First steam turbine and History of steam turbines
Historically, the first steam turbine of which we have proof was built by Heron of Alexandria around 175 BC, which consisted of a metal sphere with two nozzles at their poles and was oriented in the same direction where the steam escaped. The sphere rotated diametrically, resting on the boiler through the steam inlet nozzles. Until 1629 there is no record of a new independent design of a steam turbine, Giovanni Brance used a steam jet to drive the rotation of a water mill wheel, although I can not apply it to any useful industrial use. Speed staggering occurs in the reaction turbine. This staggering consists in producing a large pressure drop in a group of nozzles and using the resulting velocity of the steam in as many groups of blades as necessary by means of a set of straighteners reorienting the steam output of the first stage so that it enters in a second runner.
Introduction
Steam turbines are essential components in power generation and industrial processes, harnessing the energy contained in steam flow to produce mechanical work. The classification and types of steam turbines are determined by several factors, including the form of energy utilization, the number of stages, the direction of steam flow, the presence of steam extraction, and the steam outlet pressure. In this article, we will delve into each of these classifications and explore the characteristics and applications of different types of steam turbines.
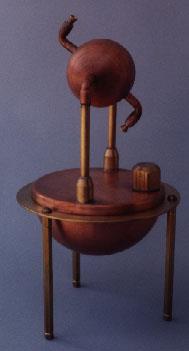
Types of steam turbines
The classification and types of the steam turbines can be done according to the form of use of the energy contained in the steam flow (reaction or impulse), according to the number of stages (multistage or single stage), according to the steam flow direction (axial or radial), if there is steam extraction or not before reaching the exhaust and finally by the steam outlet pressure (back pressure, free exhaust or condensation).
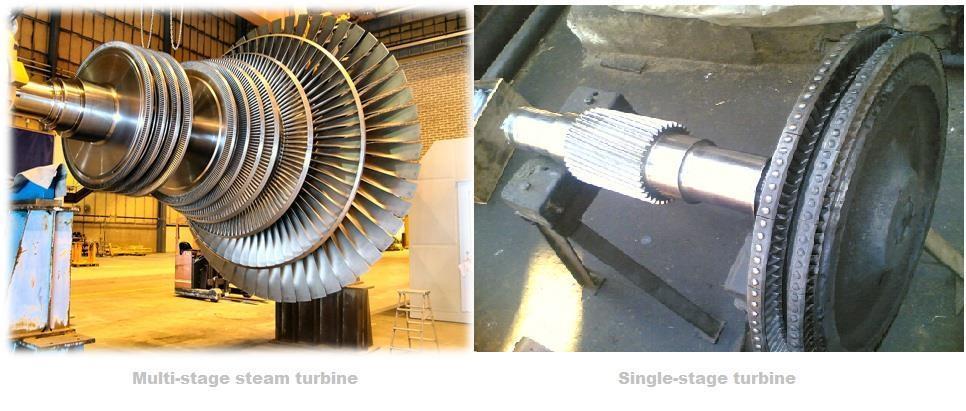
Understanding Energy Utilization
Impulse Turbine
An impulse turbine operates by utilizing the kinetic energy of steam. In this type of turbine, the steam maintains the same static pressure before and after passing through the rotor. The conversion of pressure energy into kinetic energy occurs in the fixed nozzles of the distributor, rather than in the rotor itself. The pressure drop only takes place within the nozzles. Impulse turbines are known for their simplicity and are commonly used in applications where efficiency is not the primary concern.
Reaction Steam Turbine
In contrast to impulse turbines, reaction steam turbines harness both kinetic and pressure energy of steam. As the steam expands in the moving blades of a reaction turbine, a continuous pressure drop and velocity increase occur. The pressure drop happens progressively throughout the turbine. Reaction steam turbines are widely employed in power generation due to their higher efficiency compared to impulse turbines.
Number of Stages
Single-Stage Steam Turbine
Single-stage steam turbines are designed for relatively low power outputs, typically up to 2 MW. These turbines are known for their simple construction, robustness, and safety. They have lower installation and maintenance costs compared to their multi-stage counterparts. Single-stage turbines are commonly used in small-scale power generation and industrial processes.
