The boiler drum is where water and steam are separated. Maintaining the correct boiler drum level is critical for the safe operation of a boiler. A low water level may uncover the water tubes exposing them to heat stress and damage and a High level may carry over water droplets exposing the steam turbines to damage. The level control problem is complicated by transients known as shrink and swell. This is a decreased or an increased drum level signal because of the formation of less or more vapor bubbles in the drum water while there is actually no change in the amount of water in the drum.
The design of the boiler drum level control strategy is normally described as single-element, two-element, or three-element control. This blog explains the three designs.
Single-element drum level control
Single-element drum level control is the simplest type used for controlling fire tubes and small packaged water tube boilers. Control is based only on boiler drum level and hence has no compensation of any shrink or swell. It is suitable only for small boilers with slow load changes.
Limitation of single-level control:
• Increase in demand decreases steam pressure
• Gives rise to the expansion of bubbles and drum level swell
• Feedwater flow rate decreases while an increase of flow rate is needed to maintain mass balance
• Sudden or large load changes give rise to the phasing of shrink and swell
• Water level controller loses control
• Nuisance of low water trips or water priming and carryover
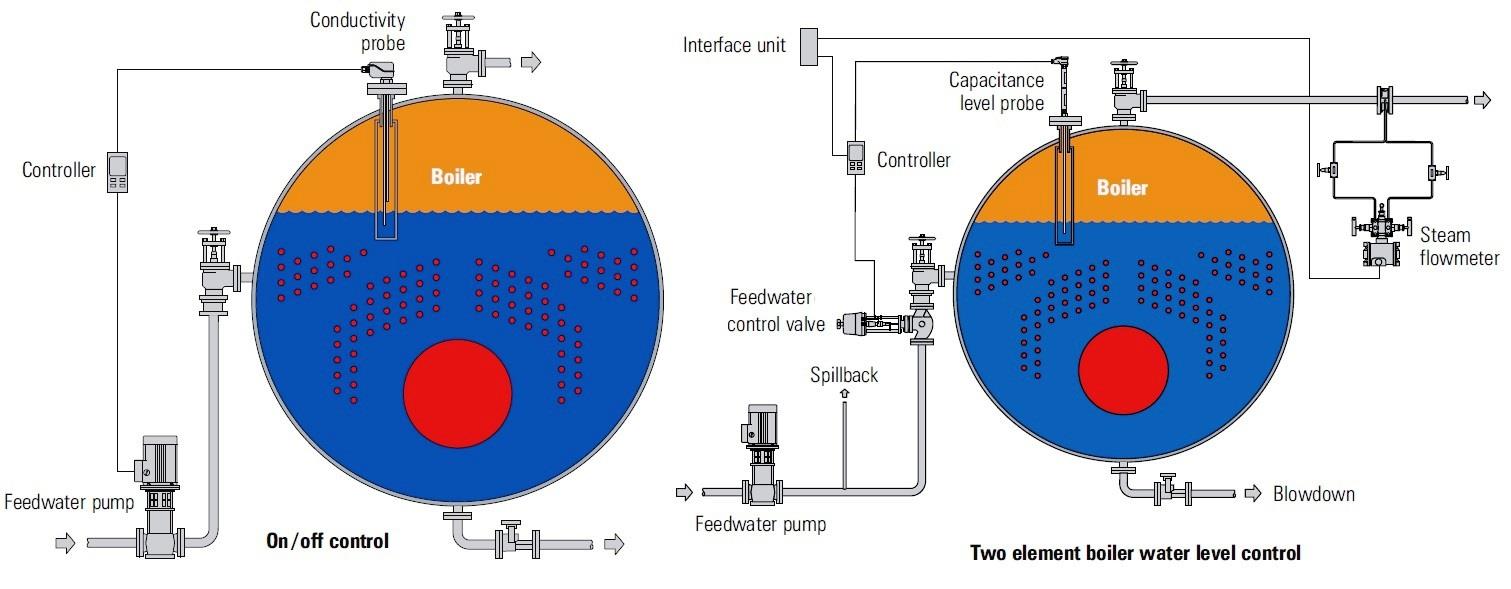
Two-element drum level control
Two-element drum level control measures steam flow along with boiler drum level. The steam flow signal is used in a feed-forward control loop to anticipate the need for an increase in feedwater flow to maintain a constant drum level. This requires the Δp across the feedwater CV to remain constant, as well as the CV signal versus flow profile. Small- and medium-sized boilers with moderate load changes can be controlled this way.
Limitations of two-element control
•Can not adjust pressure or load disturbance of the feedwater flow
•Can not eliminate the phasing interaction between the feedwater flow and drum level as only a slow process of drum level is controlled
•The second issue can lead to a high subcooling of the drum water on a large increase of steam demand due to excessive feed water entry
Three-element drum level control
The control is based on three parameters – mainly a) Drum level b) steam flow c) feedwater flow. Errors of these three elements are computed and control signals are generated to position the selected full load control valves (30% – 100 %).
Three-element drum level control further adds a feedwater flow signal to those used in two-element feedwater control. The drum level controller manipulates the feedwater flow set point in conjunction with feed-forward from the steam flow measurement. The feed-forward component keeps the feedwater supply in balance with the steam demand. The drum level controller trims the feedwater flow set point to compensate for errors in the flow measurements or any other unmeasured load disturbances (e.g. blowdown) that may affect the drum level. Three-element control is used in boilers that experience wide, fast load changes and is the most widely used form of feedwater and drum level control.
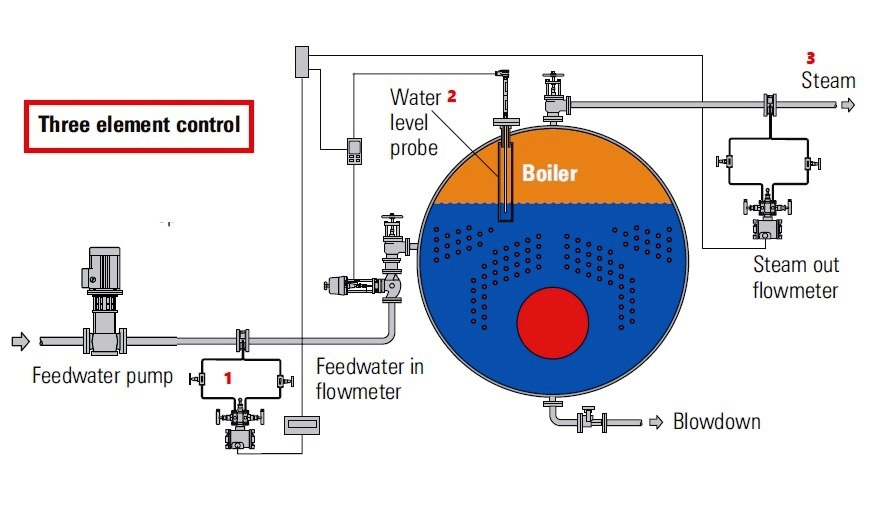
Advantages of 3element control
The basic two-element controller is cascaded to the feedwater flow controller to act as a remote setpoint
•Feed water controller (first controller) uses feedwater flow as the process variable and steam flow as the set point
•The set point of the two-element controller at just itself
•Minor losses like blowdowns can be taken care off
•Independent tuning of each controller
•Can handle large and rapid load change
•Suitable for any boiler size
•Must for multiple boilers with a common feedwater heater
•No trim correction stroke supervision needed