Risk Assessment: A Practical Guide to Assessing Operational Risks
Introduction
Risk assessment is a cornerstone of effective operational management, enabling organizations to identify, evaluate, and mitigate potential threats to their objectives. Whether in manufacturing, healthcare, construction, or any other sector, understanding and managing risks is critical for ensuring safety, efficiency, and resilience. This article provides a practical guide to assessing operational risks, outlining key concepts, methodologies, and best practices to help organizations safeguard their people, assets, and reputation.
What is Risk Assessment?
Risk assessment is a systematic process of identifying hazards, analyzing the likelihood and potential impact of these hazards, and determining the necessary controls to mitigate or eliminate risks. It is a proactive approach that helps organizations anticipate challenges and implement measures to prevent accidents, disruptions, or losses.
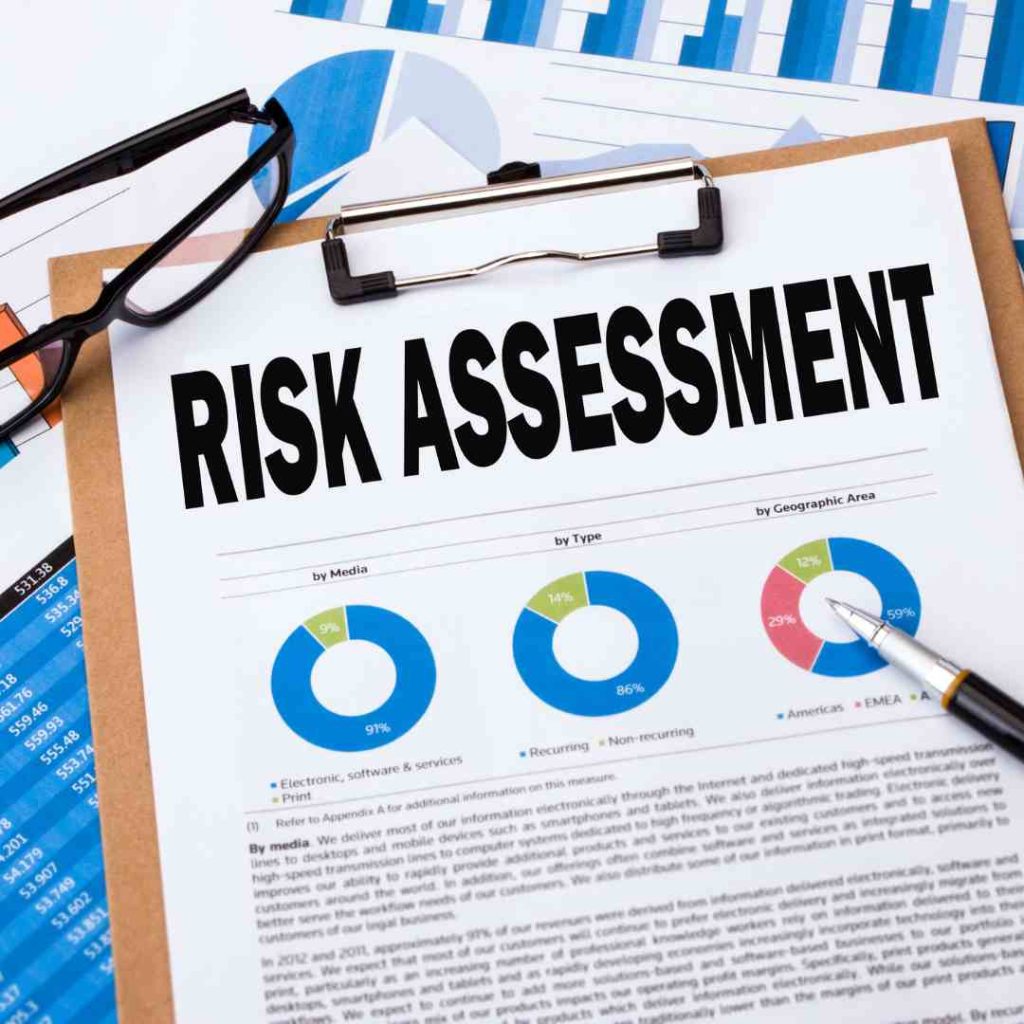
The process typically involves three key steps:
- Risk Identification: Recognizing potential hazards or vulnerabilities.
- Risk Analysis: Evaluating the probability and severity of identified risks.
- Risk Mitigation: Implementing strategies to control or reduce the risks.
By integrating risk assessment into their operations, organizations can make informed decisions that enhance safety, compliance, and operational efficiency.
Why is Risk Assessment Important?
The importance of risk assessment cannot be overstated. It provides numerous benefits, including:
Enhanced Safety: Identifying and addressing hazards reduces the likelihood of workplace accidents and injuries.
Regulatory Compliance: Risk assessment ensures compliance with legal and industry standards, avoiding penalties and legal disputes.
