Welding technology continues to evolve as an integral part of modern engineering, offering precision, strength, and efficiency in joining materials. As industries demand tighter tolerances, higher strength-to-weight ratios, and greater productivity, the quality and application of various welding processes—ranging from electron beam welding to friction stir and laser welding—have come under rigorous scientific and engineering scrutiny.
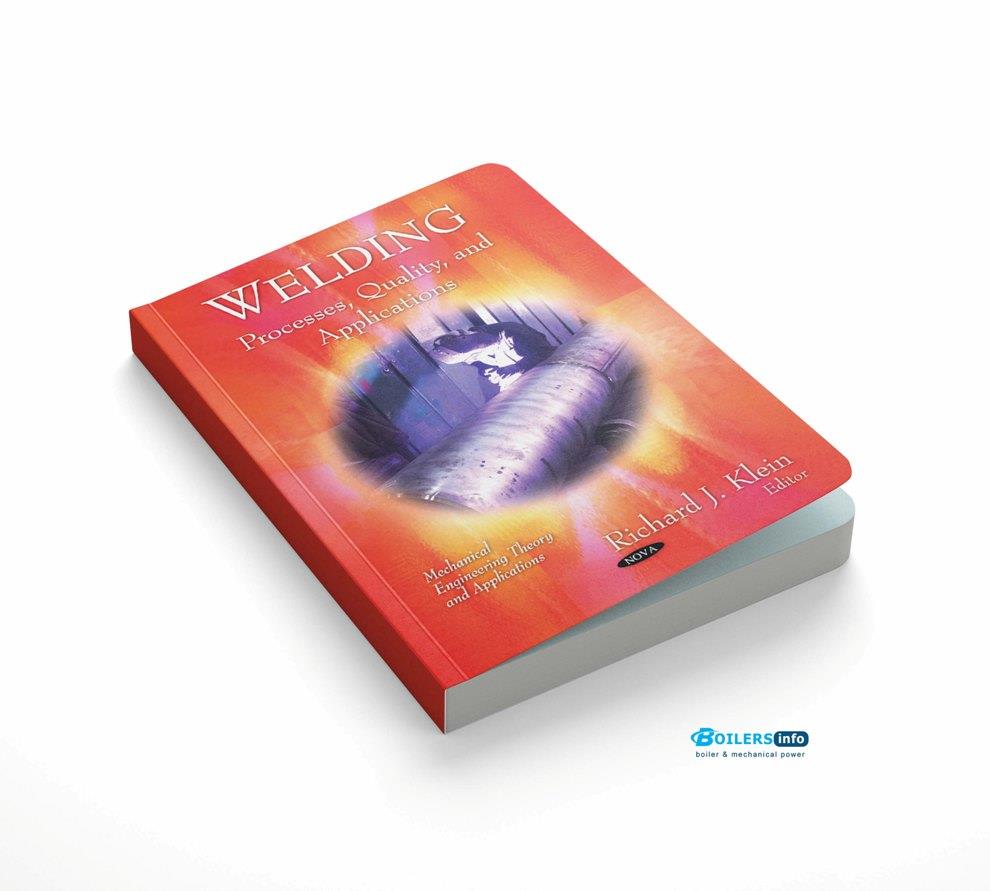
1. High-Brightness Electron Beam Welding: Precision and Control
Electron Beam Welding (EBW) stands at the pinnacle of high-precision joining technologies, especially in aerospace and nuclear applications. The development of high-brightness electron guns, as explored by Mladenov and Koleva, has significantly improved beam focusing, enhancing penetration depth and joint integrity. The beam’s quality, characterized by its intensity and stability, directly influences the microstructure and mechanical properties of the weld. Accurate control over the cathode design and beam optics is crucial for delivering focused energy with minimal defects.
2. Process Parameter Optimization in EBW
Koleva and Mladenov further extend their work by presenting strategies for process parameter optimization in EBW. Electron beam parameters such as voltage, current, and welding speed must be finely tuned for each material and geometry to ensure consistent fusion without porosity or cracking. Optimization techniques, including Design of Experiments (DoE) and simulation-based predictive modeling, are increasingly used to improve process reliability and weld quality.
3. Automated TIG Welding: Enhancing Repeatability
Automation in TIG (Tungsten Inert Gas) welding, particularly for complex geometries like shells, significantly improves quality and repeatability. Iqbal, Dar, and Qureshi demonstrate how integrating artificial intelligence and control algorithms can automate parameter selection and torch movement. This not only reduces human error but also ensures consistent penetration and aesthetic finish, crucial for applications in pressure vessels and piping.
4. Friction Stir Welding (FSW): Material Flow and Versatility
FSW is a solid-state joining process known for producing defect-free joints with excellent mechanical properties. Almanar and Hussain’s study highlights the importance of material flow behavior, especially when welding dissimilar metals. Understanding the thermomechanical interactions during stirring is vital to prevent void formation and ensure homogeneity. FSW’s adaptability makes it suitable for automotive and aerospace industries where lightweight and dissimilar metal joining is required.
5. Weld Strength Analysis: Plastic Limit Load and Fracture Mechanics
Ensuring welded joint integrity under load is a fundamental concern. Alexandrov introduces plastic limit load solutions for undermatched welds, offering insights into structural safety margins when weld metal is weaker than the base metal. This complements the fracture and fatigue studies by Cicero and Gutiérrez-Solana, who emphasize the significance of crack initiation and propagation in long-term service. Their work guides the engineering design of critical components, especially in bridges, ships, and offshore platforms.
6. Laser Welding for Plastics and Metal-Matrix Composites
Laser Transmission Welding (LTW), explored by Acherjee and co-authors, has opened up new avenues for plastic joining, especially in electronics and medical device manufacturing. It offers non-contact, high-speed joining with minimal thermal distortion. In parallel, Guo and Tam delve into Nd:YAG laser welding of SiCp/A356 composites, revealing how in-situ reactions can enhance bonding and microstructure, addressing challenges associated with welding particle-reinforced metal matrix composites.
7. Residual Stress and Weld Integrity
Residual stress is an inevitable consequence of welding due to localized heating and cooling. The evolution of these stresses, particularly under complex loading like four-point bending, impacts fatigue life and structural reliability. Advanced characterization techniques such as X-ray diffraction, neutron diffraction, and finite element modeling are employed to predict and manage these stresses effectively.
Conclusion & Book⬇️
The diversity of welding processes—from EBW to FSW and laser welding—shows that no single technique suits all applications. Each process comes with its own quality control challenges and optimization strategies. The integration of automation, advanced modeling, and new materials expands the scope of welding into previously unattainable domains. As manufacturing advances, a multidisciplinary understanding of welding—encompassing physics, materials science, and engineering—is essential for producing reliable and high-performance structures.