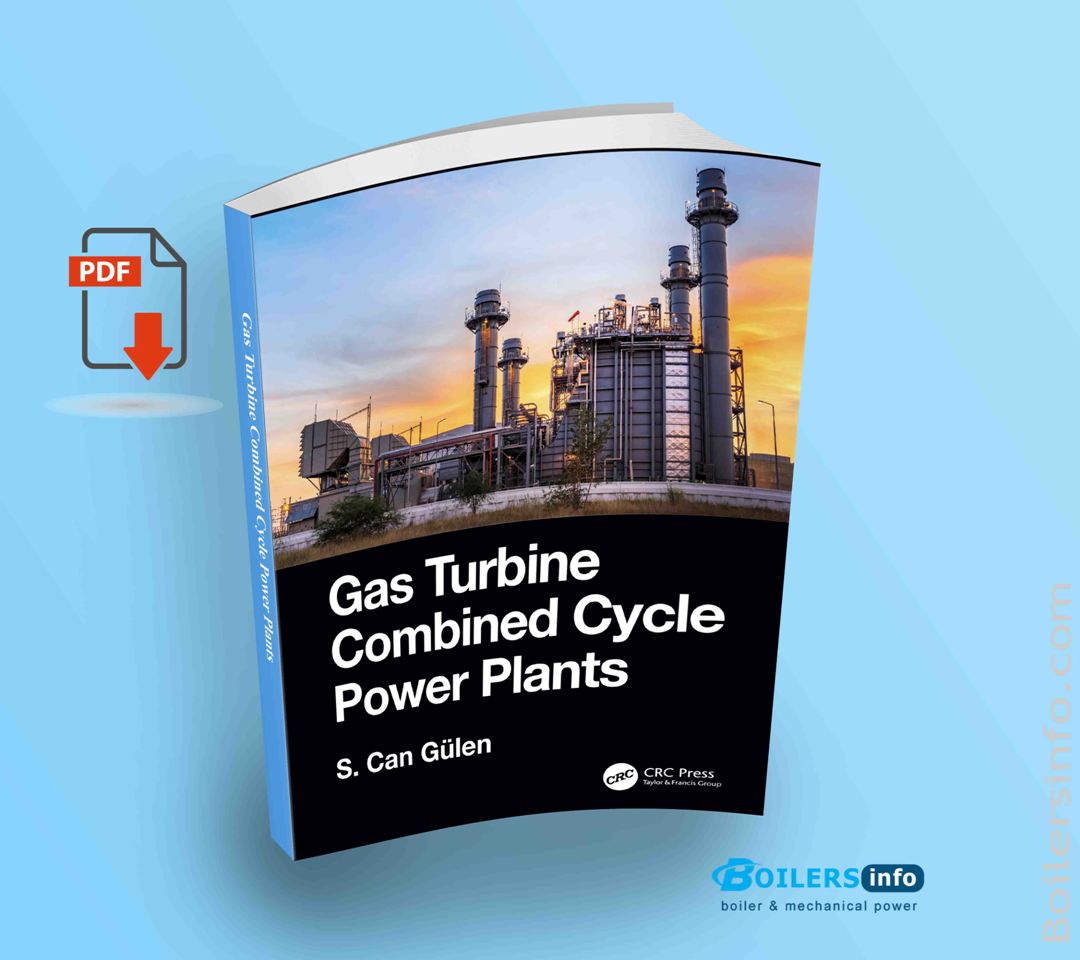
Gas Turbine Combined Cycle Power Plants: A Comprehensive Overview
Introduction
Gas Turbine Combined Cycle (GTCC) power plants represent a high-efficiency solution to modern power generation needs. By blending the strengths of both gas and steam turbines in a single system, they achieve thermal efficiencies exceeding 60%, significantly reducing fuel consumption and greenhouse gas emissions compared to traditional fossil-fuel plants.
Prerequisites for Development
Developing a GTCC plant requires careful consideration of site conditions, including fuel availability (primarily natural gas), access to water, grid connectivity, and environmental regulations. A feasibility assessment covering logistics, resource stability, and community impact is a critical first step in project planning.