Multi-Stage Steam Turbine
Multi-stage steam turbines consist of multiple stages, each comprising a set of stationary blades (stators) and moving blades (rotors). The primary objective of employing multiple stages is to reduce the speed of the impeller while maintaining a blade velocity close to the optimal value relative to the steam jet speed. Without the inclusion of multiple stages, excessively high steam pressure would require the turbine to rotate at unmanageably high speeds. Multi-stage turbines achieve higher efficiencies than single-stage turbines and are capable of handling higher-pressure steam flows. They are predominantly used in high-power applications. Mixed turbines that combine both reaction and impulse stages are often employed, with the first stages utilizing impulse action and the latter stages relying on reaction principles.
Steam Flow Direction
Axial Flow Turbine
Axial flow turbines are the most commonly used type of steam turbines. The steam passage in an axial flow turbine follows a cone that shares the same axis as the turbine. This design enables efficient energy transfer as the steam flows parallel to the axis of rotation. Axial flow turbines find extensive applications in power generation, particularly in large-scale power plants.
Radial Flow Turbine
In a radial flow turbine, the steam flow occurs in all directions perpendicular to the axis of the turbine. This type of turbine is less common than axial flow turbines but is suitable for specific applications where radial steam flow is advantageous. Radial flow turbines are often employed in small-scale power generation and niche industrial processes.
Steam Extraction
Turbine with Steam Extraction
Turbines with steam extraction allow for the extraction of steam at high-pressure stages. Part of the extracted steam is redirected back to the boiler for reheating before being sent to intermediate stages. In certain cases, steam can also be extracted from specific stages for utilization in other industrial processes. Turbines with steam extraction enhance overall system efficiency and facilitate energy integration with various applications.
Steam Outlet Pressure
Backpressure Turbine
A backpressure turbine operates with the steam pressure at the turbine outlet being higher than atmospheric pressure. Typically, it is connected to an initial condenser where the steam is condensed, resulting in the generation of hot or superheated water. This allows for subsequent thermal utilization of the condensed water. Backpressure turbines are commonly used in cogeneration systems and applications where both mechanical and thermal energy are required.
Condensing Turbines
Condensing turbines are designed to operate with the steam outlet pressure below atmospheric pressure. This design allows for greater energy utilization compared to backpressure turbines. By condensing the steam, cooling water can be obtained, enabling efficient heat transfer and subsequent use. Condensing turbines are predominantly used in high-power applications where maximizing energy efficiency is crucial.
Conclusion
In summary, steam turbines are classified and categorized based on several factors, including energy utilization, number of stages, steam flow direction, steam extraction, and steam outlet pressure. Each type of turbine has distinct characteristics and finds applications in various industries. Understanding the different classifications of steam turbines is essential for selecting the most suitable turbine for a particular power generation or industrial process.
Steam Turbines Books
FAQs
- What is the purpose of steam extraction in a turbine?
- Steam extraction allows for the utilization of high-pressure steam at different stages, enhancing overall system efficiency and enabling energy integration with other industrial processes.
- What are the advantages of multi-stage steam turbines over single-stage turbines?
- Multi-stage steam turbines offer higher efficiencies, can handle higher-pressure steam flows, and are suitable for high-power applications. They achieve these benefits by reducing the speed of the impeller through multiple stages.
- Why are axial flow turbines widely used in power generation?
- Axial flow turbines are preferred in power generation due to their efficient energy transfer, allowing steam to flow parallel to the axis of rotation. This design facilitates the generation of mechanical work with high efficiency.
- How do backpressure turbines differ from condensing turbines?
- Backpressure turbines operate with a steam outlet pressure higher than atmospheric pressure while condensing turbines operate with a steam outlet pressure below atmospheric pressure. This distinction affects the subsequent utilization of the steam and the overall energy efficiency.
- Can radial flow turbines be used in large-scale power plants?
- Radial flow turbines are less common in large-scale power plants. They are more suitable for small-scale power generation and niche industrial processes where radial steam flow provides advantages in specific applications.