Introduction to Cavitation in Turbo Pumps
Imagine this: You’re running a powerful turbo pump, everything seems fine, and then suddenly—loud noises, vibrations, and a drop in performance. What just happened? Welcome to the world of cavitation, a silent killer in turbopump systems and centrifugal pumps.
What is Cavitation?
Cavitation is like the “boiling” of a liquid at low pressure. When the liquid pressure in a pump drops below its vapor pressure, vapor bubbles form, these bubbles then collapse violently when they move into higher-pressure zones. This collapsing releases shockwaves that can literally chew away the metal.
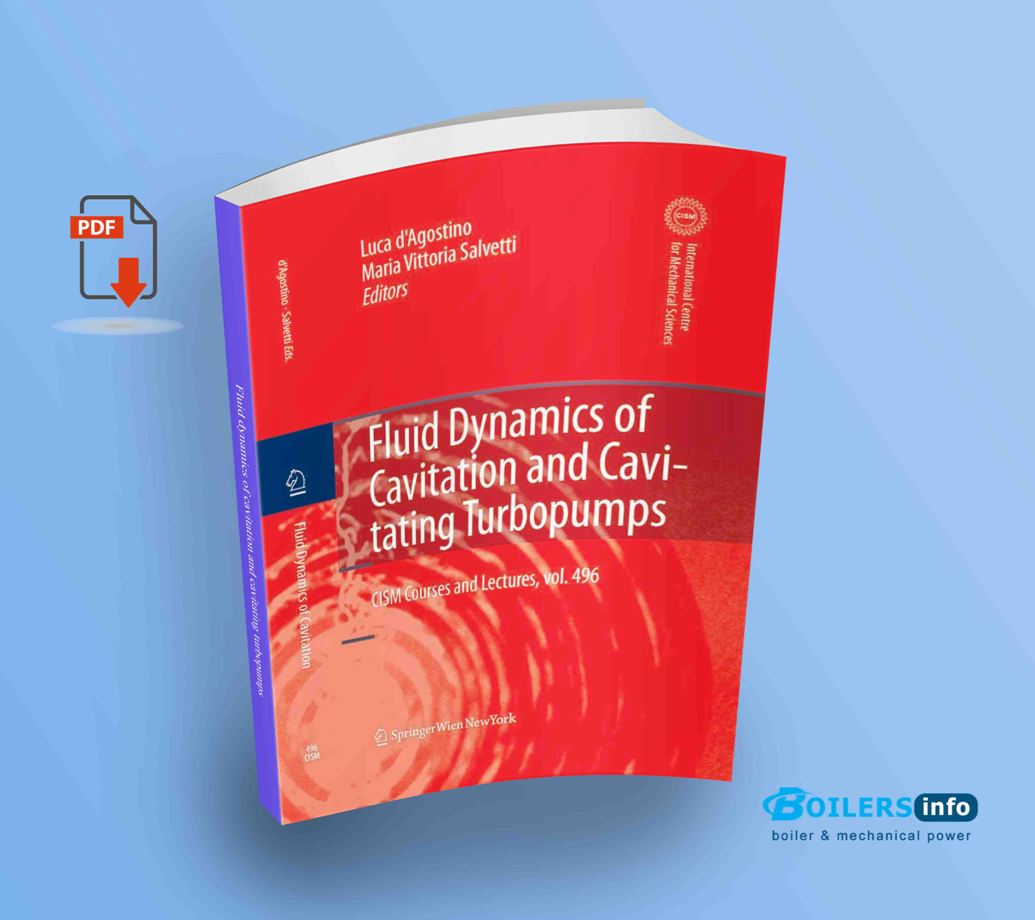
The Importance of Understanding Cavitation in Turbo Pumps
Ignoring cavitation is like ignoring termites in your house—it might not seem urgent until it’s too late. Cavitation can lead to severe equipment damage, efficiency loss, and even catastrophic failure.
Fundamentals of Turbo Pumps
To understand cavitation, you first need to grasp how turbo pumps work.
How Turbo Pumps Work
Turbo pumps use rotating impellers to increase the pressure and velocity of liquids. They are commonly used in industries like oil and gas, aerospace, and power generation.
Key Components of Turbo Pumps
- Impeller: Moves the liquid.
- Casing: Contains the fluid.
- Shaft and Bearings: Support the rotation.
- Turbopumps and Pumping Systems
What Causes Cavitation in Turbo Pumps?
Cavitation doesn’t happen by accident—specific conditions trigger it.
Pressure Variations
Low-pressure zones inside the pump create the perfect environment for bubble formation.
Vapor Pressure and Liquid Boiling
Every liquid has a boiling point, and under lower pressures, that boiling point drops.