Essential Infrastructure
Every GTCC facility relies on certain fundamental components: a stable fuel supply chain, robust electrical interconnection, effective water treatment systems, and skilled operational personnel. Without these bare necessities, even the most advanced plant designs cannot function reliably.
Gas Turbine: The Powerhouse
At the heart of the GTCC plant lies the gas turbine. Operating on the Brayton cycle, it compresses air, mixes it with fuel, ignites the mixture, and drives a turbine to generate electricity. Advances in materials, cooling technology, and combustion design have led to turbines that are not only powerful but also highly fuel-efficient and environmentally friendly.
Steam Turbine: Secondary Efficiency
The steam turbine captures and converts the waste heat from the gas turbine’s exhaust to generate additional power. This second stage, based on the Rankine cycle, is what elevates GTCC efficiency well above that of simple-cycle gas plants.
Heat Recovery Steam Generator (HRSG)
The HRSG acts as the thermal bridge between the gas and steam systems. It captures the hot exhaust gases from the gas turbine and uses them to produce steam for the steam turbine. Multi-pressure HRSG designs with reheaters and duct burners offer flexibility and increased performance.
Heat Rejection Systems
The steam cycle requires a heat sink to condense the exhaust steam. Options include air-cooled condensers, wet cooling towers, or hybrid systems. The selection depends on water availability, ambient temperature, and environmental constraints.
System Integration
Bringing together the gas turbine, HRSG, and steam turbine into a fully functioning power block requires precise mechanical, thermal, and control integration. The synchronization of rotating machinery, steam parameters, and load demand ensures seamless operation and maximized output.
Key Equipment Components
Major equipment in a GTCC plant includes not just turbines and HRSGs, but also electrical generators, transformers, condensers, and control systems. Each piece plays a vital role in ensuring the plant’s safety, reliability, and performance under various load conditions.
Supporting Systems (Balance of Plant)
Balance of Plant refers to the auxiliary systems required for smooth operation. These include water treatment, lubrication systems, fuel handling, HVAC, power distribution, and instrumentation. Optimizing these systems is essential for minimizing downtime and operating costs.
Construction and Start-Up
GTCC plant construction follows a modular and phased approach. It involves heavy lifting, structural assembly, system piping, and electrical integration. Commissioning includes rigorous cold and hot testing, synchronization with the grid, and fine-tuning for performance guarantees.
Environmental Responsibility
One of GTCC’s major advantages is its lower environmental footprint. These plants emit less CO₂, NOₓ, and particulate matter compared to coal-fired plants. Environmental assessments, emissions monitoring, and water conservation strategies are integral to plant design and operation.
Cost and Financial Considerations
While initial investment is substantial, the long-term operational savings due to high efficiency and low fuel usage make GTCC plants economically viable. Flexible operation also allows them to complement intermittent renewable energy sources, improving grid stability and revenue potential.
Cogeneration Applications
In cogeneration mode, GTCC plants can supply both electricity and useful heat (for industrial processes or district heating), dramatically increasing overall efficiency. This makes them ideal for industrial parks, chemical plants, and large urban developments.
Operational Flexibility
Modern GTCC facilities are designed to handle frequent starts and stops, fast load changes, and variable grid demands. With digital control systems and real-time diagnostics, operators can ensure both performance and safety under all operating conditions.
Maintenance Practices
Gas turbines require periodic inspection and replacement of hot-path components. HRSGs and steam turbines also demand regular maintenance to prevent corrosion, scaling, and mechanical wear. Condition-based maintenance and digital twins are now being used to predict failures before they occur.
Plant Repowering Opportunities
Older steam plants can be repowered by adding a gas turbine and HRSG, thereby converting them into GTCC units. This significantly improves efficiency, reduces emissions, and extends asset life—offering a cost-effective alternative to decommissioning.
Integrated Gasification Combined Cycle (IGCC)
IGCC plants combine coal gasification with GTCC technology, allowing solid fuels to be used more cleanly. Despite their complexity and cost, IGCC systems show promise for regions with coal resources but strict emission regulations.
Carbon Capture and the Path Forward
Carbon capture technologies can be integrated into GTCC plants to curb CO₂ emissions, aligning with global decarbonization goals. While current costs are high, ongoing innovation in solvent systems and process integration is steadily improving feasibility.