsible for overseeing the Lockout/Tagout program?
- Have all employees received proper LOTO training?
- Are proper lockout devices and tags readily available?
- Is there a system in place for inspecting and auditing the LOTO procedures?
- Are workers involved in the ongoing development and improvement of energy control procedures?
If your program is lacking in any of these areas, it’s time to make improvements. Regular self-assessments will help ensure that your LOTO program remains compliant, effective, and a key part of your workplace safety culture.
The Path to World-Class Compliance
Learn What It Takes to Go Above and Beyond Compliance Basics
Achieving world-class Lockout/Tagout compliance involves more than just meeting the minimum requirements. To go above and beyond compliance basics, consider these additional best practices:
- Continuous Improvement: Regularly review and update energy control procedures to reflect changes in equipment, technology, and workforce needs.
- Advanced Training: Offer advanced training programs for workers to stay current with best practices and new regulations. This keeps employees engaged and reinforces the importance of safety.
- Behavior-Based Safety: Implement behavior-based safety programs that focus on the actions of employees and how they affect safety. Encourage workers to report unsafe practices and reward those who follow LOTO procedures consistently.
- Incorporate Technology: Use technology such as mobile apps and digital checklists to streamline the Lockout/Tagout process. This can enhance communication, increase accountability, and ensure real-time compliance monitoring.
- Management Leadership: Strong commitment from leadership is essential. Leadership should actively participate in safety initiatives, set the example, and allocate resources to ensure the Lockout/Tagout program remains a priority.
Control of Hazardous Energy and OSHA Lockout/Tagout Requirements
The OSHA Lockout/Tagout standard (1910.147) focuses on controlling hazardous energy during maintenance work to prevent injuries. This requires employers to create written procedures for energy control, conduct employee training, and implement a program of periodic inspections. The standard applies to all industries that have employees performing maintenance or servicing tasks on machines or equipment that could release hazardous energy. Compliance with these requirements is not optional—it is crucial for worker safety and legal adherence.
By understanding Lockout/Tagout principles and implementing an effective program, businesses can protect their employees, ensure legal compliance, and reduce the risk of accidents in the workplace.
The Importance of Lockout/Tagout in Workplace Safety
Lockout/Tagout is one of the most essential safety practices in industrial settings. Workers who service machinery or equipment are exposed to potential hazards such as electrical shocks, burns, or mechanical accidents if hazardous energy is not properly controlled. Without the effective implementation of Lockout/Tagout protocols, there is an increased risk of injuries or fatalities resulting from unexpected equipment startup, the release of stored energy, or mechanical failure.
This safety procedure not only protects workers but also enhances overall workplace productivity and morale. When employees feel safe in their work environment, they are more likely to be engaged, satisfied, and less likely to take unsafe shortcuts. A well-established Lockout/Tagout program reinforces a culture of safety, reducing the likelihood of accidents and fostering trust in the organization’s commitment to worker protection.
Energy Types Controlled by Lockout/Tagout
Lockout/Tagout procedures apply to a wide range of hazardous energy types that could pose a risk to workers during maintenance. These include:
- Electrical Energy: This can include high-voltage electrical sources, capacitors, and any energy source that could cause electrical shock or burns.
- Mechanical Energy: Stored energy in springs, gears, flywheels, and other moving parts could result in severe injuries if released unexpectedly.
- Hydraulic Energy: Fluids under pressure in hydraulic systems, like those in presses and other machinery, can cause serious injury if released without warning.
- Pneumatic Energy: Compressed air or gas can result in injuries, such as flying debris or pressurized components being released unexpectedly.
- Thermal Energy: Hot surfaces or steam systems can cause burns or fires if energy is not properly isolated.
- Chemical Energy: Hazardous chemicals or vapors can pose significant risks, such as exposure to toxic substances, fires, or explosions if control systems fail.
Common Lockout/Tagout Devices
The effectiveness of a Lockout/Tagout program depends largely on the proper use of devices that can prevent hazardous energy from being released. Common lockout and tagout devices include:
- Lockout Devices: These devices physically prevent the operation of energy-isolating devices such as switches, valves, and circuit breakers. The lock is applied to the device to keep it in the “off” position, making it impossible for anyone to activate the equipment while work is being performed.
- Tagout Devices: Tagout devices are warning signs that are attached to energy-isolating devices. These tags should clearly indicate that the equipment is under maintenance and should not be operated. While tagout devices do not physically prevent energy flow, they serve as a visual warning to other workers.
- Padlocks: Used as part of lockout devices, padlocks are commonly used to secure energy-isolating devices, ensuring that unauthorized personnel cannot access or start equipment during servicing.
- Valve Lockout Devices: These are used to lock valves in the closed position, preventing the accidental release of fluids or gases during maintenance.
- Circuit Breaker Lockouts: These devices prevent electrical breakers from being turned on while maintenance is being performed, protecting workers from electrical hazards.
- Hasps: Used for situations where multiple workers are involved in maintenance. A hasp allows more than one worker to place their individual locks on the same energy-isolating device.
Lockout/Tagout Program Implementation and Best Practices
The success of a Lockout/Tagout program depends on how well it is implemented and followed. To ensure that your program is effective, follow these best practices:
- Create Written Lockout Procedures: Every machine or piece of equipment should have a written Lockout/Tagout procedure. This includes step-by-step instructions for isolating hazardous energy and verifying that the energy has been de-energized.
- Train All Employees: All workers who operate or maintain machinery should be trained in Lockout/Tagout procedures. This training should include how to apply and remove locks and tags, recognize hazardous energy sources, and understand the importance of compliance.
- Conduct Regular Inspections: Periodic inspections should be carried out to ensure that Lockout/Tagout procedures are being followed properly. These inspections should be documented, and corrective actions should be taken if deficiencies are identified.
- Involve Employees in Program Development: Workers who are directly involved in maintenance tasks are often the best source of input for developing and refining Lockout/Tagout procedures. Involving employees in this process ensures that procedures are practical and effective.
- Keep Lockout Devices Accessible: Ensure that all workers have easy access to lockout devices and know where they are stored. Devices should be standardized to prevent confusion or misuse.
- Use Clear Labels and Tags: All lockout devices and tags should be clearly labeled to identify the machine or system being worked on. Tags should include the worker’s name and the date to ensure accountability.
- Review and Update Procedures Regularly: Energy control procedures should be reviewed and updated regularly to account for changes in equipment, processes, or work practices. Any changes should be reflected in the Lockout/Tagout program documentation.
- Use Technology to Track Lockout/Tagout Actions: Some organizations are now using software or mobile applications to track Lockout/Tagout actions in real-time. This technology can improve compliance by providing documentation and audit trails.
Conclusion
In industries where workers interact with complex machinery or energy systems, Lockout/Tagout is an essential safety practice that ensures the well-being of all employees. The main objective of a Lockout/Tagout program is simple: protect workers from hazardous energy during maintenance or servicing tasks. By following the proper procedures, using the correct devices, and fostering a safety-conscious culture, businesses can significantly reduce the risk of workplace accidents.
The implementation of Lockout/Tagout procedures is not only a regulatory requirement but also a moral obligation. Non-compliance can lead to costly penalties, increased insurance premiums, and most importantly, preventable injuries or fatalities. Businesses that prioritize Lockout/Tagout programs are better positioned to maintain a safe, productive, and compliant workplace.
Whether you are just starting to develop your Lockout/Tagout program or are looking to enhance an existing one, it’s important to remember that safety always comes first. By taking the necessary steps to ensure your energy control procedures are comprehensive, well-documented, and effectively communicated, you can protect your workers and your business from the hazards associated with hazardous energy.