Operational Continuity: Proactive risk management minimizes disruptions, enabling organizations to maintain productivity and service delivery.
Cost Savings: Preventing incidents reduces expenses related to insurance claims, fines, and downtime.
Improved Decision-Making: A structured approach to risk assessment provides clarity and confidence in planning and resource allocation.
Key Steps in Conducting a Risk Assessment
Step 1: Identify the Risks
Risk identification is the foundation of any effective assessment. It involves:
Mapping Processes: Break down operations into individual tasks to identify where risks might occur.
Consulting Stakeholders: Engage employees, supervisors, and experts who understand the nuances of the work.
Reviewing Past Incidents: Analyze historical data, such as accident reports, to uncover recurring risks.
Considering External Factors: Account for external influences like weather, supply chain disruptions, or regulatory changes.
Tools such as checklists, brainstorming sessions, and inspections can be invaluable during this phase.
Step 2: Analyze the Risks
Once risks are identified, the next step is to analyze their likelihood and impact. This can be achieved by:
Qualitative Analysis: Categorize risks based on subjective criteria, such as high, medium, or low likelihood and severity.
Quantitative Analysis: Use numerical data to calculate probabilities and potential losses, providing a more precise evaluation.
Risk Matrices: Plot risks on a matrix to visualize their relative significance and prioritize them accordingly.
For example, a risk matrix might rank a high-likelihood, high-impact event as critical, while a low-likelihood, low-impact event may be deemed negligible.
Step 3: Implement Control Measures
Risk mitigation involves selecting and applying appropriate control measures to reduce risks to acceptable levels. These measures fall into the following categories:
Elimination: Remove the hazard entirely, such as discontinuing a risky procedure.
Substitution: Replace hazardous materials or processes with safer alternatives.
Engineering Controls: Design or modify equipment to isolate people from hazards.
Administrative Controls: Develop policies, training, or schedules to minimize exposure.
Personal Protective Equipment (PPE): Provide gear to protect employees from residual risks.
The hierarchy of controls emphasizes prioritizing measures that address risks at their source.
Step 4: Monitor and Review
Risk assessment is not a one-time exercise. Continuous monitoring and periodic reviews are essential to ensure controls remain effective. This involves:
- Regularly inspecting workplaces and equipment.
- Updating assessments in response to changes in operations or regulations.
- Gathering feedback from employees to identify new or evolving risks.
- Analyzing the effectiveness of implemented controls.
By maintaining an iterative process, organizations can adapt to changing circumstances and sustain a robust risk management program.
Best Practices for Effective Risk Assessment
To maximize the effectiveness of your risk assessment efforts, consider the following best practices:
- Engage Stakeholders: Involve employees at all levels to gain diverse perspectives and foster a shared commitment to safety.
- Use Standardized Tools: Adopt consistent templates, checklists, and methodologies to streamline the process and ensure thoroughness.
- Integrate with Business Processes: Embed risk assessment into daily operations, such as project planning, procurement, and maintenance.
- Leverage Technology: Utilize software and data analytics to automate risk identification, tracking, and reporting.
- Focus on Training: Equip employees with the knowledge and skills to recognize hazards and respond effectively.
- Document Thoroughly: Maintain detailed records of assessments, decisions, and actions to demonstrate compliance and facilitate audits.
Common Challenges in Risk Assessment
Despite its benefits, risk assessment can present challenges, including:
Inadequate Data: Limited information on risks or past incidents may hinder accurate analysis.
Resource Constraints: Small organizations may lack the time, expertise, or budget to conduct comprehensive assessments.
Resistance to Change: Employees or managers may be skeptical of new processes or perceive them as overly burdensome.
Overcomplexity: Excessive detail or overly technical methodologies can make the process daunting and inefficient.
Addressing these challenges requires clear communication, leadership support, and a focus on practicality and relevance.
Industry Applications of Risk Assessment
Risk assessment is vital across industries, with specific applications tailored to different operational contexts. Examples include:
Construction: Identifying hazards like falls, equipment malfunctions, or exposure to hazardous materials on job sites.
Healthcare: Assessing risks related to patient handling, infection control, or medical equipment use.
Manufacturing: Evaluating risks in machinery operation, chemical handling, or ergonomic factors.
Transportation: Managing risks in vehicle operation, route planning, or cargo handling.
Each industry benefits from customized approaches that address unique challenges and regulatory requirements.
Conclusion
Risk assessment is an indispensable tool for managing operational risks and ensuring organizational resilience. By systematically identifying, analyzing, and mitigating risks, organizations can protect their people, assets, and reputation while achieving compliance and operational excellence. This practical guide highlights the importance of integrating risk assessment into daily operations, adopting best practices, and maintaining a culture of continuous improvement. With a proactive approach to risk management, organizations can navigate uncertainties and seize opportunities with confidence.