Pump Design and Operating Conditions
Poor design, improper flow rates, and extreme operating conditions increase the risk.
Types of Cavitation
Cavitation isn’t one-size-fits-all. There are several types:
Vaporous Cavitation
Classic cavitation caused by liquid turning into vapor.
Gaseous Cavitation
Gas, not vapor, forms bubbles—often due to dissolved gases coming out of the solution.
Vortex Cavitation
Formed by swirling fluids creating low-pressure vortices.
Transient Cavitation
Short-lived but can still cause damage.
Signs and Symptoms of Cavitation
How do you know if cavitation is happening? Here are the telltale signs:
Noise and Vibration
It often sounds like gravel or marbles rattling inside the pump.
Decreased Pump Performance
Lower flow rates and reduced head pressure.
Physical Damage to Components
Pitting, erosion, and material loss on impellers and casings.
Effects of Cavitation on Turbo Pumps
The consequences are brutal if cavitation is left unchecked.
Erosion and Pitting
Surface metal gets hammered and eroded, creating holes.
Mechanical Failure
Bearings, seals, and shafts can fail due to the vibrations.
Reduced Efficiency and Downtime
More energy wasted, more downtime, more money lost.
How to Detect Cavitation
Early detection is key to avoiding costly repairs.
Visual Inspections
Look for signs of wear, pitting, or corrosion.
Acoustic Monitoring
Use ultrasonic sensors to pick up the distinct noise of cavitation.
Performance Testing
Measure flow rates, pressures, and temperatures regularly.
Preventing Cavitation in Turbo Pumps
Good news—cavitation can be prevented with the right approach.
Proper Pump Selection
Make sure the pump is suited for the application.
Correct Operating Conditions
Maintain flow rates and pressures within safe ranges.
Use of Inducers and Design Modifications
Inducers lower the suction pressure, reducing cavitation risk.
Advanced Techniques for Cavitation Control
Going beyond the basics with modern tools.
Computational Fluid Dynamics (CFD)
Simulates fluid behavior to identify risk zones.
Material Selection and Coatings
Use cavitation-resistant materials like stainless steel or apply protective coatings.
Condition Monitoring Systems
AI-driven sensors can predict cavitation before it happens.
Real-Life Case Studies of Cavitation in Turbo Pumps
Industrial Example 1: Chemical Plant Failure
A major chemical facility faced pump breakdowns every six months due to cavitation. After redesigning the suction piping and changing impellers, the problem vanished.
Industrial Example 2: Power Plant Success Story
A thermal power plant reduced cavitation incidents by 80% by installing variable frequency drives and upgrading pump materials.
Maintenance Strategies to Avoid Cavitation
Prevention is better than cure—especially when it comes to cavitation.
Routine Inspections
Regular checks can catch early signs of damage.
Predictive Maintenance
Using AI-based tools to forecast problems.
Staff Training
Equip your team with the knowledge to spot and stop cavitation.
Cost Implications of Cavitation Damage
Cavitation doesn’t just cost you in repairs.
Direct Costs
Repairs, parts replacement, and downtime.
Indirect Costs
Production losses, safety risks, and environmental fines.
Environmental Impacts of Cavitation
Cavitation can have a darker side.
Fluid Leaks and Contamination
Damaged pumps can leak hazardous fluids.
Energy Waste
Inefficient pumps consume more energy, increasing your carbon footprint.
Future Trends in Cavitation Prevention
Where is the industry heading?
Smart Pumps
Self-regulating pumps that adjust flow automatically.
AI and IoT Integration
Real-time monitoring and predictive maintenance powered by artificial intelligence.
Conclusion & Book
Cavitation in turbo pumps is like a hidden enemy—quiet at first, but capable of wreaking havoc if ignored. By understanding the causes, effects, and prevention strategies, industries can protect their equipment, save costs, and boost efficiency. The future holds promise with smart technology leading the way. So, the next time your pump makes that odd noise—don’t ignore it!
FAQs
Q1: What is the main cause of cavitation in turbo pumps?
A: Low-pressure zones inside the pump causing the liquid to vaporize.
Q2: How can you tell if cavitation is occurring?
A: Unusual noises, vibration, and decreased performance are the key signs.
Q3: Can cavitation be completely prevented?
A: While it can’t always be eliminated, proper design, monitoring, and maintenance can greatly reduce the risk.
Q4: Does cavitation only happen in high-speed pumps?
A: No, cavitation can occur in both high and low-speed pumps depending on conditions.
Q5: What is the most effective way to monitor cavitation?
A: Acoustic monitoring, combined with real-time performance data, offers the most effective detection method.