Turbines, Compressors, and Fans: Principles and Applications
Turbomachinery is fundamental in converting energy between fluid and mechanical forms. Whether it’s producing electricity, driving industrial processes, or powering aircraft, turbines, compressors, and fans play critical roles across industries. This article explores their design, operation, and integration in energy systems, drawing insights from thermodynamics, fluid mechanics, and modern plant configurations.
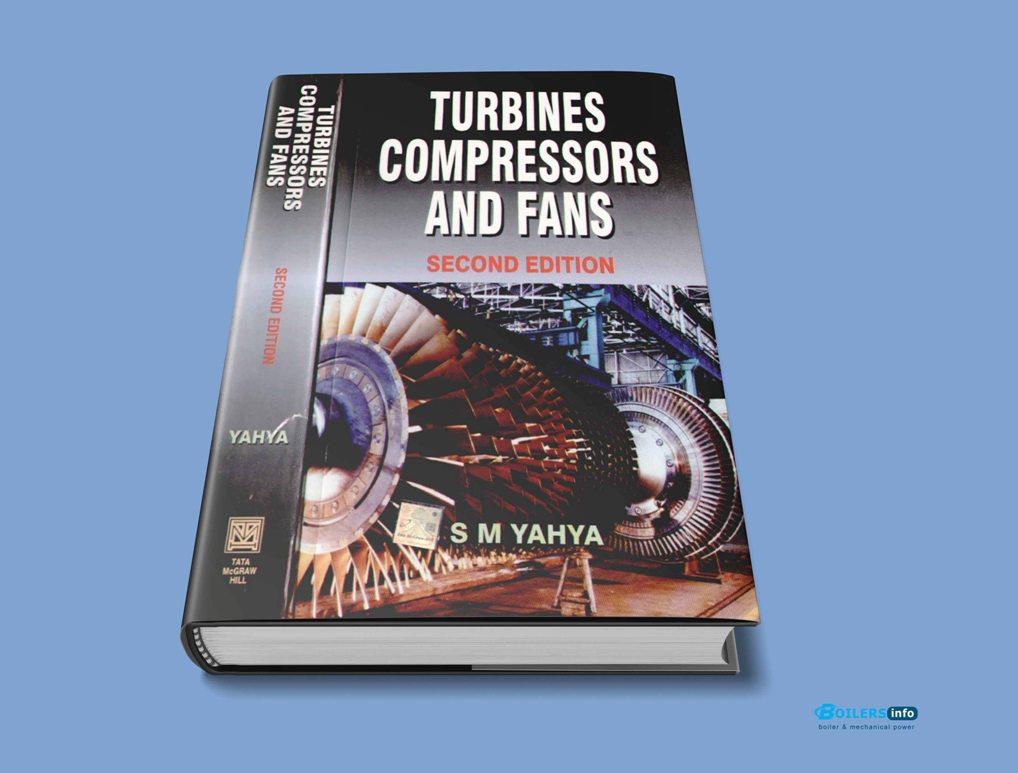
Thermodynamics and Turbomachinery
At the core of all turbomachinery lies the application of thermodynamics. Key principles include:
- First Law (Energy Conservation): Used to track energy flow through turbines and compressors.
- Second Law (Entropy and Efficiency): Defines the theoretical efficiency and guides design improvements.
- Cycle Analysis: Brayton and Rankine cycles are foundational for gas and steam turbines.
- Thermodynamics Combustion, and Engines
Gas Turbine Plants
Gas turbines are widely used in aviation, power generation, and mechanical drive applications. They operate on the Brayton cycle and typically include:
- Compressor → Combustion Chamber → Turbine
- High power-to-weight ratio
- Rapid start-up time
- Advanced cooling and material technologies for high-temperature operations
Steam Turbine Plants
Steam turbines convert thermal energy from high-pressure steam into mechanical work. Key features include:
- Multi-stage expansion for efficiency
- Use in thermal and nuclear power plants
- Requires complex piping, condensers, and feedwater systems
Combined Cycle Plants (CCPP)
CCPPs combine gas and steam turbines to improve efficiency:
- The gas turbine produces electricity and its exhaust heats water to drive a steam turbine.
- Typical efficiency: 55–62%, higher than standalone cycles
- Ideal for large-scale power generation with lower emissions
- Combined Cycle Gas And Steam Turbine Power Plants
Fluid Dynamics in Turbomachinery
Fluid dynamics governs the flow behavior inside turbines, compressors, and fans. Essential concepts include:
- Continuity, momentum, and energy equations
- Boundary layers and flow separation
- Shock waves and compressibility effects in high-speed flows
Dimensional Analysis and Performance Parameters
Understanding performance requires dimensionless numbers such as:
- Reynolds Number: Characterizes flow regime
- Mach Number: Indicates compressibility effects
- Specific Speed (Ns): Helps classify turbomachinery and predict performance
Performance maps show efficiency, pressure ratio, and flow behavior under various conditions.
Flow-Through Cascades
Blade rows in turbines and compressors are analyzed using cascades:
- Study of flow across blade passages in 2D or 3D
- Important for evaluating losses, flow angles, and pressure changes
- Cascade testing helps optimize blade profiles
Axial Turbine Stages
Axial turbines are common in jet engines and power plants:
- Consist of stator and rotor blade rows
- Designed for high flow rates and moderate pressure ratios
- Efficiency depends on blade design, clearance, and cooling methods
High Temperature (Cooled) Turbine Stages
To achieve higher thermal efficiency, turbine inlet temperatures must be increased. Cooling methods include:
- Film Cooling
- Internal Air Cooling
- Thermal Barrier Coatings
These innovations extend component life in extreme environments.
Axial Compressor Stages
Axial compressors increase the pressure of incoming air in stages:
- Each stage includes rotating (rotor) and stationary (stator) blades
- Prone to stall and surge if not designed properly
- Found in gas turbines and aero engines for their high efficiency
Centrifugal Compressor Stage
Centrifugal compressors use radial flow to achieve compression:
- Impeller increases kinetic energy
- Diffuser converts velocity into pressure
- Used in small gas turbines, turbochargers, and refrigeration systems
Radial Turbine Stages
Radial turbines are often used in turbochargers and small-scale power generation:
- Compact and robust
- Less sensitive to inlet flow distortion
- Efficient for lower power ranges
Axial Fans and Propellers
Axial fans move air parallel to the shaft:
- Common in ventilation, cooling towers, and aircraft propellers
- High flow rates, but lower pressure rise
- Efficiency affected by blade shape, tip clearance, and speed
Centrifugal Fans and Blowers
Centrifugal fans move air outward through radial impellers:
- Ideal for high-pressure applications
- Used in HVAC, dust collection, and industrial systems
- Easy to maintain and operate
Wind Turbines
Wind turbines convert wind energy into electricity using rotor blades:
- Horizontal-axis wind turbines (HAWT) are most common
- Design includes pitch control, yaw mechanisms, and power electronics
- Challenges: Wind variability, noise, and environmental impacts
Solar Turbine Plants
In solar thermal systems, turbines can be driven by heat from concentrated solar power (CSP):
- Technologies include parabolic troughs, solar towers, and dish systems
- Hybrid systems combine solar and gas turbines
- CSP with thermal storage allows extended operation beyond sunlight hours
- Get Gas Turbines Training Course PDF
📘 If you’d like to explore this topic in more depth, you can download the complete PDF guide for easy reading and future reference.